To determine if a filter is working properly, the most effective method is to conduct performance testing by analyzing the water before and after it passes through the filter. This involves testing for specific contaminants to evaluate the filter's effectiveness in reducing or removing harmful substances. By comparing the pre- and post-filtration results, you can assess whether the filter meets its intended performance standards.
Key Points Explained:
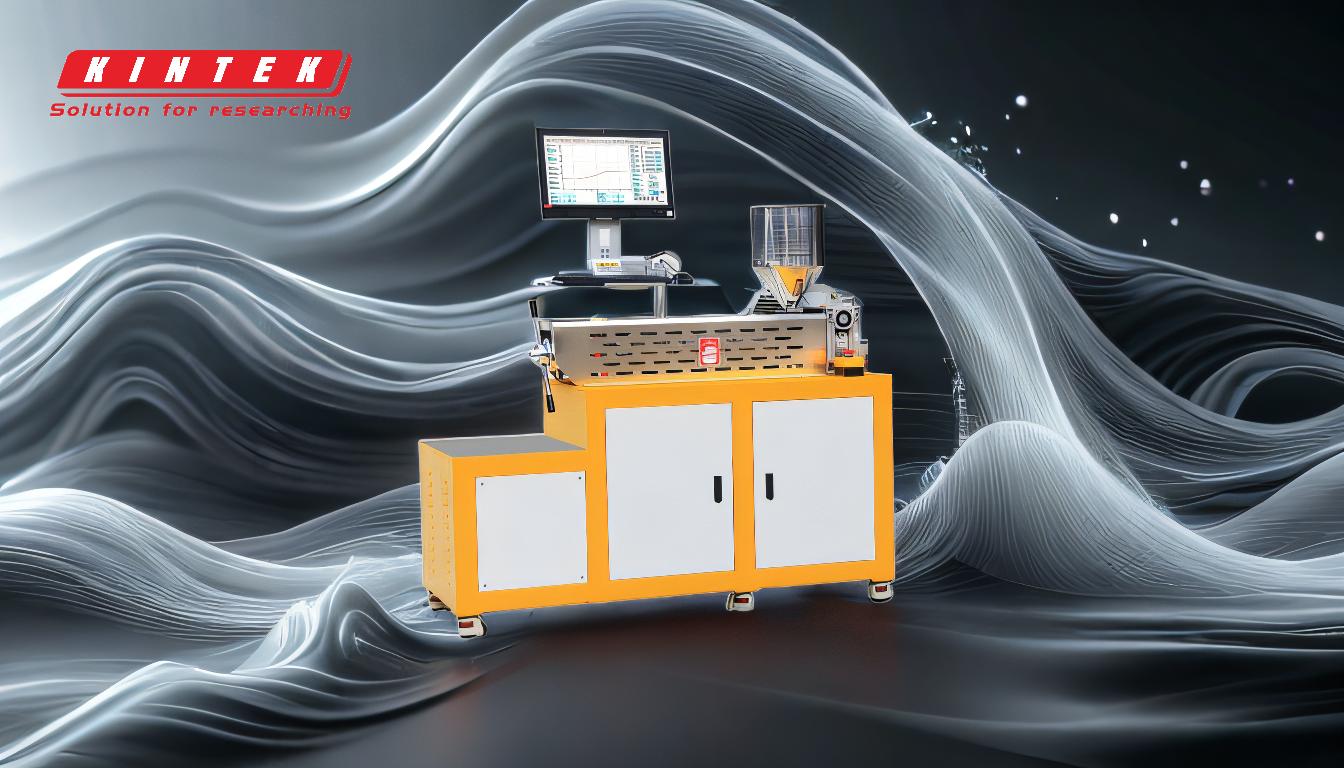
-
Understanding Performance Testing
- Performance testing is the process of evaluating a filter's ability to reduce or remove contaminants from water.
- This involves collecting water samples before and after filtration and testing them for specific contaminants.
- The results provide a clear comparison of the filter's effectiveness in improving water quality.
-
Types of Contaminants to Test For
- Physical Contaminants: Sediment, rust, or particulate matter.
- Chemical Contaminants: Chlorine, lead, pesticides, or volatile organic compounds (VOCs).
- Biological Contaminants: Bacteria, viruses, or parasites.
- Testing should focus on contaminants relevant to your water source and the filter's intended purpose.
-
Steps to Conduct Performance Testing
- Step 1: Collect a water sample directly from the source before it passes through the filter.
- Step 2: Collect a second water sample after it has been filtered.
- Step 3: Use a certified laboratory or at-home testing kits to analyze both samples for specific contaminants.
- Step 4: Compare the results to determine the filter's effectiveness in reducing contaminants.
-
Interpreting Test Results
- Compare the pre- and post-filtration results to see if the filter has significantly reduced the targeted contaminants.
- Check if the filtered water meets safety standards set by regulatory bodies, such as the EPA or WHO.
- If the filter fails to reduce contaminants to acceptable levels, it may indicate a malfunction or the need for replacement.
-
Additional Indicators of Filter Performance
- Flow Rate: A noticeable decrease in water flow may indicate clogging or a need for filter replacement.
- Taste and Odor: Improved taste and odor of water can be a qualitative indicator of effective filtration.
- Visual Inspection: Check for visible signs of wear, damage, or sediment buildup in the filter.
-
Maintenance and Regular Testing
- Regularly replace filters according to the manufacturer's guidelines to ensure consistent performance.
- Conduct periodic performance testing to verify that the filter continues to function effectively over time.
- Keep a record of test results to track the filter's performance and identify any decline in effectiveness.
By following these steps and regularly monitoring your filter's performance, you can ensure that it is working properly and providing safe, clean water.
Summary Table:
Aspect | Details |
---|---|
Performance Testing | Evaluate filter effectiveness by comparing pre- and post-filtration results. |
Contaminants to Test | Physical (sediment, rust), Chemical (chlorine, lead), Biological (bacteria). |
Testing Steps | 1. Collect pre-filtration sample. 2. Collect post-filtration sample. 3. Analyze with lab or kit. 4. Compare results. |
Interpreting Results | Check if contaminants are reduced to safe levels (EPA/WHO standards). |
Additional Indicators | Flow rate, taste/odor improvement, and visual inspection for wear or damage. |
Maintenance | Replace filters as recommended and conduct periodic performance testing. |
Ensure your water filter is working at its best—contact us today for expert advice and testing solutions!