PVD (Physical Vapor Deposition) and CVD (Chemical Vapor Deposition) are both advanced coating technologies, but they differ significantly in their processes, applications, and outcomes. PVD is generally better suited for applications requiring high durability, temperature resistance, and environmental friendliness, as it operates at lower temperatures and produces no harmful by-products. CVD, on the other hand, is better for coating a wider range of materials and achieving thicker, more uniform layers, but it often requires higher temperatures and can produce toxic by-products. The choice between PVD and CVD depends on the specific requirements of the application, such as material compatibility, desired coating properties, and environmental considerations.
Key Points Explained:
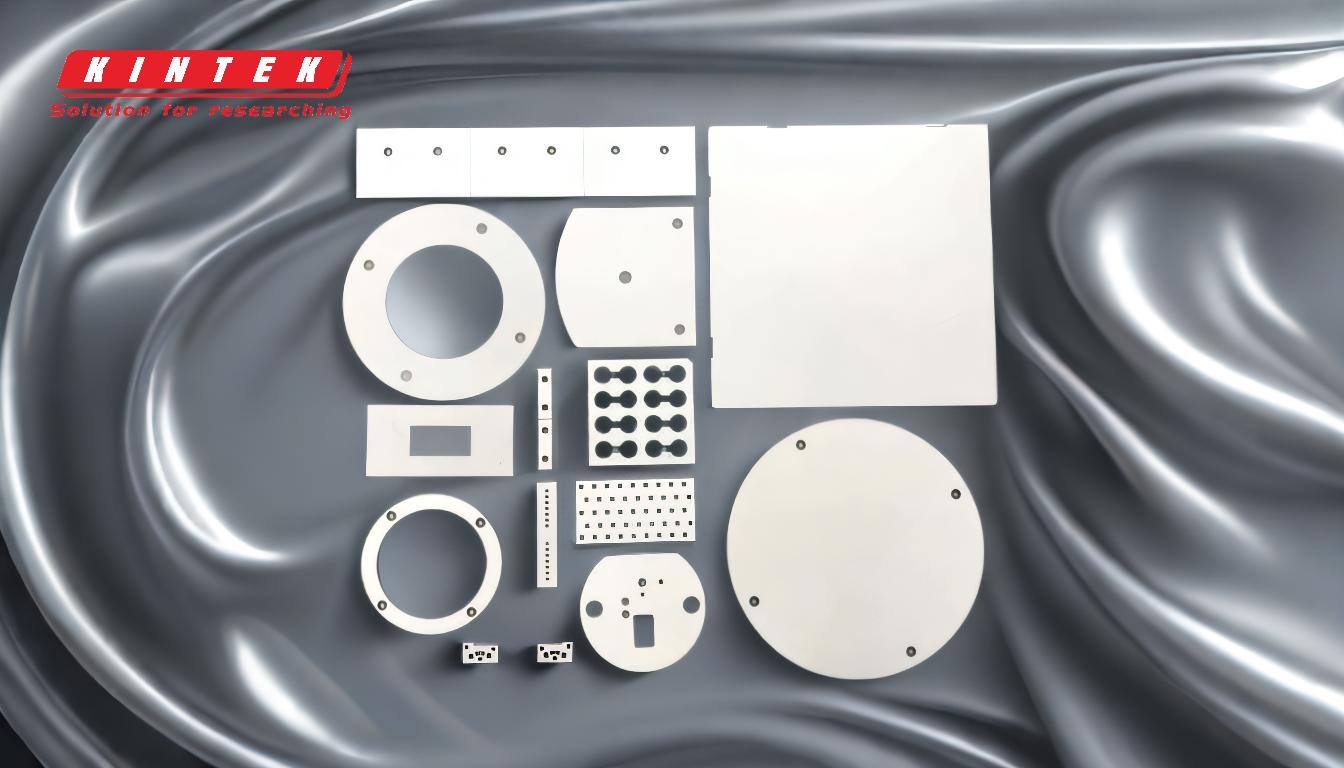
-
Process Differences:
- PVD: Involves the physical transformation of a solid coating material into a vapor, which then condenses onto the substrate. This process does not involve chemical reactions, making it environmentally friendly.
- CVD: Relies on chemical reactions between gaseous precursors and the substrate to form a thin film. This process can produce toxic by-products and requires higher temperatures.
-
Temperature Requirements:
- PVD: Operates at relatively low temperatures (250°C~450°C), making it suitable for heat-sensitive materials and eliminating the need for post-coating heat treatment.
- CVD: Typically requires higher temperatures (450°C to 1050°C), which can limit its use with certain materials and necessitate additional heat treatment.
-
Coating Properties:
- PVD: Produces thin, smooth, and durable coatings that replicate the original surface finish of the substrate. PVD coatings are known for their high temperature and abrasion resistance.
- CVD: Can create thicker and more uniform coatings, but often results in a matte finish unless the part is polished. CVD coatings are generally more versatile in terms of material compatibility.
-
Environmental Impact:
- PVD: Environmentally friendly, as it produces no harmful by-products and uses physical processes that do not involve chemical reactions.
- CVD: Can generate toxic by-products due to the chemical reactions involved, making it less environmentally friendly compared to PVD.
-
Application Suitability:
- PVD: Ideal for applications requiring high durability, wear resistance, and environmental friendliness. Commonly used in industries such as aerospace, automotive, and medical devices.
- CVD: Better suited for applications requiring thicker coatings and compatibility with a wider range of materials. Often used in semiconductor manufacturing and other high-tech industries.
-
Equipment and Cost:
- PVD: Equipment is generally less specialized and easier to maintain, with lower operational costs due to the absence of toxic by-products.
- CVD: Requires more specialized equipment to handle toxic by-products and higher temperatures, leading to higher operational and maintenance costs.
In summary, while both PVD and CVD have their unique advantages, PVD is often preferred for its environmental benefits, lower temperature requirements, and high durability. CVD, however, offers greater versatility in material compatibility and the ability to produce thicker coatings. The choice between the two should be based on the specific needs of the application, including material properties, desired coating characteristics, and environmental considerations.
Summary Table:
Aspect | PVD | CVD |
---|---|---|
Process | Physical transformation of solid to vapor; no chemical reactions. | Chemical reactions between gases and substrate; may produce by-products. |
Temperature | Low (250°C~450°C); suitable for heat-sensitive materials. | High (450°C to 1050°C); may require post-coating heat treatment. |
Coating Properties | Thin, smooth, durable; replicates substrate finish. | Thicker, uniform; matte finish unless polished. |
Environmental Impact | No harmful by-products; environmentally friendly. | May produce toxic by-products; less eco-friendly. |
Applications | High durability, wear resistance; used in aerospace, automotive, medical. | Thicker coatings, material versatility; used in semiconductors, high-tech. |
Cost & Equipment | Lower operational costs; less specialized equipment. | Higher costs; specialized equipment for handling toxic by-products. |
Need help choosing between PVD and CVD for your application? Contact our experts today for personalized advice!