Plastic pyrolysis can be energy efficient, particularly when advanced technologies and optimized designs are employed. The energy efficiency of plastic pyrolysis depends on several factors, including the design of the reactor, the condensing system, and the overall process management. Advanced pyrolysis plants incorporate features like 360-degree thermal insulation and efficient condensing systems to minimize heat loss and improve energy recovery. Additionally, the high recovery rate of converting pyrolysis oil into usable fuels like gasoline or diesel further enhances energy efficiency. However, factors such as heat loss, hydrogen compression, and side reactions must be carefully managed to maximize efficiency. Overall, with proper design and operation, plastic pyrolysis can be a highly energy-efficient process.
Key Points Explained:
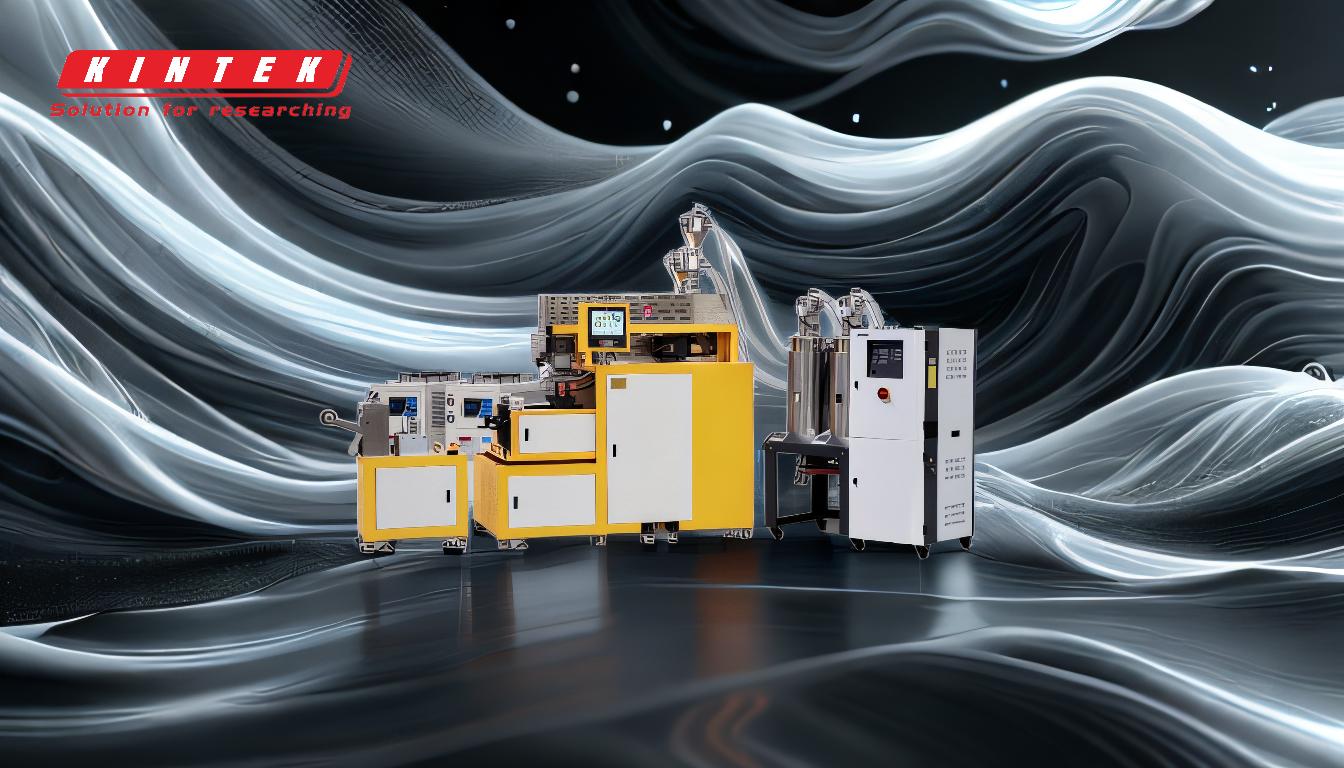
-
Importance of Energy Efficiency in Pyrolysis Plants:
- Energy efficiency is critical for the profitability of pyrolysis operations.
- Advanced pyrolysis plants focus on efficient energy recovery to optimize performance.
-
Reactor Design and Thermal Insulation:
- The reactor is designed with a 360-degree all-directional thermal insulation layer.
- This design reduces heating heat requirements and shortens the pyrolysis time, contributing to energy savings.
-
Condensing System Efficiency:
- The condensing system combines vertical and horizontal condensation.
- This combination cools the pyrolysis oil gas more efficiently, reducing cooling time and improving batch processing efficiency.
-
High Recovery Rate of Pyrolysis Oil:
- The plant efficiently converts plastic pyrolysis oil into gasoline or diesel.
- The high recovery rate of approximately 90% indicates effective energy utilization in the conversion process.
-
Factors Affecting Energy Efficiency:
- Process-specific heat loss must be minimized to maintain high energy efficiency.
- The expenditure for hydrogen compression and the presence of side reactions producing hydrocarbons and aromatic compounds can impact overall efficiency.
-
Overall Energy Efficiency:
- With advanced design features and careful management of operational factors, plastic pyrolysis can achieve high energy efficiency.
- The integration of efficient thermal insulation, condensing systems, and high recovery rates makes plastic pyrolysis a viable and energy-efficient method for converting waste plastic into valuable fuels.
Summary Table:
Key Factor | Impact on Energy Efficiency |
---|---|
Reactor Design | 360-degree thermal insulation reduces heat loss and shortens pyrolysis time. |
Condensing System | Vertical and horizontal condensation improves cooling efficiency and batch processing. |
Pyrolysis Oil Recovery Rate | High recovery rate (~90%) ensures effective energy utilization in fuel conversion. |
Heat Loss Management | Minimizing heat loss is critical for maintaining high energy efficiency. |
Hydrogen Compression Costs | Expenditure for hydrogen compression can impact overall efficiency. |
Side Reactions | Managing side reactions prevents energy waste and improves process efficiency. |
Want to maximize energy efficiency in your pyrolysis operations? Contact our experts today to learn more!