Diamond coatings are typically very thin, ranging from 0.25 to 5 microns in thickness. This thinness is crucial for maintaining the precision and functionality of the underlying material while enhancing properties such as hardness, wear resistance, and thermal conductivity. The exact thickness can vary depending on the application, with decorative coatings being on the thinner end (around 0.30 microns) and functional coatings being thicker (up to 5 microns). The deposition process and parameters can be adjusted to tailor the coating's properties, such as grain size and surface roughness, to meet specific needs.
Key Points Explained:
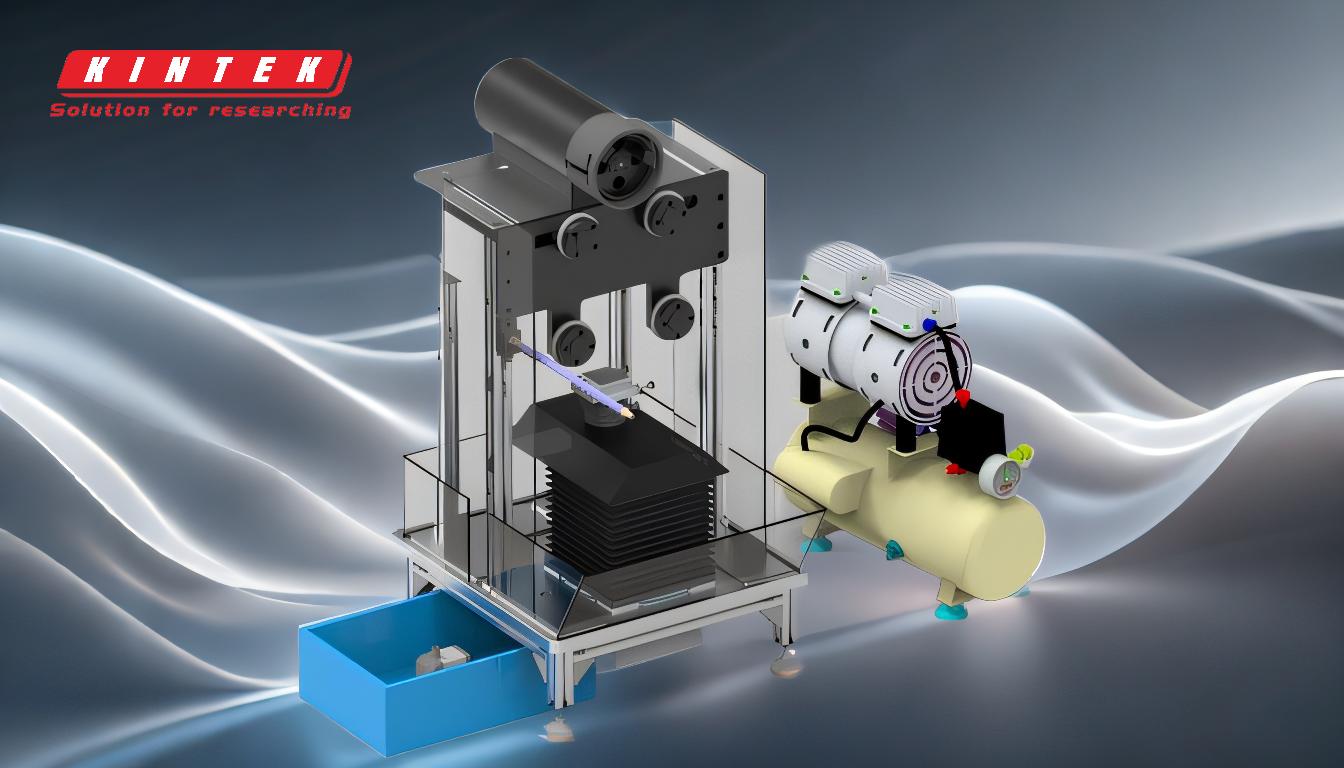
-
Typical Thickness Range of Diamond Coatings:
- Diamond coatings are generally between 0.25 to 5 microns thick.
- This range ensures that the coating enhances properties like hardness and wear resistance without significantly altering the dimensions or appearance of the base material.
-
Comparison to Everyday Objects for Perspective:
- To put this into perspective, a red blood cell is about 8 microns in diameter, and a human hair is around 80 microns thick.
- This means diamond coatings are much thinner than a human hair and even thinner than a red blood cell.
-
Application-Specific Thickness:
- For decorative applications, such as coatings on stainless steel sheets, the thickness might be as low as 0.30 microns.
- For functional applications, where enhanced durability and performance are required, the thickness can range from 2 to 5 microns.
-
Factors Influencing Coating Thickness:
- The thickness of diamond coatings can be tailored based on the application requirements. Factors such as lubrication, surface finish, and type of motion can influence the optimal thickness.
- The deposition process parameters, including gas phase composition and deposition conditions, can also be adjusted to achieve the desired thickness and properties.
-
Benefits of Thin Diamond Coatings:
- Despite their thinness, diamond coatings provide significant benefits, including:
- High hardness: Diamond is one of the hardest known materials, making it ideal for wear-resistant applications.
- Excellent thermal conductivity: This property is beneficial in applications requiring heat dissipation.
- Chemical inertness: Diamond coatings are resistant to chemical reactions, making them suitable for harsh environments.
- Despite their thinness, diamond coatings provide significant benefits, including:
-
Tailoring Coating Properties:
- The quality and characteristics of diamond coatings, such as grain size, surface roughness, and crystallinity, can be controlled during the deposition process.
- This allows for customization of the coating to meet specific performance requirements for different applications.
By understanding these key points, a purchaser can make informed decisions about the appropriate thickness and properties of diamond coatings for their specific needs. The thinness of the coating ensures that it enhances the material's performance without compromising its original specifications.
Summary Table:
Aspect | Details |
---|---|
Thickness Range | 0.25 to 5 microns |
Comparison | Thinner than a red blood cell (8 microns) and a human hair (80 microns) |
Decorative Applications | ~0.30 microns |
Functional Applications | 2 to 5 microns |
Key Benefits | High hardness, excellent thermal conductivity, chemical inertness |
Customization | Grain size, surface roughness, and crystallinity can be tailored |
Need diamond coatings tailored to your application? Contact our experts today for a customized solution!