PVD (Physical Vapor Deposition) coatings are known for their thinness, typically ranging from 0.25 microns to 5 microns. This ultra-thin layer is applied to enhance the surface properties of materials, such as hardness, wear resistance, and corrosion resistance, without significantly altering the dimensions or appearance of the substrate. The thinness of PVD coatings ensures that they are suitable for precision-engineered parts, jewelry, and tools, where maintaining the original specifications is critical. Additionally, PVD coatings are applied at relatively low temperatures, minimizing the risk of thermal damage to the substrate.
Key Points Explained:
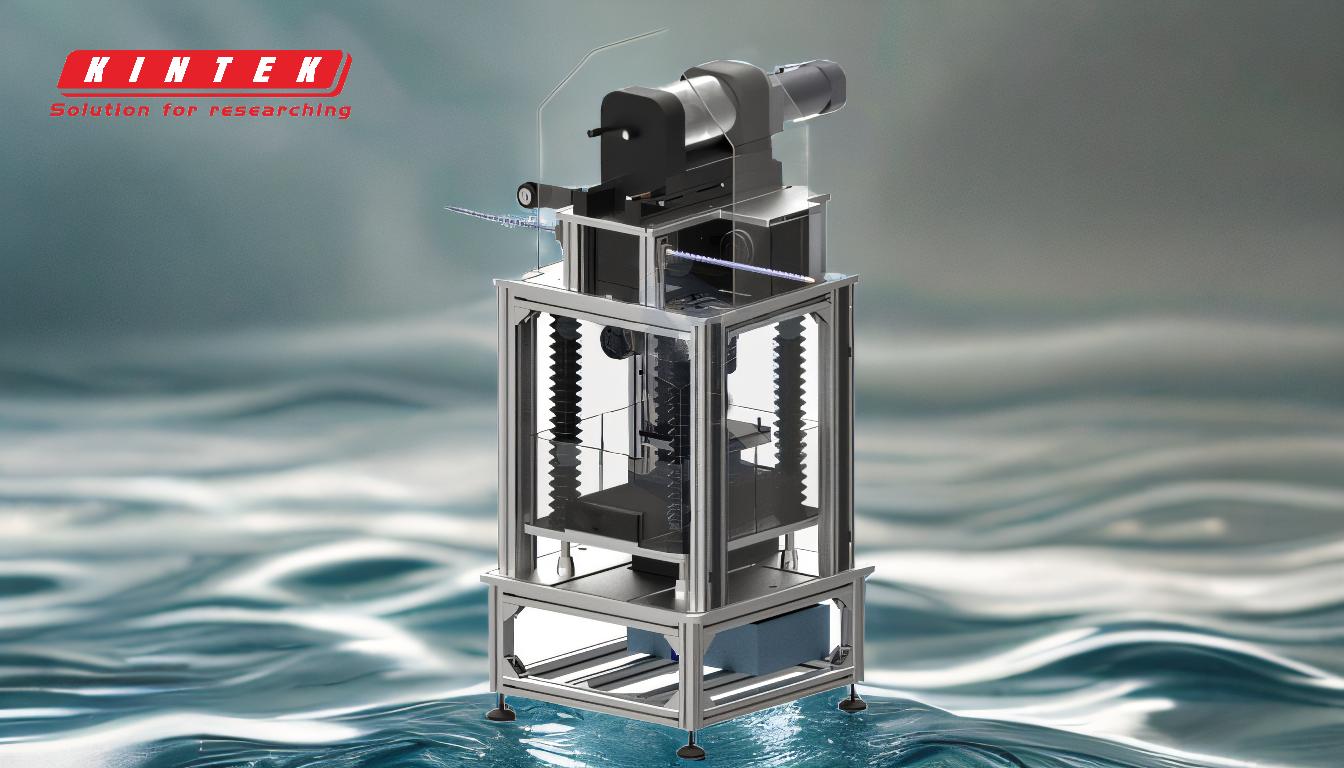
-
Typical Thickness Range of PVD Coatings:
- PVD coatings are extremely thin, with thicknesses ranging from 0.25 microns to 5 microns. This range is consistent across various applications, including engineered parts, jewelry, and cutting tools.
- For comparison, the diameter of a human hair is about 70 microns, making PVD coatings significantly thinner.
-
Benefits of Thin PVD Coatings:
- Preservation of Substrate Dimensions: The thinness of PVD coatings ensures that the original dimensions and specifications of the substrate remain largely unchanged. This is particularly important for precision-engineered parts and tools.
- Enhanced Surface Properties: Despite their thinness, PVD coatings significantly improve surface properties such as hardness, wear resistance, and corrosion resistance.
- Aesthetic Versatility: PVD coatings can be applied to materials like stainless steel to create a variety of finishes and textures without altering the appearance.
-
Application-Specific Thickness:
- Jewelry: PVD coatings on jewelry typically range from 0.25 microns to 5 microns, providing a durable and attractive finish without adding bulk.
- Tools and Industrial Parts: For cutting tools and industrial components, PVD coatings are usually 2-5 microns thick. This thickness is sufficient to enhance performance while preserving the sharpness of blades and reducing cutting forces.
-
Comparison with CVD Coatings:
- PVD coatings are generally thinner than CVD (Chemical Vapor Deposition) coatings. While PVD coatings range from 0.25 to 5 microns, CVD coatings are typically 5-10 microns thick. The thinner PVD coatings are preferred in applications where maintaining precise dimensions is critical.
-
Process Advantages of PVD:
- Low-Temperature Deposition: PVD coatings are applied at temperatures around 500 °C, which is lower than many other coating processes. This reduces the risk of thermal damage to the substrate.
- Compressive Stress Formation: During cooling, PVD coatings form compressive stress, which helps prevent crack formation and expansion. This makes PVD coatings suitable for demanding applications like interrupted cutting processes (e.g., milling).
-
Environmental and Operational Benefits:
- PVD coating processes are environmentally friendly, using physical means rather than chemical reactions. They also feature fast deposition speeds and low deposition temperatures, making them efficient and suitable for coating precision tools and complex geometries.
In summary, PVD coatings are valued for their thinness, which allows them to enhance material properties without compromising the integrity or appearance of the substrate. Their versatility, combined with environmental and operational advantages, makes them a preferred choice in industries ranging from jewelry manufacturing to precision engineering.
Summary Table:
Aspect | Details |
---|---|
Thickness Range | 0.25 to 5 microns |
Key Benefits | - Preserves substrate dimensions - Enhances hardness, wear & corrosion resistance - Aesthetic versatility |
Applications | - Jewelry: 0.25–5 microns - Tools & industrial parts: 2–5 microns |
Comparison with CVD | PVD: 0.25–5 microns CVD: 5–10 microns |
Process Advantages | - Low-temperature deposition (~500°C) - Compressive stress formation |
Environmental Benefits | Eco-friendly, fast deposition, suitable for complex geometries |
Discover how PVD coatings can enhance your materials—contact our experts today for tailored solutions!