Physical vapor deposition (PVD) is a manufacturing process used to deposit thin films of material onto a substrate. It is widely used in industries such as semiconductors, optics, and coatings. The question of whether PVD is a top-down or bottom-up process is rooted in the fundamental approach of how materials are assembled or manipulated. PVD is inherently a bottom-up process because it involves the creation of thin films by building up material atom by atom or molecule by molecule from a vapor phase onto a substrate. This contrasts with top-down processes, which involve removing material from a bulk source to achieve the desired structure.
Key Points Explained:
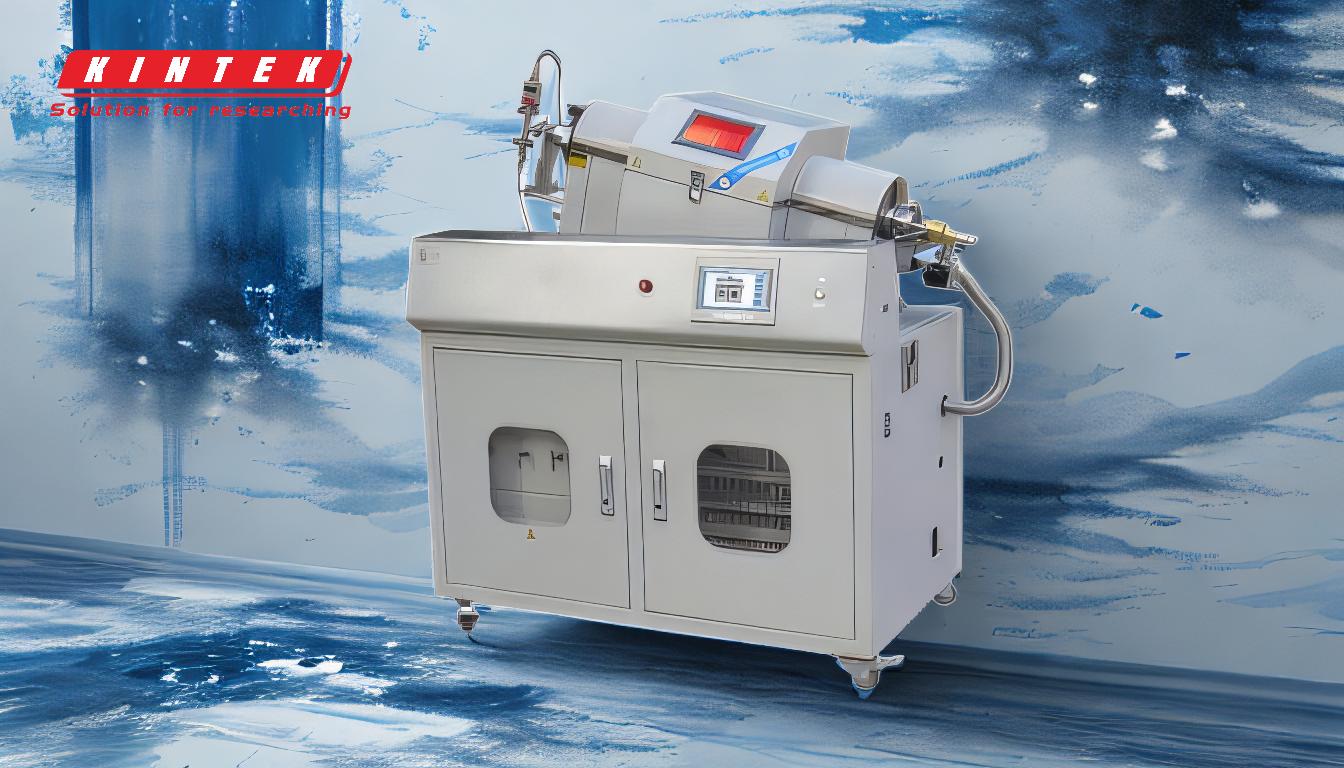
-
Definition of PVD:
- Physical vapor deposition (PVD) is a process where a solid material is vaporized in a vacuum and then deposited as a thin film onto a substrate. This is achieved through methods such as sputtering, evaporation, or ion plating.
- The process involves the transformation of a solid material into a vapor phase, followed by condensation onto a target surface.
-
Bottom-Up Approach:
- PVD is classified as a bottom-up process because it builds material layer by layer at the atomic or molecular level. This is in contrast to top-down methods, which involve cutting, etching, or machining material away from a larger piece.
- In PVD, the material is deposited atom by atom or molecule by molecule, allowing for precise control over the thickness and composition of the film.
-
Comparison to Top-Down Processes:
- Top-down processes, such as lithography or mechanical machining, start with a bulk material and remove portions to create the desired shape or structure.
- PVD, on the other hand, starts with a vaporized material and deposits it onto a substrate, building up the structure from the ground up.
-
Advantages of PVD as a Bottom-Up Process:
- Precision: PVD allows for the creation of very thin and uniform films, often at the nanometer scale.
- Material Versatility: A wide range of materials, including metals, ceramics, and composites, can be deposited using PVD.
- Adhesion: The films produced by PVD typically have excellent adhesion to the substrate, making them durable and long-lasting.
-
Applications of PVD:
- Semiconductors: PVD is used to deposit thin films of conductive and insulating materials in the fabrication of integrated circuits.
- Optics: PVD is employed to create reflective and anti-reflective coatings on lenses and mirrors.
- Coatings: PVD is used to apply wear-resistant and decorative coatings on tools, automotive parts, and jewelry.
-
Process Steps in PVD:
- Vaporization: The source material is vaporized using techniques such as thermal evaporation, sputtering, or arc vaporization.
- Transport: The vaporized material is transported through a vacuum or low-pressure environment to the substrate.
- Deposition: The vaporized material condenses on the substrate, forming a thin film.
- Nucleation and Growth: The deposited atoms or molecules nucleate and grow into a continuous film.
-
Challenges and Considerations:
- Uniformity: Achieving uniform deposition across large or complex substrates can be challenging.
- Contamination: The process must be carefully controlled to avoid contamination from impurities in the vacuum environment.
- Cost: PVD equipment and processes can be expensive, particularly for large-scale or high-throughput applications.
In summary, physical vapor deposition (PVD) is a bottom-up process that involves the deposition of material from a vapor phase onto a substrate, building up thin films atom by atom or molecule by molecule. This approach offers significant advantages in terms of precision, material versatility, and adhesion, making it a valuable technique in various industries.
Summary Table:
Aspect | Details |
---|---|
Process Type | Bottom-up |
Key Mechanism | Builds material atom by atom or molecule by molecule from a vapor phase |
Comparison to Top-Down | Top-down removes material; PVD deposits material |
Advantages | Precision, material versatility, excellent adhesion |
Applications | Semiconductors, optics, coatings |
Challenges | Uniformity, contamination control, cost |
Unlock the potential of PVD for your projects—contact our experts today!