Plasma generation in magnetron sputtering is a critical process that enables the deposition of thin films onto substrates. It involves creating a low-pressure environment, introducing a gas like argon, and applying a high voltage to ionize the gas atoms, forming a plasma. The plasma is sustained by a magnetic field, which enhances the ionization process and directs ions toward the target material for sputtering. This process is efficient due to the ionization potential of argon and the use of magnetic fields to confine and guide the plasma.
Key Points Explained:
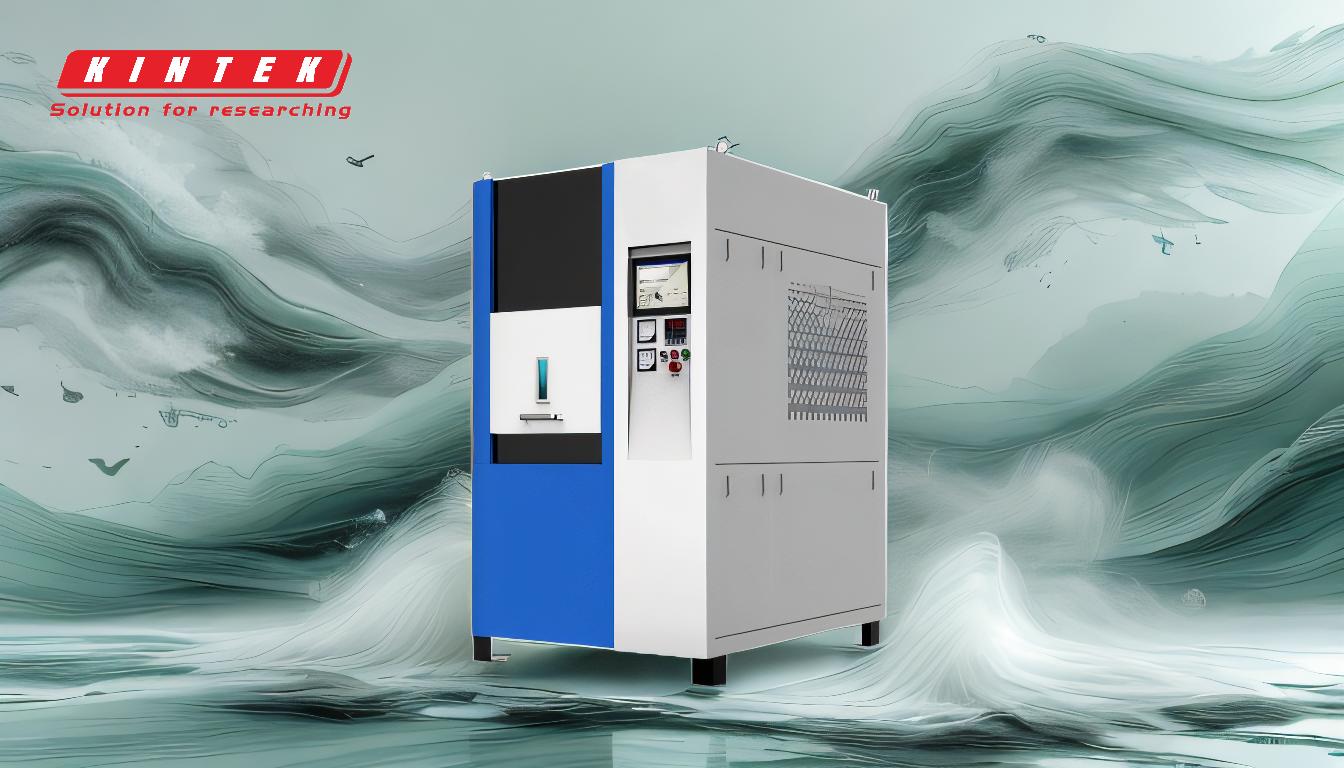
-
Low-Pressure Gas Environment:
- Plasma generation begins by creating a vacuum inside a chamber to reduce the pressure. This low-pressure environment is essential because it minimizes collisions between gas molecules, allowing for easier ionization.
- A gas, typically argon, is introduced into the chamber. Argon is preferred due to its inert nature and relatively low ionization potential (15.8 eV), making it easier to ionize compared to other gases.
-
High Voltage Application:
- A high voltage is applied between the cathode (target material) and the anode. This creates a strong electric field that accelerates free electrons within the gas.
- These high-energy electrons collide with argon atoms, knocking off their outer electrons and ionizing them. This process creates positively charged argon ions and additional free electrons, forming a plasma.
-
Plasma Formation:
- The plasma consists of a mixture of ionized gas atoms, free electrons, and neutral atoms. It is a highly conductive state of matter that sustains the ionization process.
- The plasma is generated in close proximity to the target material, which is the source of the material to be sputtered onto the substrate.
-
Role of Magnetic Fields:
- A magnetic field is generated by a magnet assembly behind the target. This field confines the electrons to spiral along the magnetic field lines, increasing their path length and the likelihood of collisions with gas atoms.
- This confinement enhances the ionization efficiency, leading to a denser and more stable plasma.
-
Ion Bombardment and Sputtering:
- The positively charged argon ions are accelerated toward the negatively charged target material due to the electric field.
- When these ions collide with the target, they dislodge atoms from its surface, a process known as sputtering. These sputtered atoms then deposit onto the substrate, forming a thin film.
-
RF Magnetron Sputtering:
- In some cases, a radio frequency (RF) power supply is used instead of a DC power supply. This is particularly useful for insulating target materials.
- The RF power supply alternates the polarity of the electric field, preventing charge buildup on the target and enabling continuous plasma generation.
-
Advantages of Argon:
- Argon is the most commonly used gas due to its high sputtering yield, inert nature, and cost-effectiveness.
- Its ionization potential is relatively low, making it easier to sustain the plasma compared to other gases.
-
Efficiency and Control:
- The combination of a low-pressure environment, high voltage, and magnetic fields ensures efficient plasma generation and control over the sputtering process.
- This setup allows for precise deposition of thin films with desired properties, making magnetron sputtering a widely used technique in industries such as semiconductor manufacturing, optics, and coatings.
By understanding these key points, one can appreciate the intricate process of plasma generation in magnetron sputtering and its role in enabling high-quality thin film deposition.
Summary Table:
Key Aspect | Description |
---|---|
Low-Pressure Environment | Creates a vacuum to minimize gas molecule collisions, facilitating ionization. |
Argon Gas | Preferred for its inert nature, low ionization potential (15.8 eV), and cost. |
High Voltage Application | Accelerates free electrons to ionize argon atoms, forming plasma. |
Magnetic Fields | Confines electrons, enhancing ionization efficiency and plasma stability. |
Ion Bombardment | Argon ions sputter target atoms, depositing thin films onto substrates. |
RF Magnetron Sputtering | Uses RF power for insulating targets, preventing charge buildup. |
Advantages of Argon | High sputtering yield, inert, cost-effective, and easy to sustain plasma. |
Efficiency & Control | Combines low pressure, high voltage, and magnetic fields for precise deposition. |
Discover how magnetron sputtering can revolutionize your thin film processes—contact our experts today!