A ball mill is highly versatile and suitable for both dry and wet grinding processes. It is designed to produce very fine powders with particle sizes as small as 10 microns, making it ideal for a wide range of applications across various industries. The enclosed system ensures sterility and safety, especially when handling toxic materials. Ball mills are also energy-efficient, easy to clean, and require minimal maintenance. Their ability to handle abrasive materials and maintain consistent milling fineness over long periods makes them a reliable choice for continuous operation. Below, we explore the key aspects of ball mills in detail.
Key Points Explained:
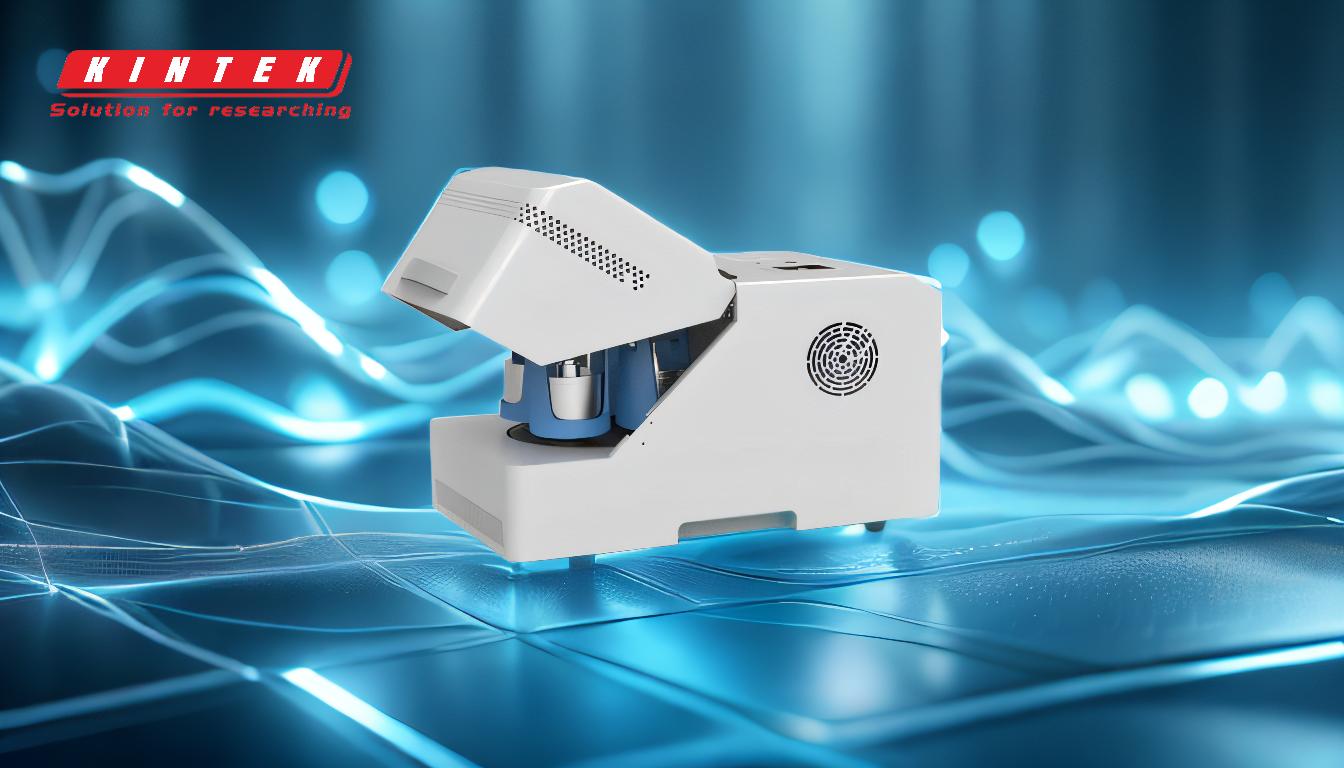
-
Suitability for Dry and Wet Grinding:
- Ball mills are designed to handle both dry and wet grinding processes effectively.
- In dry grinding, the material is fed into the mill in a dry state, and the grinding process relies on the impact and attrition of the grinding balls to reduce particle size.
- In wet grinding, a liquid (usually water or a solvent) is added to the material, creating a slurry. This method is particularly useful for materials that are difficult to grind in a dry state or when a finer particle size is required.
- The choice between dry and wet grinding depends on the material properties, desired particle size, and specific application requirements.
-
Particle Size Reduction:
- Ball mills are capable of producing very fine powders, with particle sizes as small as 10 microns.
- This level of fineness is achieved through the repeated impact and friction between the grinding balls and the material being processed.
- The ability to control particle size makes ball mills suitable for applications requiring precise particle size distribution, such as in the pharmaceutical, chemical, and ceramics industries.
-
Versatility in Applications:
- Ball mills are used in a wide range of industries, including mining, cement, ceramics, fertilizers, and pharmaceuticals.
- They are particularly effective for grinding abrasive materials, such as ores, coal, and pigments.
- In scientific research, ball mills are used for mechanical alloying, mixing materials, and changing material properties.
-
Enclosed System for Safety and Sterility:
- The enclosed design of ball mills ensures that toxic or hazardous materials can be safely processed without risk of contamination or exposure.
- This feature is particularly important in industries like pharmaceuticals and chemicals, where sterility and safety are critical.
-
Energy Efficiency and Low Maintenance:
- Ball mills are designed to be energy-efficient, with low power consumption relative to the amount of material processed.
- They require minimal maintenance, with periodic additions of grinding balls to compensate for wear being the primary upkeep task.
- The simplicity of the design also makes them easy to clean and service, reducing downtime and operational costs.
-
Continuous Operation Capability:
- Ball mills can operate continuously, making them suitable for large-scale industrial applications.
- The ability to maintain consistent milling fineness over long periods ensures reliable performance and high productivity.
-
Space Efficiency:
- Ball mills have a compact design, requiring minimal space for installation.
- This makes them ideal for facilities with limited space or where multiple milling units are needed.
-
Cost-Effectiveness:
- The low maintenance costs and energy efficiency of ball mills contribute to their overall cost-effectiveness.
- Their durability and long service life further enhance their value as a grinding solution.
Conclusion:
Ball mills are a versatile and efficient solution for both dry and wet grinding processes. Their ability to produce fine powders, handle abrasive materials, and operate continuously makes them suitable for a wide range of industrial applications. The enclosed system ensures safety and sterility, while the low energy consumption and maintenance requirements make them a cost-effective choice. Whether you need to grind materials for mining, pharmaceuticals, or ceramics, a ball mill is a reliable and effective option.
Summary Table:
Feature | Description |
---|---|
Dry & Wet Grinding | Handles both dry and wet grinding processes effectively. |
Particle Size Reduction | Produces powders as fine as 10 microns for precise applications. |
Versatility | Used in mining, cement, ceramics, pharmaceuticals, and more. |
Safety & Sterility | Enclosed system ensures safe handling of toxic materials. |
Energy Efficiency | Low power consumption and minimal maintenance requirements. |
Continuous Operation | Reliable performance for large-scale industrial applications. |
Space Efficiency | Compact design ideal for facilities with limited space. |
Cost-Effectiveness | Low operational and maintenance costs with long service life. |
Ready to optimize your grinding process? Contact us today to find the perfect ball mill for your needs!