The cost of establishing a biochar production facility can vary significantly depending on factors such as scale, technology, feedstock, and location. While the reference provided does not directly address the cost of setting up a facility, it does offer insights into the economics of biochar production, which can help estimate the investment required. Based on the reference, biochar production costs are approximately $230 per ton, and the market price is around $1,000 per ton. These figures suggest a profitable margin, but the initial capital expenditure for the facility must also be considered. Below, we break down the key factors influencing the cost of a biochar production facility and provide a detailed analysis.
Key Points Explained:
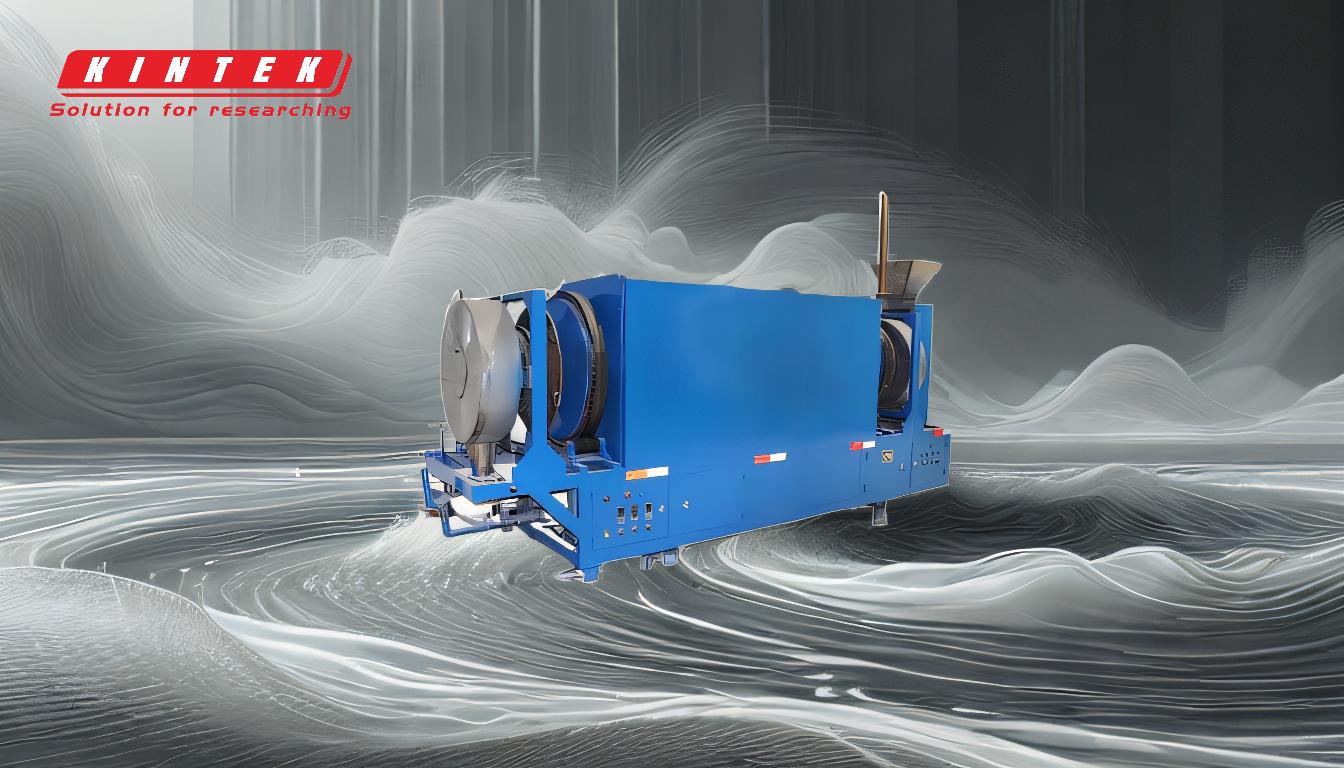
-
Scale of the Facility
- The size of the biochar production facility is a primary determinant of cost.
- Small-scale facilities: These are typically modular and can cost between $50,000 and $200,000. They are suitable for localized operations and have lower throughput.
- Medium-scale facilities: These require more advanced equipment and infrastructure, with costs ranging from $200,000 to $1 million.
- Large-scale facilities: These are industrial-grade operations and can cost upwards of $1 million to $5 million or more, depending on capacity and automation levels.
- The size of the biochar production facility is a primary determinant of cost.
-
Technology and Equipment
- The type of pyrolysis technology used significantly impacts costs.
- Batch pyrolysis systems: These are cheaper but less efficient, with costs ranging from $50,000 to $300,000.
- Continuous pyrolysis systems: These are more efficient and scalable but cost between $300,000 and $2 million.
- Advanced systems with gas capture and energy recovery: These systems are more expensive but can offset costs by generating additional revenue streams from syngas or heat.
- The type of pyrolysis technology used significantly impacts costs.
-
Feedstock Availability and Cost
- The type and availability of feedstock influence both operational and capital costs.
- Agricultural waste, forestry residues, and municipal green waste are common feedstocks.
- If feedstock is abundant and locally available, transportation and storage costs are minimized.
- Feedstock processing equipment (e.g., chippers, grinders) can add $20,000 to $100,000 to the initial investment.
- The type and availability of feedstock influence both operational and capital costs.
-
Location and Infrastructure
- The cost of land, permits, and infrastructure varies by region.
- Rural areas with low land costs and proximity to feedstock sources are ideal.
- Urban or industrial zones may require additional permits and compliance with environmental regulations, increasing costs.
- Infrastructure such as access roads, utilities, and storage facilities can add $50,000 to $200,000 to the total cost.
- The cost of land, permits, and infrastructure varies by region.
-
Labor and Operational Costs
- Labor costs depend on the level of automation and local wage rates.
- Small-scale facilities may require 2-5 workers, while large-scale operations may need 10-20 employees.
- Automation reduces labor costs but increases upfront capital expenditure.
- Labor costs depend on the level of automation and local wage rates.
-
Revenue and Profitability Considerations
- While the reference indicates a production cost of $230 per ton and a market price of $1,000 per ton, the profitability of the facility depends on:
- Throughput capacity (tons per year).
- Operational efficiency and downtime.
- Additional revenue streams (e.g., syngas, heat, carbon credits).
- A facility producing 1,000 tons annually could generate $770,000 in gross profit ($1,000 - $230 = $770 per ton), but this must cover operational and capital costs.
- While the reference indicates a production cost of $230 per ton and a market price of $1,000 per ton, the profitability of the facility depends on:
-
Environmental and Regulatory Compliance
- Compliance with environmental regulations can add to the cost.
- Emissions control systems may cost $50,000 to $200,000.
- Permitting and licensing fees vary by jurisdiction.
- Compliance with environmental regulations can add to the cost.
-
Maintenance and Long-Term Costs
- Maintenance costs for pyrolysis equipment and feedstock processing machinery should be factored in.
- Annual maintenance costs can range from 5% to 10% of the initial equipment cost.
- Replacement parts and upgrades may add $10,000 to $50,000 annually.
- Maintenance costs for pyrolysis equipment and feedstock processing machinery should be factored in.
In summary, the cost of a biochar production facility depends on multiple factors, including scale, technology, feedstock, location, and compliance requirements. Small-scale facilities can be established for as little as $50,000, while large-scale industrial operations may require investments of $1 million or more. The reference highlights the profitability potential of biochar production, with a significant margin between production costs and market prices. However, careful planning and analysis are essential to ensure that the facility meets both operational and financial goals.
Summary Table:
Factor | Cost Range |
---|---|
Small-scale facilities | $50,000 - $200,000 |
Medium-scale facilities | $200,000 - $1 million |
Large-scale facilities | $1 million - $5 million+ |
Batch pyrolysis systems | $50,000 - $300,000 |
Continuous pyrolysis systems | $300,000 - $2 million |
Feedstock processing equipment | $20,000 - $100,000 |
Infrastructure costs | $50,000 - $200,000 |
Emissions control systems | $50,000 - $200,000 |
Annual maintenance costs | 5% - 10% of equipment cost |
Ready to start your biochar production facility? Contact us today for expert guidance and tailored solutions!