Diamond-like carbon (DLC) coatings are renowned for their exceptional strength and durability, making them ideal for wear-protective applications. These coatings exhibit a unique combination of high hardness, low friction, chemical inertness, and smooth surface properties. The strength of DLC coatings stems from their hybrid structure, which includes both diamond-like (Sp3) and graphite-like (Sp2) carbon bonds. This structure allows DLC to provide superior sliding properties, resistance to wear, and performance in harsh environments. Additionally, DLC coatings can be tailored to specific applications by adjusting deposition parameters, ensuring optimal grain size, surface roughness, and crystallinity. Their biocompatibility and resistance to chemicals further expand their utility in various industries.
Key Points Explained:
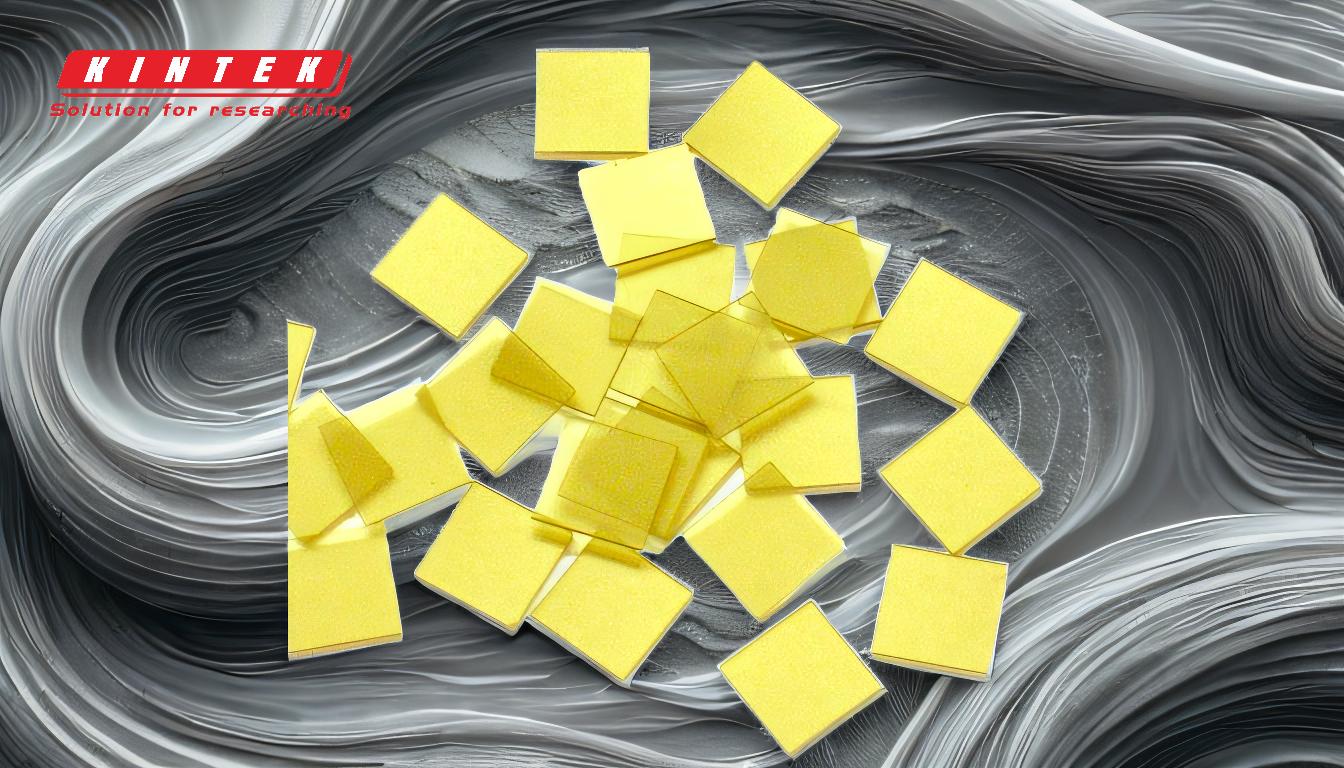
-
High Hardness:
- DLC coatings are extremely hard, often comparable to natural diamond. This hardness is due to the presence of Sp3 (diamond-like) carbon bonds, which provide a robust and wear-resistant surface.
- The high hardness makes DLC coatings ideal for applications where surfaces are subjected to significant mechanical stress, such as in cutting tools, engine components, and industrial machinery.
-
Low Coefficient of Friction:
- DLC coatings exhibit a low coefficient of friction, which reduces wear and tear on moving parts. This property is particularly beneficial in applications involving sliding or rotating components, such as bearings, gears, and pistons.
- The low friction also contributes to energy efficiency by minimizing energy losses due to friction.
-
Chemical Inertness:
- DLC coatings are chemically inert, meaning they do not react with most chemicals. This property makes them suitable for use in corrosive environments, such as in chemical processing equipment or medical devices.
- The chemical inertness also ensures that the coatings remain stable and effective over time, even when exposed to harsh substances.
-
Surface Smoothness:
- The high surface smoothness of DLC coatings reduces friction and wear, further enhancing their durability. Smooth surfaces are less prone to abrasion and can maintain their integrity even under continuous use.
- This smoothness is particularly important in precision applications, such as optical components or medical implants, where surface imperfections can lead to performance issues.
-
Tailorable Properties:
- The properties of DLC coatings, such as grain size, surface roughness, and crystallinity, can be precisely controlled by adjusting deposition parameters and gas phase composition. This allows for customization to meet specific application requirements.
- Tailoring the properties ensures that the coatings provide optimal performance in different environments and for various uses, from industrial machinery to medical devices.
-
Biocompatibility:
- DLC coatings are biocompatible, making them suitable for medical applications. They can be used in implants, surgical instruments, and other medical devices without causing adverse reactions in the body.
- The biocompatibility, combined with the coatings' durability and resistance to wear, makes them an excellent choice for long-term medical applications.
-
Resistance to Wear and Corrosion:
- DLC coatings are highly resistant to wear and corrosion, making them ideal for protective applications. They can withstand harsh conditions, including exposure to abrasive materials, chemicals, and high temperatures.
- This resistance ensures that the coatings maintain their protective properties over extended periods, reducing the need for frequent maintenance or replacement.
-
Applications in Various Industries:
- Due to their unique combination of properties, DLC coatings are used in a wide range of industries, including automotive, aerospace, medical, and manufacturing. They are applied to components such as engine parts, cutting tools, bearings, and optical devices.
- The versatility of DLC coatings makes them a valuable solution for enhancing the performance and longevity of critical components across different sectors.
In summary, DLC coatings are exceptionally strong and durable, offering a range of benefits that make them suitable for diverse applications. Their high hardness, low friction, chemical inertness, and smooth surface properties, combined with the ability to tailor their characteristics, ensure that they provide optimal performance in various environments. Whether used in industrial machinery, medical devices, or precision instruments, DLC coatings deliver superior wear protection and longevity.
Summary Table:
Property | Description |
---|---|
High Hardness | Comparable to natural diamond, ideal for high-stress applications. |
Low Friction | Reduces wear and energy loss in moving parts. |
Chemical Inertness | Resists corrosion and harsh chemicals, ensuring long-term stability. |
Surface Smoothness | Minimizes friction and wear, ideal for precision applications. |
Tailorable Properties | Customizable grain size, roughness, and crystallinity for specific needs. |
Biocompatibility | Safe for medical implants and devices. |
Wear & Corrosion Resistance | Withstands abrasive materials, chemicals, and high temperatures. |
Versatile Applications | Used in automotive, aerospace, medical, and manufacturing industries. |
Enhance your components with DLC coatings—contact us today for tailored solutions!