The time required to leave ceramic slip in a mold depends on the desired thickness of the cast and the specific properties of the slip and mold. Generally, for a casting thickness between ? and 1 inch, the slip should remain in the mold for approximately 15-18 minutes. This allows the plaster mold to absorb moisture from the slip, forming a solid layer of clay (greenware) that can be removed without deformation. The exact time may vary based on factors such as slip consistency, mold porosity, and environmental conditions like temperature and humidity.
Key Points Explained:
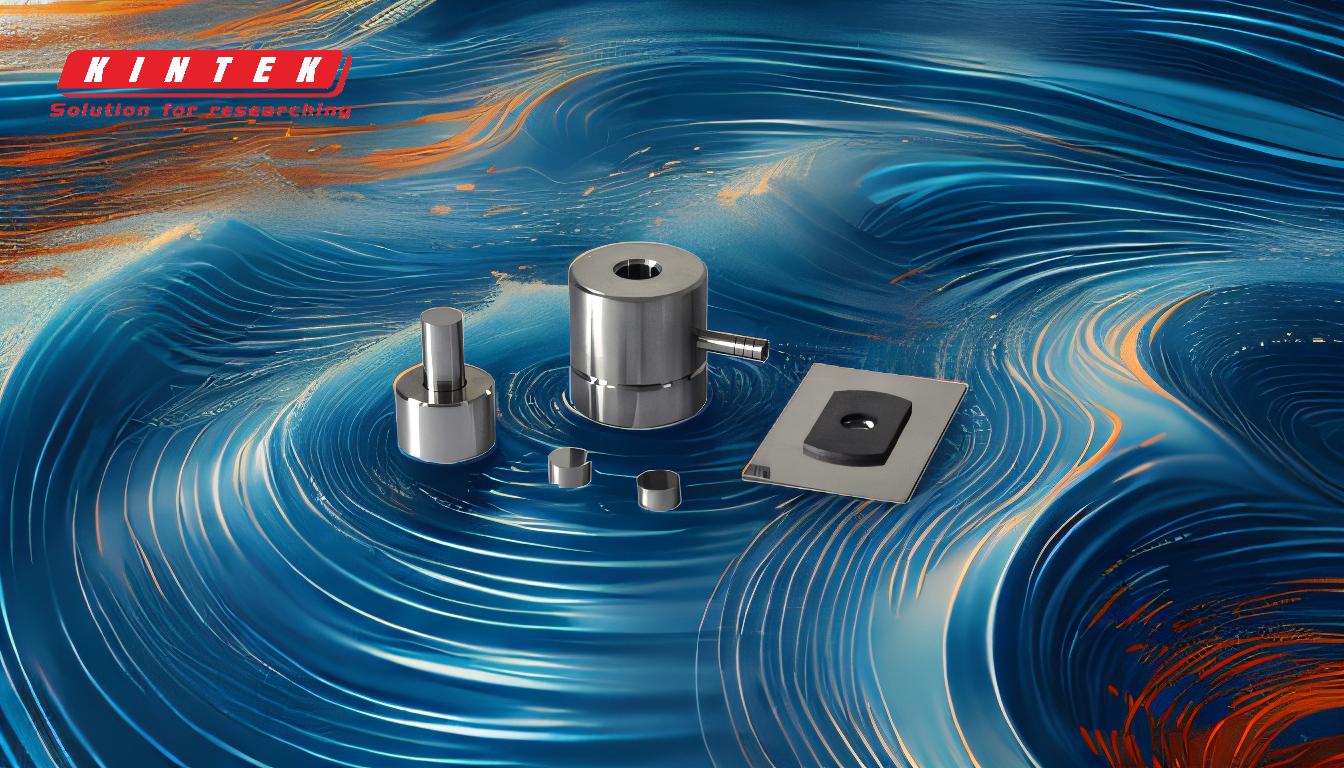
-
Purpose of Leaving Slip in the Mold:
- The primary goal is to allow the plaster mold to absorb water from the slip, creating a solid clay layer. This process is crucial for achieving the desired thickness and structural integrity of the greenware.
-
Typical Time Frame:
- For a casting thickness between ? and 1 inch, the slip should remain in the mold for 15-18 minutes. This duration ensures that the clay layer is sufficiently firm to hold its shape when the mold is opened.
-
Factors Influencing Drying Time:
- Slip Consistency: Thicker slips may require slightly longer drying times, while thinner slips may dry faster.
- Mold Porosity: More porous molds absorb water more quickly, reducing the required drying time.
- Environmental Conditions: Higher temperatures and lower humidity levels can accelerate the drying process, while cooler, more humid conditions may slow it down.
-
Monitoring the Process:
- It's essential to monitor the slip's condition during the casting process. Over-drying can lead to cracks or difficulty in removing the greenware, while under-drying can result in a weak or deformed shape.
-
Removing the Greenware:
- Once the desired thickness is achieved, the mold halves can be separated carefully to remove the greenware. Handling the greenware gently is crucial to avoid damage before it undergoes further drying and firing.
-
Adjustments for Specific Projects:
- For thicker or more intricate designs, the drying time may need to be adjusted. Experimentation and experience with specific materials and molds will help determine the optimal duration for each project.
By understanding these key points, you can effectively manage the slip casting process to produce high-quality ceramic pieces.
Summary Table:
Factor | Impact on Drying Time |
---|---|
Slip Consistency | Thicker slips require longer drying; thinner slips dry faster. |
Mold Porosity | More porous molds absorb water faster, reducing drying time. |
Environmental Conditions | High temperatures and low humidity speed up drying; cooler, humid conditions slow it down. |
Need help perfecting your ceramic slip casting process? Contact our experts today for tailored advice!