Compression molding is a manufacturing process used to shape materials like plastics, composites, and rubber by applying heat and pressure. While it is not the fastest molding process compared to methods like injection molding, it offers advantages in terms of cost-effectiveness, material versatility, and the ability to produce large, complex parts. The speed of compression molding depends on factors such as material type, part complexity, mold design, and curing time. For simpler parts and materials with shorter curing times, compression molding can be relatively fast. However, for more complex parts or materials requiring longer curing, the process can be slower. Overall, compression molding is a balanced process that prioritizes quality and cost over speed.
Key Points Explained:
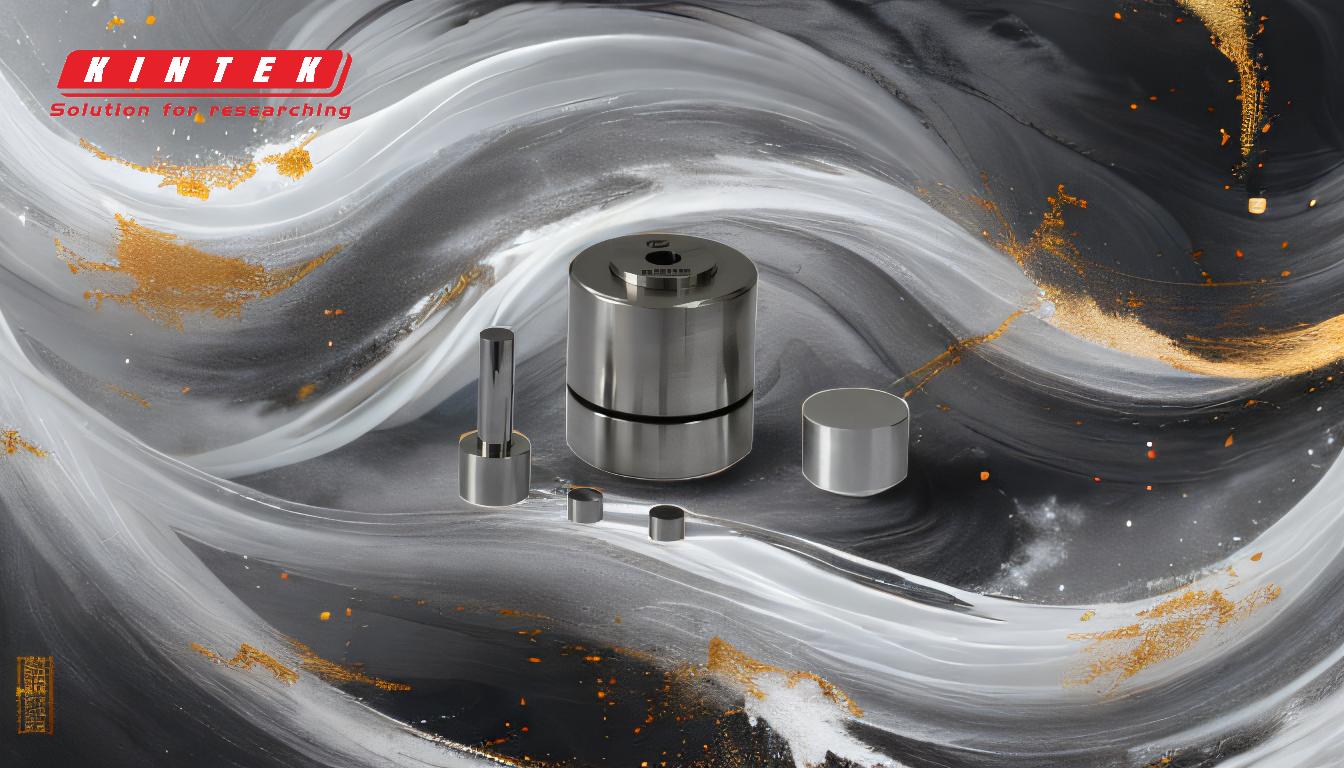
-
Definition of Compression Molding:
- Compression molding involves placing a pre-measured amount of material (often in the form of a preform or sheet) into a heated mold cavity. The mold is then closed, and pressure is applied to shape the material into the desired form. Heat and pressure are maintained until the material cures or solidifies.
-
Speed Comparison with Other Molding Processes:
- Compression molding is generally slower than injection molding, which is known for its high-speed production capabilities. Injection molding injects molten material into a mold at high pressure, allowing for rapid cycle times.
- However, compression molding is faster than some other processes, such as hand lay-up in composite manufacturing, which is labor-intensive and time-consuming.
-
Factors Affecting Speed in Compression Molding:
- Material Type: Thermoplastics and thermosets behave differently under heat and pressure. Thermosets, which require curing, often take longer than thermoplastics, which can be cooled quickly.
- Part Complexity: Simple parts with minimal details can be produced faster than intricate designs that require precise pressure distribution and longer curing times.
- Mold Design: Well-designed molds with efficient heating and cooling systems can reduce cycle times.
- Curing Time: Some materials, like certain rubber compounds, require extended curing times, which can slow down the overall process.
-
Advantages of Compression Molding:
- Cost-Effectiveness: Lower tooling costs compared to injection molding make it suitable for small to medium production runs.
- Material Versatility: It can handle a wide range of materials, including reinforced composites, rubber, and thermosets.
- Large Part Production: Compression molding is ideal for producing large, bulky parts that are difficult to manufacture using other methods.
-
When Compression Molding is Considered Fast:
- For simpler parts made from materials with short curing times, compression molding can be relatively fast. For example, producing rubber gaskets or seals can be quick due to the simplicity of the parts and the properties of the material.
- Automated compression molding systems can also improve speed by reducing manual intervention and optimizing cycle times.
-
Limitations in Speed:
- Complex parts with intricate details or those requiring long curing times can slow down the process.
- The need for manual loading and unloading in some setups can add to the overall production time.
-
Applications Where Speed is Secondary:
- Compression molding is often chosen for applications where quality, material properties, and cost are more critical than speed. Examples include automotive components, electrical insulators, and high-strength composite parts.
In summary, while compression molding is not the fastest molding process, it offers a balance of speed, cost, and quality that makes it suitable for specific applications. Its speed depends on various factors, but it excels in producing high-quality parts efficiently for certain industries and materials.
Summary Table:
Factor | Impact on Speed |
---|---|
Material Type | Thermosets (slower) vs. thermoplastics (faster) |
Part Complexity | Simple parts (faster) vs. intricate designs (slower) |
Mold Design | Efficient heating/cooling systems reduce cycle times |
Curing Time | Longer curing times slow the process |
Automation | Automated systems improve speed by reducing manual steps |
Need help determining if compression molding is right for your project? Contact our experts today!