Aluminum brazing and welding are both widely used joining techniques, but they differ significantly in terms of strength, application, and process. Brazing involves joining metals using a filler material with a lower melting point than the base metals, while welding fuses the base metals directly. While brazing can produce strong joints, it is generally not as strong as welding, especially for high-stress applications. However, brazing offers advantages such as lower heat input, reduced distortion, and the ability to join dissimilar metals. The choice between brazing and welding depends on the specific requirements of the application, including the desired strength, material compatibility, and production efficiency.
Key Points Explained:
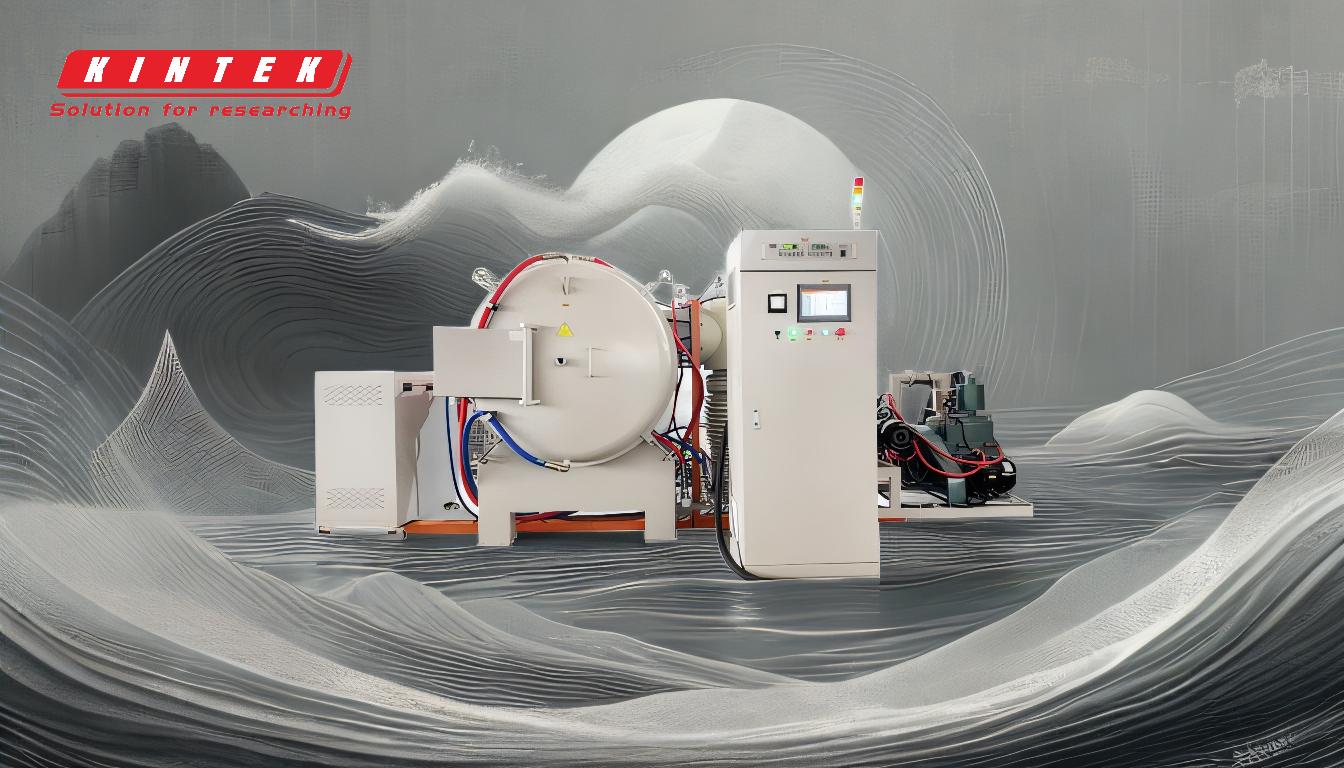
-
Definition and Process Differences:
- Brazing: A joining process that uses a filler metal with a melting point above 450°C (842°F) but below the melting point of the base metals. The filler metal flows into the joint by capillary action, creating a bond without melting the base materials.
- Welding: A process that involves melting the base metals to form a joint, often with the addition of a filler material. The molten pool solidifies to create a strong, continuous bond.
-
Strength Comparison:
- Welding: Generally produces stronger joints because it fuses the base metals directly. The resulting joint has mechanical properties similar to the base material, making it suitable for high-stress applications.
- Brazing: While brazed joints can be strong, they are typically not as strong as welded joints. The strength of a brazed joint depends on the filler material and the design of the joint. Brazed joints are often used in applications where high strength is not the primary requirement.
-
Advantages of Brazing:
- Lower Heat Input: Brazing requires less heat than welding, reducing the risk of distortion or damage to the base materials.
- Joining Dissimilar Metals: Brazing can join different metals, such as aluminum to copper or stainless steel, which can be challenging with welding.
- Complex Geometries: Brazing is well-suited for joining complex or delicate parts because it does not require melting the base materials.
-
Advantages of Welding:
- Higher Strength: Welded joints are generally stronger and more durable, making them ideal for structural applications.
- Better for High-Stress Environments: Welding is preferred in applications where the joint must withstand significant mechanical stress or high temperatures.
- Material Compatibility: Welding is often used for joining similar metals, as it creates a homogeneous joint.
-
Applications:
- Brazing: Commonly used in the automotive, aerospace, and HVAC industries for components like heat exchangers, radiators, and electrical connections.
- Welding: Widely used in construction, manufacturing, and heavy industries for structural components, pipelines, and machinery.
-
Limitations:
- Brazing: Not suitable for high-stress or high-temperature applications. The joint strength is limited by the filler material and joint design.
- Welding: Requires higher skill levels and can cause distortion or heat-affected zones in the base material. It is also less suitable for joining dissimilar metals.
-
Material Considerations:
- Aluminum Brazing: Aluminum and its alloys are commonly brazed using filler metals like aluminum-silicon alloys. The process requires careful control of temperature and atmosphere to prevent oxidation.
- Aluminum Welding: Aluminum welding can be challenging due to its high thermal conductivity and susceptibility to oxidation. Techniques like TIG (Tungsten Inert Gas) welding are often used for aluminum.
-
Cost and Efficiency:
- Brazing: Generally more cost-effective for mass production and complex assemblies due to lower energy consumption and faster processing times.
- Welding: Can be more expensive and time-consuming, especially for large or complex structures, but it offers superior strength and durability.
In conclusion, while aluminum brazing can produce strong and reliable joints, it is generally not as strong as welding. The choice between the two methods depends on the specific requirements of the application, including the desired strength, material compatibility, and production efficiency. For high-stress applications, welding is typically preferred, while brazing is advantageous for joining dissimilar metals or complex geometries with lower heat input.
Summary Table:
Aspect | Brazing | Welding |
---|---|---|
Strength | Strong, but generally not as strong as welding. | Produces stronger joints, ideal for high-stress applications. |
Heat Input | Lower heat input, reduces distortion. | Higher heat input, may cause distortion or heat-affected zones. |
Material Compatibility | Can join dissimilar metals (e.g., aluminum to copper). | Best for joining similar metals. |
Applications | Automotive, aerospace, HVAC (e.g., heat exchangers, radiators). | Construction, manufacturing, heavy industries (e.g., pipelines). |
Cost & Efficiency | Cost-effective for mass production and complex assemblies. | More expensive and time-consuming but offers superior durability. |
Need help choosing between brazing and welding for your project? Contact our experts today for personalized advice!