Chemical Vapor Deposition (CVD) is a sophisticated process used to deposit thin, solid films onto substrates by utilizing gaseous phase materials. This method involves introducing the coating material into a reaction chamber in vapor form, where it reacts or decomposes on the substrate to form a coating. The process requires precise control of temperature, pressure, and gas flow, and is widely used in industries such as electronics, optics, and materials science due to its ability to produce high-quality, uniform coatings with excellent step coverage and repeatability.
Key Points Explained:
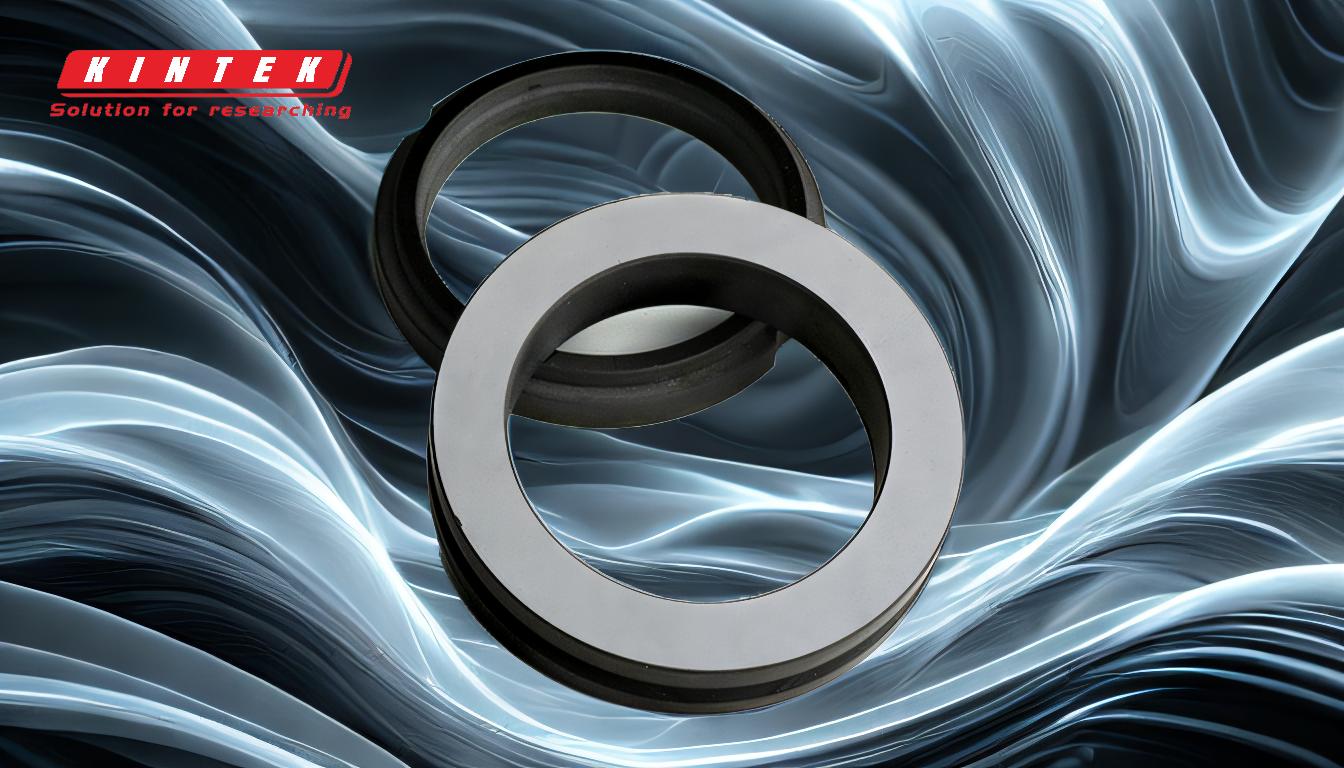
-
Process Overview:
- CVD involves the activation of gaseous reactants, which then undergo a chemical reaction to form a stable solid deposit on a substrate.
- The energy required for the reaction can be supplied by heat, light, or electric discharge, depending on the specific application.
-
Components of CVD:
- Gas Delivery System: Delivers the gaseous reactants to the reaction chamber.
- Reaction Chamber: Where the chemical reaction occurs, typically under vacuum conditions.
- Substrate Loading Mechanism: Ensures the substrate is properly positioned and held during the deposition process.
- Energy Supplier: Provides the necessary energy (heat, light, or electric discharge) to drive the chemical reaction.
-
Steps in CVD Process:
- Ablation: The initial step where the solid material is vaporized.
- Transport: The vaporized material is transported to the substrate.
- Reaction: The gaseous reactants undergo a chemical reaction on the substrate surface.
- Deposition: The resulting solid material forms a thin film on the substrate.
-
Temperature and Pressure Control:
- The substrate temperature is critical for the deposition process, as it affects the rate and quality of the film formation.
- The reaction typically occurs in a vacuum to prevent contamination and ensure uniform deposition.
-
Applications of CVD:
- Electronics: Used for depositing dielectric films (e.g., SiO2, Si3N4) and semiconductor films in integrated circuits, capacitors, and resistors.
- Optics: Produces high-quality optical coatings.
- Materials Science: Creates coatings for wear resistance, corrosion protection, and other functional properties.
-
Advantages of CVD:
- Repeatability: Ensures consistent quality across multiple batches.
- Step Coverage: Provides uniform coating even on complex geometries.
- Versatility: Can deposit a wide range of materials, including metals, semiconductors, and organic compounds.
-
Example of CVD in Diamond Synthesis:
- A thin seed diamond is placed in a sealed chamber and exposed to high temperatures (up to 800°C).
- The chamber is filled with a carbon-rich gas mixture (e.g., hydrogen and methane).
- Ionization breaks the molecular bonds in the gases, allowing pure carbon to adhere to the diamond seed.
- As carbon accumulates, it forms atomic bonds with the seed diamond, creating a new, larger diamond.
-
Environmental Considerations:
- CVD is more environmentally friendly compared to other coating technologies, as it often occurs under vacuum conditions and can be designed to minimize waste.
In summary, CVD is a versatile and precise method for depositing thin films, offering excellent repeatability and step coverage. Its applications span across various industries, making it a crucial technology in modern manufacturing and materials science.
Summary Table:
Aspect | Details |
---|---|
Process Overview | Gaseous reactants form a solid deposit on a substrate via chemical reaction. |
Key Components | Gas delivery system, reaction chamber, substrate loading, energy supplier. |
Steps in CVD Process | Ablation, transport, reaction, deposition. |
Temperature Control | Critical for film quality; typically occurs under vacuum. |
Applications | Electronics, optics, materials science. |
Advantages | Repeatability, step coverage, versatility. |
Discover how CVD coating can transform your manufacturing process—contact us today for expert guidance!