The pressure of the sputtering gas significantly impacts both the film quality and the sputtering rate in the sputter deposition process. Higher gas pressures cause sputtered ions to collide with gas atoms, leading to a diffusive motion that results in a random walk before deposition. This reduces the energy of the ions, leading to lower sputtering rates but potentially improving film uniformity and coverage. Conversely, lower gas pressures allow for high-energy ballistic impacts, increasing the sputtering rate but potentially compromising film uniformity. The choice of gas pressure is thus a critical parameter that must be optimized based on the desired film properties and deposition efficiency.
Key Points Explained:
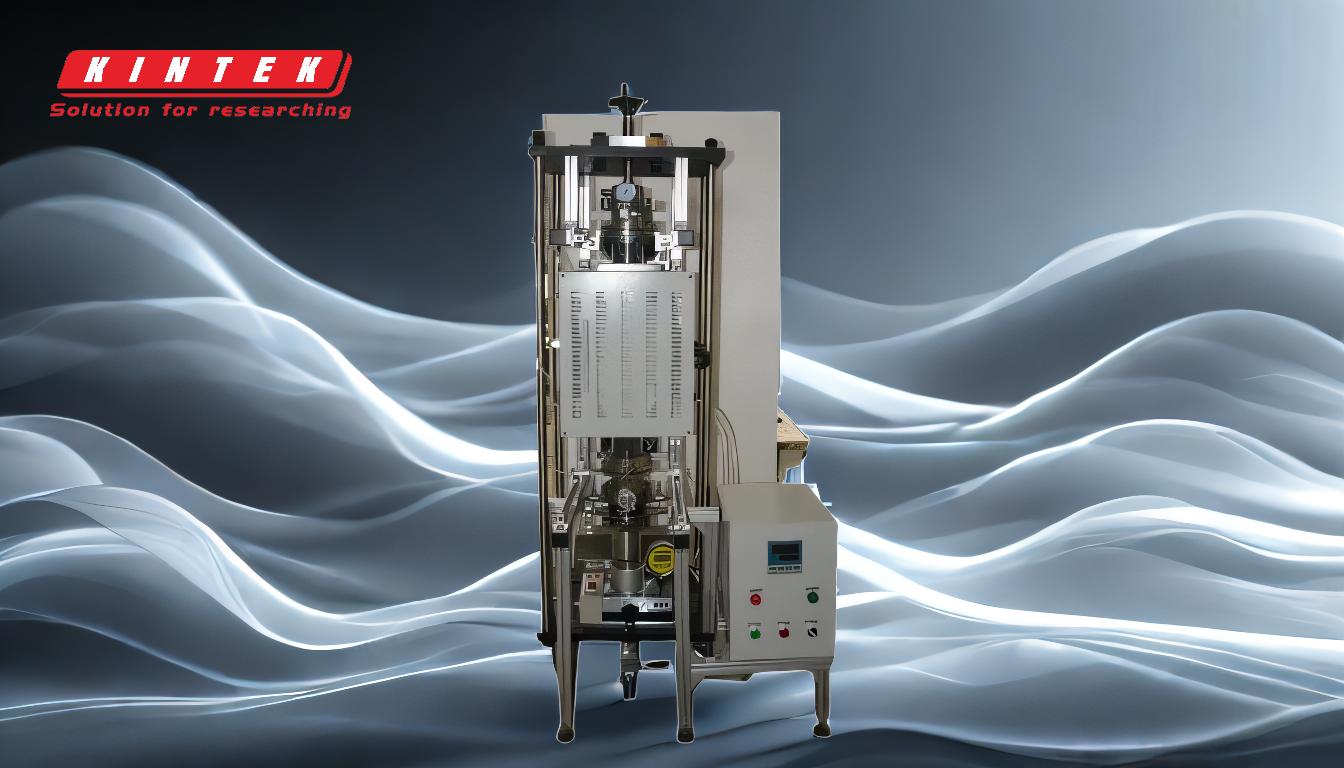
-
Effect of Gas Pressure on Sputtering Rate:
- Higher Gas Pressure: At higher pressures, sputtered ions collide more frequently with gas atoms, which act as moderators. This causes the ions to lose energy and move diffusively, resulting in a slower sputtering rate. The ions undergo a random walk before reaching the substrate, which can reduce the overall deposition rate.
- Lower Gas Pressure: At lower pressures, ions experience fewer collisions with gas atoms, allowing them to travel in a more direct, ballistic path to the substrate. This results in higher energy impacts and a faster sputtering rate, but may lead to less uniform film deposition.
-
Impact on Film Quality:
- Higher Gas Pressure: The diffusive motion of ions at higher pressures can lead to more uniform film coverage, as the ions are more likely to spread out evenly across the substrate. This can improve film quality in terms of uniformity and reduce defects. However, the lower energy of the ions may result in films with lower density and adhesion.
- Lower Gas Pressure: The high-energy ballistic impacts at lower pressures can lead to denser films with better adhesion, but the deposition may be less uniform, potentially leading to variations in film thickness and quality across the substrate.
-
Trade-offs and Optimization:
- Uniformity vs. Density: There is a trade-off between film uniformity and density when adjusting gas pressure. Higher pressures favor uniformity, while lower pressures favor density and adhesion. The optimal pressure must be chosen based on the specific requirements of the film being deposited.
- Process Control: Adjusting the background gas pressure allows for fine-tuning the sputtering process, enabling control over the energy and direction of the sputtered ions. This control is crucial for achieving the desired film properties, such as microstructure, stress, and surface morphology.
-
Influence of Other Factors:
- Source to Substrate Distance: The distance between the sputtering source and the substrate can affect how the gas pressure influences film quality. A longer distance may allow more time for ions to undergo collisions and diffuse, enhancing uniformity at higher pressures.
- Cathode Angle and Target-Substrate Alignment: The angle of the cathode and the alignment of the target with the substrate can also influence how ions are deposited, affecting both the sputtering rate and film quality. Proper alignment can help mitigate some of the negative effects of lower pressures on uniformity.
-
Practical Considerations:
- Power Source: The type of power source (DC or RF) used in the sputtering process can interact with gas pressure to influence the deposition rate and film quality. RF sputtering, for example, can be more effective at lower pressures due to its ability to sustain plasma under such conditions.
- Material Compatibility: Different target materials may respond differently to changes in gas pressure. Some materials may require higher pressures to achieve the desired film properties, while others may perform better at lower pressures.
In summary, the pressure of the sputtering gas is a critical parameter that directly affects both the sputtering rate and the quality of the deposited film. By carefully adjusting the gas pressure, along with other process parameters, it is possible to achieve the desired balance between deposition rate, film uniformity, and film density. This optimization is essential for producing high-quality thin films tailored to specific applications.
Summary Table:
Parameter | Higher Gas Pressure | Lower Gas Pressure |
---|---|---|
Sputtering Rate | Slower due to ion collisions and diffusive motion | Faster due to high-energy ballistic impacts |
Film Uniformity | Improved uniformity and coverage | Less uniform, potential thickness variations |
Film Density & Adhesion | Lower density and adhesion | Higher density and better adhesion |
Trade-offs | Favors uniformity | Favors density and adhesion |
Key Considerations | Source-substrate distance, cathode alignment | Power source type, material compatibility |
Need help optimizing your sputtering process? Contact our experts today for tailored solutions!