Magnetron sputtering is a distinct physical vapor deposition (PVD) technique that differs significantly from other sputtering methods and evaporation-based processes like electron beam deposition (E-Beam). Unlike E-Beam, which relies on heating or electron-beam bombardment to vaporize materials, magnetron sputtering uses a plasma to physically dislodge atoms from a target material, which then deposit onto a substrate. This method does not require melting or evaporation, making it suitable for a wider range of materials, including alloys and ceramics. Additionally, magnetron sputtering offers advantages such as precise control over film composition, uniform thickness, and high deposition rates, making it ideal for industrial applications and exotic material experimentation.
Key Points Explained:
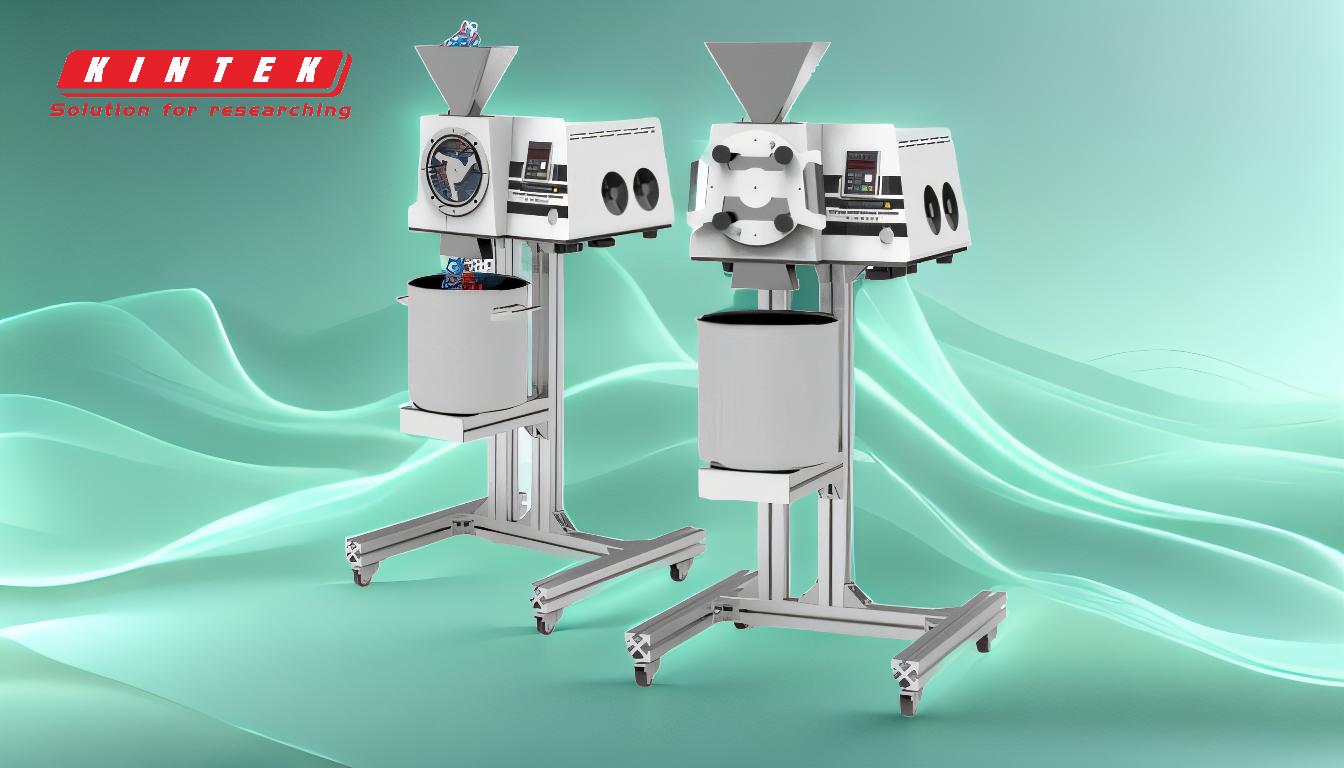
-
Mechanism of Material Deposition:
- Magnetron Sputtering: Utilizes a plasma generated by a magnetic field to bombard a target material, freeing atoms that deposit onto a substrate. This process does not require the target material to be melted or vaporized, allowing for the deposition of a wide range of materials, including alloys and ceramics.
- E-Beam Deposition: Relies on heating or electron-beam bombardment to vaporize source materials, which then condense onto a substrate. This method is simpler and faster for batch processing but is limited to materials that can be easily vaporized.
-
Temperature Requirements:
- Magnetron Sputtering: Operates at lower temperatures compared to evaporation-based methods, making it suitable for coating temperature-sensitive materials like plastics, organics, and glass.
- E-Beam Deposition: Requires higher temperatures to vaporize materials, which can limit its application to substrates that can withstand these conditions.
-
Material Versatility:
- Magnetron Sputtering: Can deposit a wide variety of materials, including metals, alloys, and ceramics. It also allows for the co-sputtering of multiple targets to create precise alloy compositions and the addition of reactive gases to deposit compound films.
- E-Beam Deposition: Primarily used for simpler materials and is less versatile in terms of the types of coatings it can produce.
-
Film Quality and Precision:
- Magnetron Sputtering: Produces dense, uniform films with excellent adhesion and precise control over thickness. This makes it ideal for high-precision applications and industrial-scale production.
- E-Beam Deposition: While it can produce high-quality coatings, it may not offer the same level of precision and uniformity as magnetron sputtering, especially for complex materials.
-
Industrial Applications:
- Magnetron Sputtering: Highly suitable for high-volume, high-efficiency industrial production due to its fast coating rates and ability to produce dense, adherent films. It is often the preferred method for depositing coatings of industrial interest.
- E-Beam Deposition: More commonly used in scenarios where simplicity and speed are prioritized over material versatility and precision.
In summary, magnetron sputtering stands out for its ability to deposit a wide range of materials at lower temperatures, with high precision and uniformity, making it a versatile and efficient choice for both experimental and industrial applications. In contrast, E-Beam deposition is simpler and faster but is limited in material versatility and precision.
Summary Table:
Aspect | Magnetron Sputtering | E-Beam Deposition |
---|---|---|
Mechanism | Uses plasma to dislodge atoms; no melting or evaporation required. | Relies on heating or electron-beam bombardment to vaporize materials. |
Temperature | Operates at lower temperatures, suitable for sensitive materials. | Requires higher temperatures, limiting substrate compatibility. |
Material Versatility | Deposits metals, alloys, ceramics, and compound films. | Limited to simpler materials that can be easily vaporized. |
Film Quality | Produces dense, uniform films with precise thickness control. | High-quality coatings but less precise for complex materials. |
Industrial Applications | Ideal for high-volume, high-efficiency production with fast coating rates. | Preferred for simpler, faster batch processing. |
Learn how magnetron sputtering can enhance your material deposition process—contact us today for expert advice!