Working with ceramic molds involves a series of steps that require precision and patience to ensure the final piece is of high quality. The process begins with preparing the mold and slip, followed by filling the mold, removing excess slip, releasing the casting, and finishing the piece. Each step plays a crucial role in achieving a successful outcome, from ensuring the mold is securely assembled to carefully releasing the casting without damaging it. Proper technique and attention to detail are essential throughout the process to produce a well-crafted ceramic piece.
Key Points Explained:
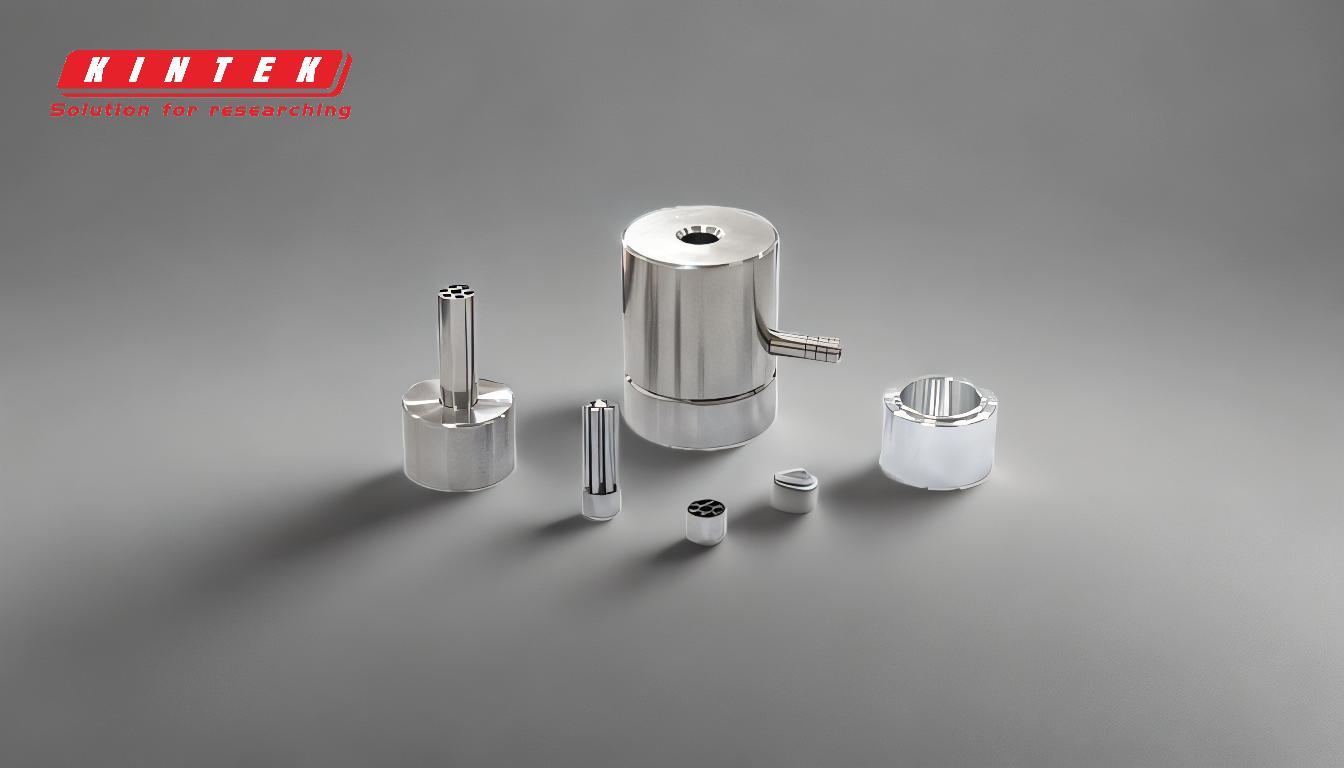
-
Preparing the Mold and Slip:
- Assembling the Mold: Start by aligning the two pieces of your ceramic mold. Ensure they fit together perfectly to avoid any gaps that could cause the slip to leak or create imperfections in the final piece. Secure the mold using rubber bands or clamps to hold it firmly in place during the pouring process.
- Preparing the Slip: Slip is a liquid mixture of clay and water used to fill the mold. Ensure the slip is well-mixed and free of lumps. The consistency of the slip is crucial; it should be fluid enough to pour easily but thick enough to hold its shape once in the mold.
-
Filling the Mold with Slip:
- Pouring the Slip: Slowly pour the slip into the mold's opening until it reaches the top. Pouring too quickly can introduce air bubbles, which may result in defects in the final piece. Take your time to ensure the slip flows evenly and fills all parts of the mold.
- Tapping the Mold: After pouring, gently tap the sides of the mold to release any trapped air bubbles. This step helps to ensure a smooth and even surface on the finished piece.
-
Removing Excess Slip:
- Draining the Mold: Once the mold is filled, allow it to sit for a short period to let the slip begin to set. Then, carefully pour out the excess slip from the mold. This step is crucial for achieving the desired thickness of the ceramic piece. The longer the slip remains in the mold, the thicker the walls of the piece will be.
- Cleaning the Mold Opening: After draining, wipe the opening of the mold to remove any residual slip. This helps to ensure a clean edge on the final piece and prevents any excess material from interfering with the release process.
-
Releasing the Casting from the Mold:
- Drying Time: Allow the slip to dry partially in the mold. The drying time will vary depending on the size of the piece and the humidity of your environment. The piece should be firm enough to hold its shape but still slightly damp when you remove it from the mold.
- Carefully Opening the Mold: Gently separate the two halves of the mold. Take your time to avoid damaging the piece. If the piece sticks to the mold, use a soft tool or your fingers to carefully release it without applying too much pressure.
-
Finishing Your Piece:
- Trimming and Smoothing: Once the piece is removed from the mold, inspect it for any rough edges or imperfections. Use a sponge or a trimming tool to smooth out any uneven areas. This step is essential for achieving a professional finish.
- Drying Completely: Allow the piece to dry completely before moving on to the next steps, such as bisque firing or glazing. Ensure the piece is dried evenly to prevent cracking or warping during the firing process.
- Final Touches: After the piece is fully dried, you can add any additional details, such as carving or attaching handles, before it goes into the kiln for firing. This is also the time to apply any underglazes or decorative elements if desired.
By following these steps carefully, you can successfully work with ceramic molds to create beautiful and functional ceramic pieces. Each stage of the process requires attention to detail, but with practice, you can achieve consistent and high-quality results.
Summary Table:
Step | Key Actions |
---|---|
Preparing the Mold | Align and secure mold pieces; prepare slip for consistent pouring. |
Filling the Mold | Pour slip slowly; tap to release air bubbles. |
Removing Excess Slip | Drain excess slip; clean mold opening for a clean edge. |
Releasing the Casting | Allow partial drying; carefully open the mold to avoid damage. |
Finishing the Piece | Trim, smooth, and dry completely; add final touches before firing. |
Ready to create stunning ceramic pieces? Contact us today for expert guidance and tools!