CVD (Chemical Vapor Deposition) and PVD (Physical Vapor Deposition) are both advanced coating technologies, each with unique advantages and limitations. CVD excels in creating uniform, high-purity, and fine-grained coatings, even on complex shapes, and offers higher deposition rates with precise thickness control. It is also cost-effective for producing high-quality thin films and large-area coatings. However, CVD has higher energy consumption and requires medium-to-high temperatures. On the other hand, PVD is environmentally friendly, produces extremely thin and pure coatings, and is suitable for creating harder, corrosion-resistant surfaces. While PVD is slower, more expensive, and requires maintenance, it has been improving in material versatility and performance. The choice between CVD and PVD depends on specific application requirements, such as coating uniformity, material properties, cost, and environmental considerations.
Key Points Explained:
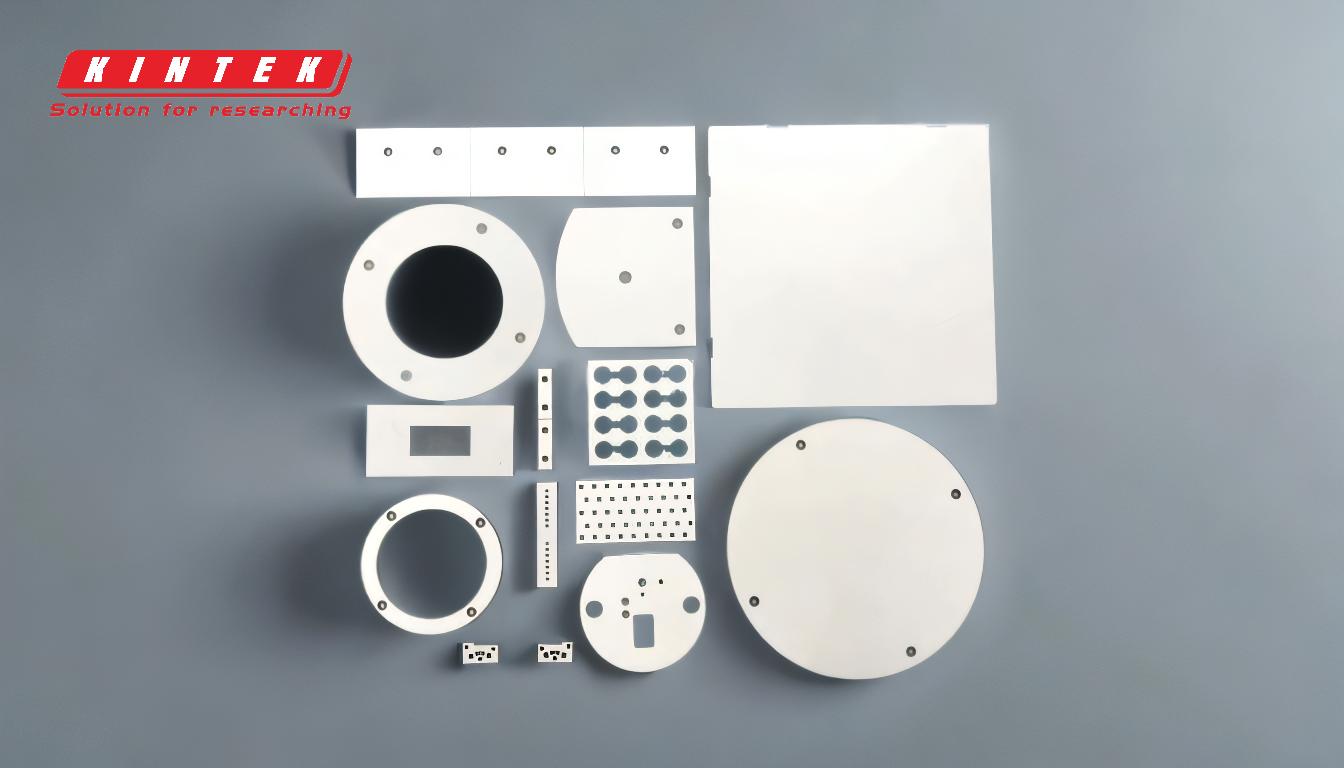
-
Uniform Coating Thickness and Complex Shapes:
- CVD can produce coatings with uniform thickness even on complex geometries, which is challenging for PVD due to its line-of-sight nature. This makes CVD ideal for applications requiring consistent coverage over intricate shapes.
-
Coating Properties:
- CVD coatings are high-purity, waterproof, fine-grained, and harder than those produced by traditional methods. These properties make CVD suitable for applications demanding durability and precision.
- PVD, on the other hand, creates extremely thin, pure, and corrosion-resistant coatings, improving surface quality and hardness. It is particularly valued for its environmental friendliness and compliance with FDA requirements.
-
Deposition Rates and Thickness Control:
- CVD offers high deposition rates, and the thickness of coatings can be precisely controlled by adjusting temperature and duration. This makes CVD efficient for large-scale production and applications requiring specific coating thicknesses.
- PVD has a slower rate of yield, which can limit its feasibility in high-throughput applications.
-
Energy Consumption and Temperature Requirements:
- CVD operates at medium temperatures (500–1100°C), making it versatile for various applications. However, it has higher energy consumption compared to PVD, which is a consideration for sustainability and cost.
- PVD processes, while requiring routine maintenance and cooling systems, are generally more energy-efficient.
-
Cost and Equipment Maintenance:
- CVD has lower equipment setup costs compared to some high-pressure, high-temperature (HPHT) technologies, making it cost-effective for certain applications.
- PVD can be expensive due to equipment costs and maintenance requirements, particularly for cooling systems. This limits its feasibility in some scenarios.
-
Material Versatility and Performance:
- CVD is advantageous for growing diamonds and producing coatings over large areas, with control over chemical impurities. It does not require high pressure, simplifying the process.
- PVD has been expanding its range of coating materials and improving performance, gradually outperforming CVD in many areas, particularly with advanced materials like Al2O3.
-
Environmental and Regulatory Compliance:
- PVD is environmentally friendly, non-toxic, and meets FDA requirements, making it suitable for applications in the medical and food industries.
- CVD, while effective, has higher energy consumption and may not be as environmentally friendly in some cases.
In conclusion, the choice between CVD and PVD depends on the specific requirements of the application, such as the need for uniform coatings, material properties, cost considerations, and environmental impact. Both technologies have their strengths and are continually evolving to meet industry demands.
Summary Table:
Feature | CVD | PVD |
---|---|---|
Uniform Coating | Excellent on complex shapes | Limited by line-of-sight nature |
Coating Properties | High-purity, fine-grained, hard | Thin, pure, corrosion-resistant |
Deposition Rate | High | Slower |
Energy Consumption | Higher | Lower |
Cost | Cost-effective for large-area coatings | Expensive due to equipment and maintenance |
Environmental Impact | Higher energy consumption | Environmentally friendly, FDA-compliant |
Applications | Ideal for uniform coatings, large areas, and diamond growth | Suitable for medical, food industries, and corrosion-resistant surfaces |
Still unsure which coating technology is right for you? Contact our experts today for personalized advice!