DLC (Diamond-Like Carbon) coatings are known for their exceptional hardness, low friction, and wear resistance, making them a popular choice for various industrial applications. The lifespan of a DLC coating depends on several factors, including the application environment, the substrate material, and the specific type of DLC coating used. Generally, DLC coatings can last for several years under normal operating conditions, but this can vary significantly based on the intensity of use and the presence of abrasive or corrosive elements. The durability of DLC coatings is often compared to other advanced coating technologies like CVD (Chemical Vapor Deposition) and PVD (Physical Vapor Deposition), which also offer high levels of protection but differ in their application methods and material properties.
Key Points Explained:
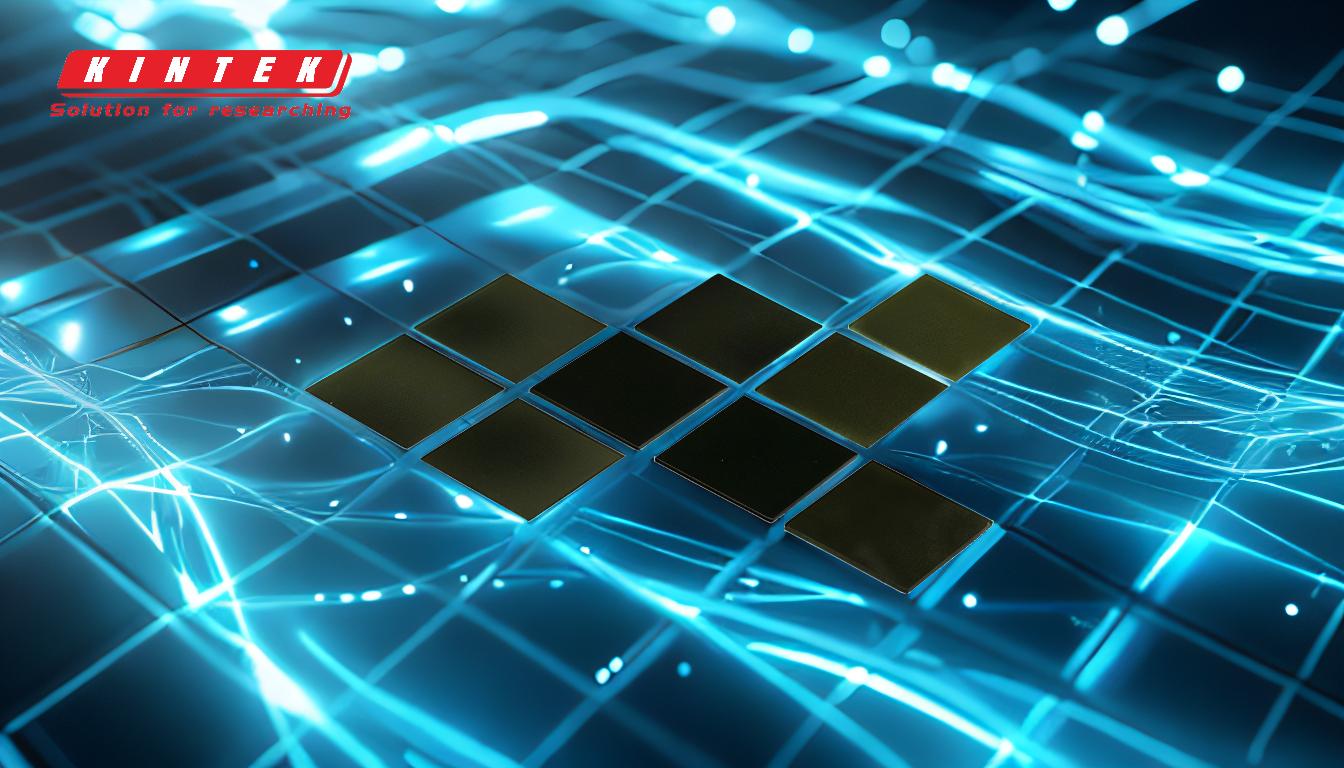
-
Durability and Lifespan of DLC Coatings:
- DLC coatings are renowned for their hardness and wear resistance, which contribute to their long lifespan. In typical applications, such as automotive components or cutting tools, DLC coatings can last for several years before showing significant wear.
- The exact lifespan depends on the operating conditions. For example, in high-stress environments with constant friction or exposure to corrosive substances, the coating may degrade faster.
-
Comparison with CVD and PVD Coatings:
- CVD Coatings: These coatings are known for forming a hard and robust layer that enhances durability and resistance to stains. They are often used in applications where extreme durability is required, such as in the glass industry. However, CVD coatings are generally thicker than DLC coatings, which can affect the flexibility and precision of the coated part.
- PVD Coatings: PVD coatings are extremely thin, allowing the product to retain its original shape while providing excellent corrosion resistance and temperature stability. They are often used in decorative applications and in environments where maintaining the original dimensions of the part is crucial. PVD coatings are also highly resistant to abrasion, which can contribute to a longer lifespan in certain applications.
-
Factors Affecting Coating Lifespan:
- Application Environment: The presence of abrasive particles, corrosive chemicals, or extreme temperatures can accelerate the wear of DLC coatings.
- Substrate Material: The material being coated can also affect the longevity of the DLC coating. For example, coatings on softer materials may wear out faster due to the substrate's inability to support the coating under stress.
- Coating Thickness and Quality: The thickness and quality of the DLC coating itself play a significant role in its durability. Thicker coatings may offer better protection but could also be more prone to cracking under stress.
-
Maintenance and Care:
- Proper maintenance can extend the life of DLC coatings. Regular cleaning to remove abrasive particles and avoiding exposure to harsh chemicals can help maintain the coating's integrity.
- In some cases, reapplication of the coating may be necessary after several years of use, depending on the wear and tear experienced.
In summary, DLC coatings are highly durable and can last for several years under normal conditions. However, their lifespan can be influenced by the application environment, substrate material, and the quality of the coating itself. Comparing DLC with other coating technologies like CVD and PVD highlights the unique advantages and limitations of each, helping users choose the most appropriate coating for their specific needs.
Summary Table:
Aspect | Details |
---|---|
Lifespan | Several years under normal conditions; varies with use and environment. |
Key Factors | Application environment, substrate material, coating thickness, and quality. |
Comparison with CVD | Thicker, less flexible, ideal for extreme durability. |
Comparison with PVD | Thinner, retains part dimensions, excellent for corrosion resistance. |
Maintenance Tips | Regular cleaning, avoid harsh chemicals, reapply as needed. |
Need help choosing the right coating for your application? Contact our experts today!