When comparing a filter press and a clarifier, the choice depends on the specific application, the nature of the material being processed, and the desired outcomes. A filter press is a mechanical device that uses pressure to separate liquids and solids, making it highly effective for dewatering and producing dry filter cakes. On the other hand, a clarifier is designed for liquid-solid separation through sedimentation, making it ideal for continuous operations and producing clear liquids. Both systems have distinct advantages and limitations, and the decision to use one over the other should be based on factors such as throughput, particle size, operational efficiency, and maintenance requirements.
Key Points Explained:
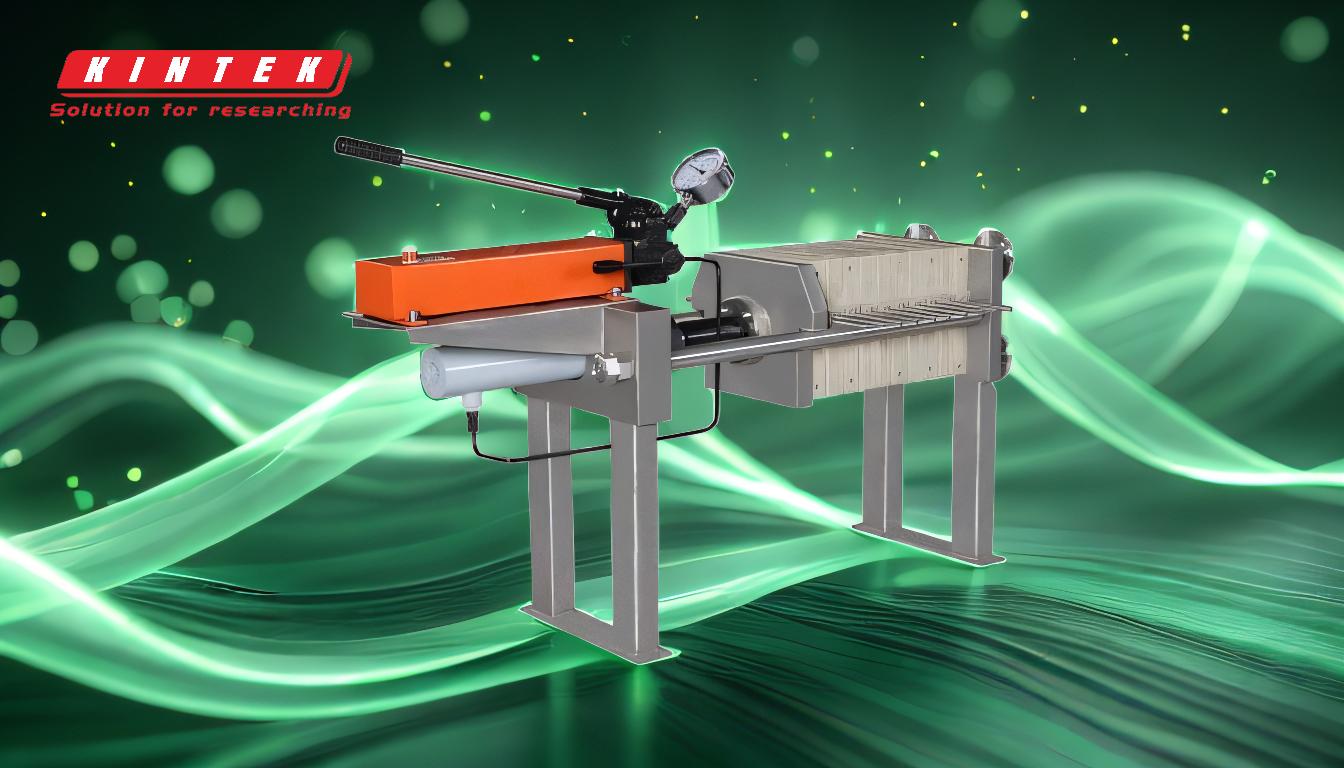
-
Mechanism of Operation:
- Filter Press: A lab filter press operates by applying pressure to a slurry, forcing the liquid (filtrate) through filter cloths or plates while retaining the solids (filter cake). This process is batch-based and highly effective for achieving high solid-liquid separation efficiency.
- Clarifier: A clarifier uses gravity to separate solids from liquids. The slurry is fed into a large tank, where the solids settle at the bottom due to their higher density, and the clarified liquid is collected from the top. This is a continuous process, making it suitable for high-volume operations.
-
Applications:
- Filter Press: Ideal for applications requiring dry filter cakes, such as wastewater treatment, mining, chemical processing, and food production. It is particularly useful when the solids need to be recovered or disposed of in a dry form.
- Clarifier: Best suited for applications where the primary goal is to produce a clear liquid, such as in water treatment plants, beverage production, and municipal wastewater treatment. It is less effective for applications requiring dry solids.
-
Throughput and Efficiency:
- Filter Press: Offers high efficiency in dewatering and can handle a wide range of particle sizes. However, it operates in batches, which may limit throughput in continuous processes.
- Clarifier: Provides continuous operation, making it more suitable for high-throughput applications. However, it may not achieve the same level of dryness in the solids as a filter press.
-
Operational Considerations:
- Filter Press: Requires periodic maintenance, such as replacing filter cloths and cleaning plates. It also needs a reliable source of pressure, which can increase operational costs.
- Clarifier: Generally requires less maintenance but may need regular cleaning to prevent sludge buildup. It is more energy-efficient since it relies on gravity rather than mechanical pressure.
-
Cost and Space Requirements:
- Filter Press: Typically has a higher initial cost and requires more space due to its mechanical components and batch operation.
- Clarifier: Often has a lower initial cost and requires less space, especially in large-scale operations. However, the cost of chemicals used for flocculation in clarifiers can add to operational expenses.
-
Flexibility and Scalability:
- Filter Press: Highly flexible and can be scaled to meet specific needs by adding more plates or increasing pressure. It can handle varying feed concentrations and particle sizes.
- Clarifier: Less flexible in terms of handling varying feed conditions but can be easily scaled for larger volumes by increasing tank size or adding additional units.
In conclusion, neither system is universally "better" than the other; the choice depends on the specific requirements of the application. A filter press is better suited for applications requiring dry solids and high separation efficiency, while a clarifier is more appropriate for continuous operations and producing clear liquids. Both systems have their unique advantages and should be selected based on the specific needs of the process.
Summary Table:
Aspect | Filter Press | Clarifier |
---|---|---|
Mechanism | Uses pressure to separate solids and liquids; batch-based. | Uses gravity for sedimentation; continuous operation. |
Applications | Ideal for dry filter cakes (e.g., wastewater, mining, chemical processing). | Best for clear liquids (e.g., water treatment, beverage production). |
Throughput | High efficiency but limited to batch processing. | Continuous operation, suitable for high-volume applications. |
Maintenance | Requires periodic maintenance (e.g., filter cloth replacement). | Less maintenance but needs regular cleaning to prevent sludge buildup. |
Cost & Space | Higher initial cost and more space required. | Lower initial cost and less space, but chemical costs may add up. |
Flexibility | Highly flexible; scalable by adding plates or increasing pressure. | Less flexible but easily scalable for larger volumes. |
Still unsure which system is right for you? Contact our experts today for personalized advice!