PVD (Physical Vapor Deposition) coating is an excellent choice for watches due to its durability, aesthetic appeal, and functional benefits. It enhances the appearance of watches by providing a wide range of colors, including gold-like finishes, while also improving resistance to corrosion, wear, and scratches. PVD coatings are environmentally friendly, operate at lower temperatures to avoid thermal damage, and are thin enough to preserve intricate details. These qualities make PVD-coated watches more durable and visually appealing, ensuring they maintain their look and functionality over time. Additionally, PVD coatings are versatile, making them suitable for both high-volume production and small batches, which aligns well with the watch industry's needs.
Key Points Explained:
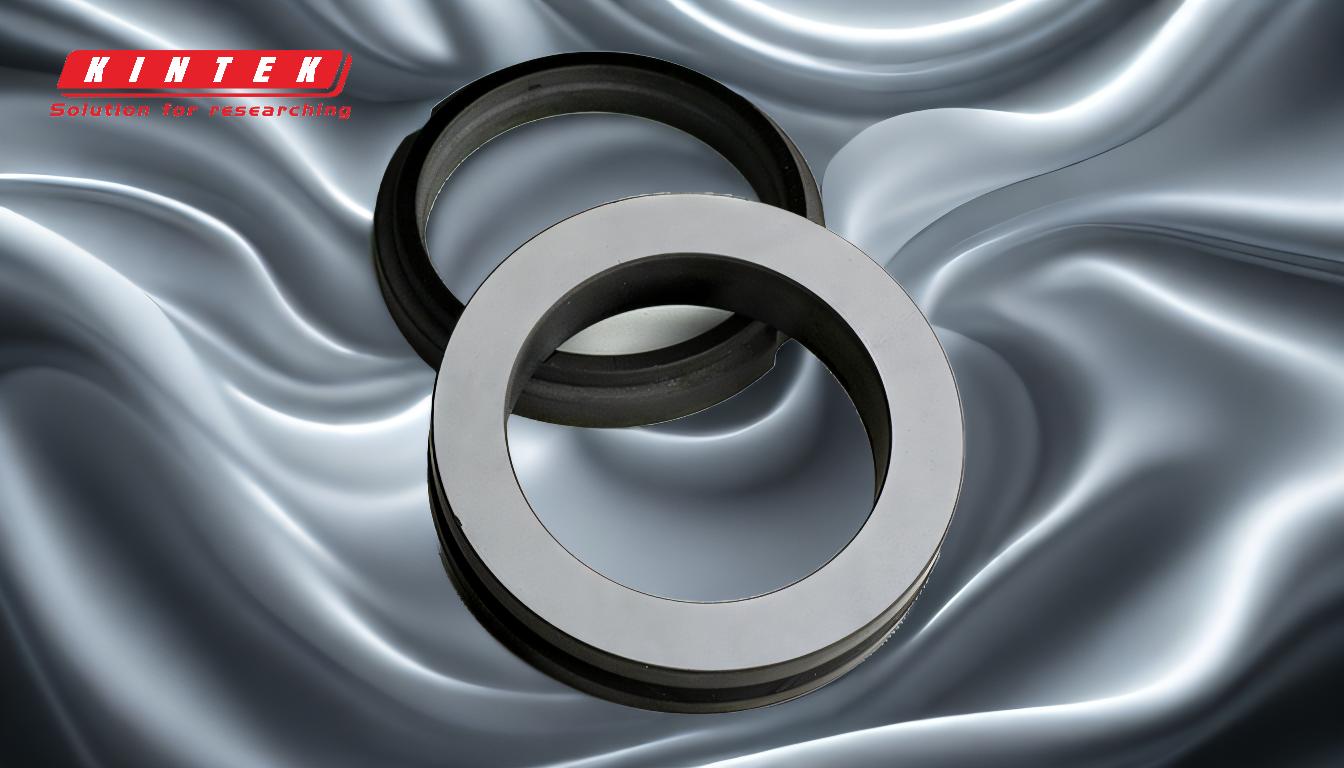
-
Durability and Longevity
- PVD coatings significantly enhance the durability of watches by providing resistance to corrosion, wear, and scratches. This ensures that the watch maintains its appearance and functionality over time, even with daily use.
- The process forms a thin, hard layer (3~5μm) that is highly resistant to environmental factors, making it ideal for watches exposed to varying conditions.
-
Aesthetic Appeal
- PVD coatings offer a wide range of colors, including gold-like finishes, which can enhance the visual appeal of watches. This allows for customization and luxury finishes without the need for solid gold, making high-end designs more accessible.
- The coatings do not fade over time, ensuring that the watch retains its original look for years.
-
Environmental and Operational Benefits
- PVD is an environmentally friendly process, as it does not involve harmful chemicals or produce hazardous waste. This aligns with the growing demand for sustainable manufacturing practices.
- The process operates at relatively low temperatures (around 500 °C), reducing the risk of thermal damage to the watch components, which is crucial for preserving delicate materials and intricate designs.
-
Functional Advantages
- PVD coatings improve wear resistance, which is particularly beneficial for watch components like bezels and bracelets that are prone to scratches and abrasions.
- The compressive stress formed during the coating process helps prevent crack formation and expansion, further enhancing the durability of the watch.
-
Versatility in Production
- PVD coating machines are computer-controlled and adaptable to both high-volume and small-batch production. This makes them ideal for the watch industry, where manufacturers may need to produce limited-edition designs alongside mass-market models.
- The process reduces production costs and turnaround time, making it an efficient choice for watchmakers.
-
Industry Applications
- PVD coatings are widely used in industries such as automotive, aerospace, and medical devices, where durability and performance are critical. This demonstrates the reliability and effectiveness of PVD coatings, which can be directly applied to the watch industry.
In conclusion, PVD coating is an excellent option for watches, offering a combination of durability, aesthetic appeal, and functional benefits. Its environmentally friendly nature and versatility in production further solidify its position as a preferred choice for watch manufacturers aiming to produce high-quality, long-lasting timepieces.
Summary Table:
Benefit | Description |
---|---|
Durability | Resistant to corrosion, wear, and scratches; maintains appearance over time. |
Aesthetic Appeal | Wide range of colors, including gold-like finishes; retains original look. |
Environmental Benefits | Eco-friendly process with no harmful chemicals or waste. |
Functional Advantages | Improves wear resistance; prevents crack formation. |
Versatility | Suitable for high-volume and small-batch production; reduces costs and time. |
Enhance your watch designs with PVD coating—contact us today to learn more!