Thermal evaporation is a widely used technique for depositing thin metal films, particularly in applications requiring high purity and precise control over film thickness. The process involves heating a metal source to its evaporation point in a vacuum, allowing the metal atoms to travel and condense onto a substrate, forming a thin film. The substrate is often positioned on a holder or stage that can be rotated or moved to ensure uniform deposition. Additionally, the substrate may be heated to enhance adhesion between the film and the substrate. The entire process is carefully controlled to achieve the desired film properties, which may include post-deposition treatments like annealing to optimize the film's characteristics.
Key Points Explained:
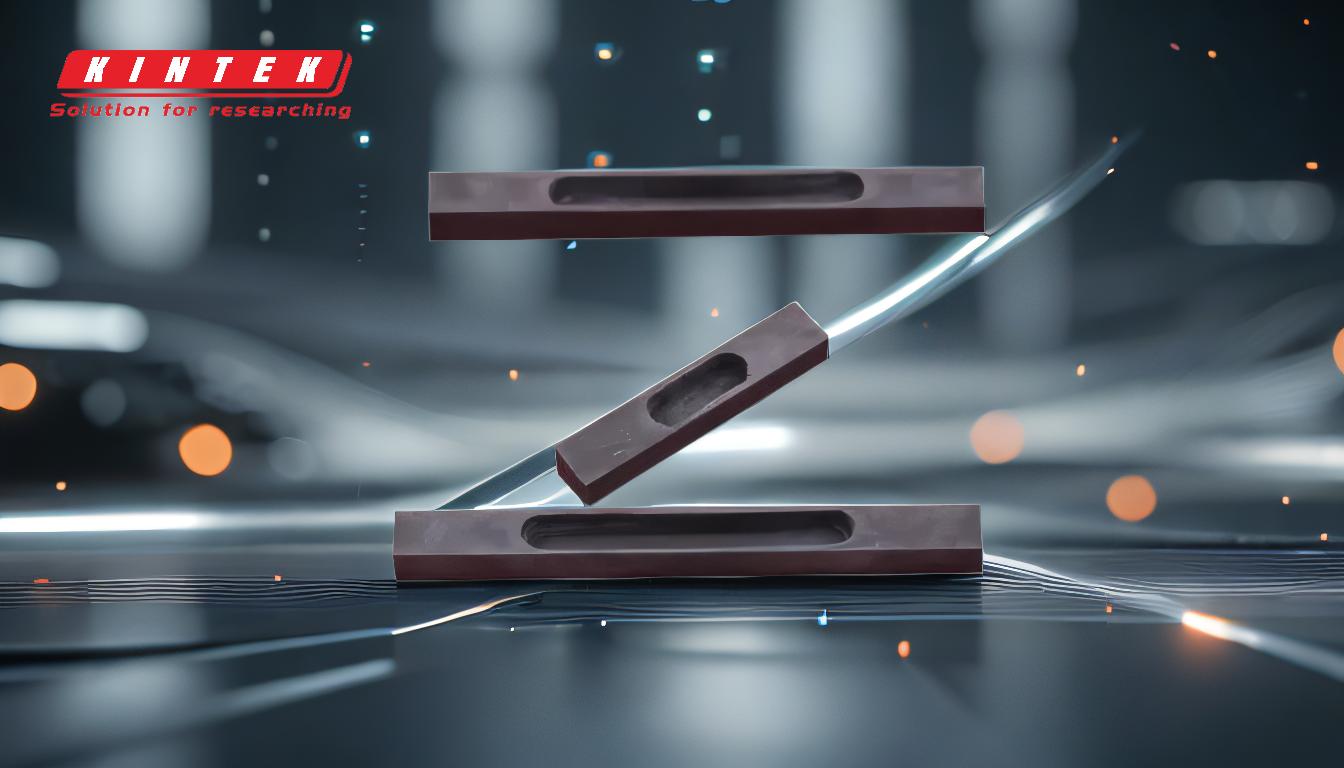
-
Preparation of the Substrate:
- The substrate is placed on a holder or stage designed to ensure even deposition. This stage may have rotational or translational capabilities to expose all areas of the substrate uniformly to the evaporating metal.
- The substrate may be heated to improve adhesion. Heating reduces the likelihood of film delamination and promotes better bonding between the metal film and the substrate.
-
Selection of the Metal Source:
- A pure metal source, often referred to as the target, is chosen based on the desired properties of the thin film. The material must have a suitable evaporation temperature and compatibility with the substrate.
-
Creation of a Vacuum Environment:
- Thermal evaporation is typically performed in a vacuum chamber to minimize contamination and ensure that metal atoms travel unimpeded to the substrate. The vacuum environment also prevents oxidation of the metal during deposition.
-
Heating and Evaporation of the Metal:
- The metal source is heated using a resistive heating element, electron beam, or other methods until it reaches its evaporation point. This causes the metal to transition from a solid to a vapor phase.
- The vaporized metal atoms travel through the vacuum and deposit onto the substrate, forming a thin film.
-
Deposition and Film Formation:
- The metal atoms condense on the substrate, creating a thin film. The thickness of the film is controlled by the duration of the evaporation process and the distance between the source and the substrate.
- Uniformity is achieved through the movement or rotation of the substrate holder.
-
Post-Deposition Treatments:
- After deposition, the film may undergo annealing or heat treatment to improve its structural and electrical properties. This step can help reduce defects and enhance adhesion.
-
Analysis and Optimization:
- The deposited film is analyzed to assess its properties, such as thickness, uniformity, and adhesion. Based on the results, adjustments may be made to the deposition process to achieve the desired film characteristics.
Thermal evaporation is a versatile and precise method for depositing thin metal films, making it suitable for applications in microelectronics, optics, and coatings. The ability to control the deposition environment and parameters ensures high-quality films with tailored properties.
Summary Table:
Step | Description |
---|---|
Substrate Preparation | Substrate is placed on a holder with rotational/translational capabilities. |
Metal Source Selection | Pure metal source chosen based on evaporation temperature and compatibility. |
Vacuum Environment | Process performed in a vacuum to minimize contamination and prevent oxidation. |
Heating & Evaporation | Metal heated to evaporation point, transitioning to vapor phase. |
Deposition & Film Formation | Metal atoms condense on substrate, forming a thin film with controlled thickness. |
Post-Deposition Treatments | Annealing or heat treatment enhances film properties and adhesion. |
Analysis & Optimization | Film properties analyzed; adjustments made to optimize deposition process. |
Discover how thermal evaporation can elevate your thin film applications—contact our experts today!