PVD (Physical Vapor Deposition) coatings are generally considered food-safe due to their strong adhesion to substrates, chemical inertness, and biological stability. These coatings are widely used in the food industry, particularly in cutlery and commercial kitchen equipment, because of their durability, resistance to wear, and ability to prevent microbial growth. PVD coatings are thin, ranging from 0.5 to 5 microns, and are highly resistant to corrosion and oxidation. While the application process requires safety precautions to avoid inhaling particles, the coatings themselves are safe once applied, as the particles are firmly bonded and pose no risk of contamination.
Key Points Explained:
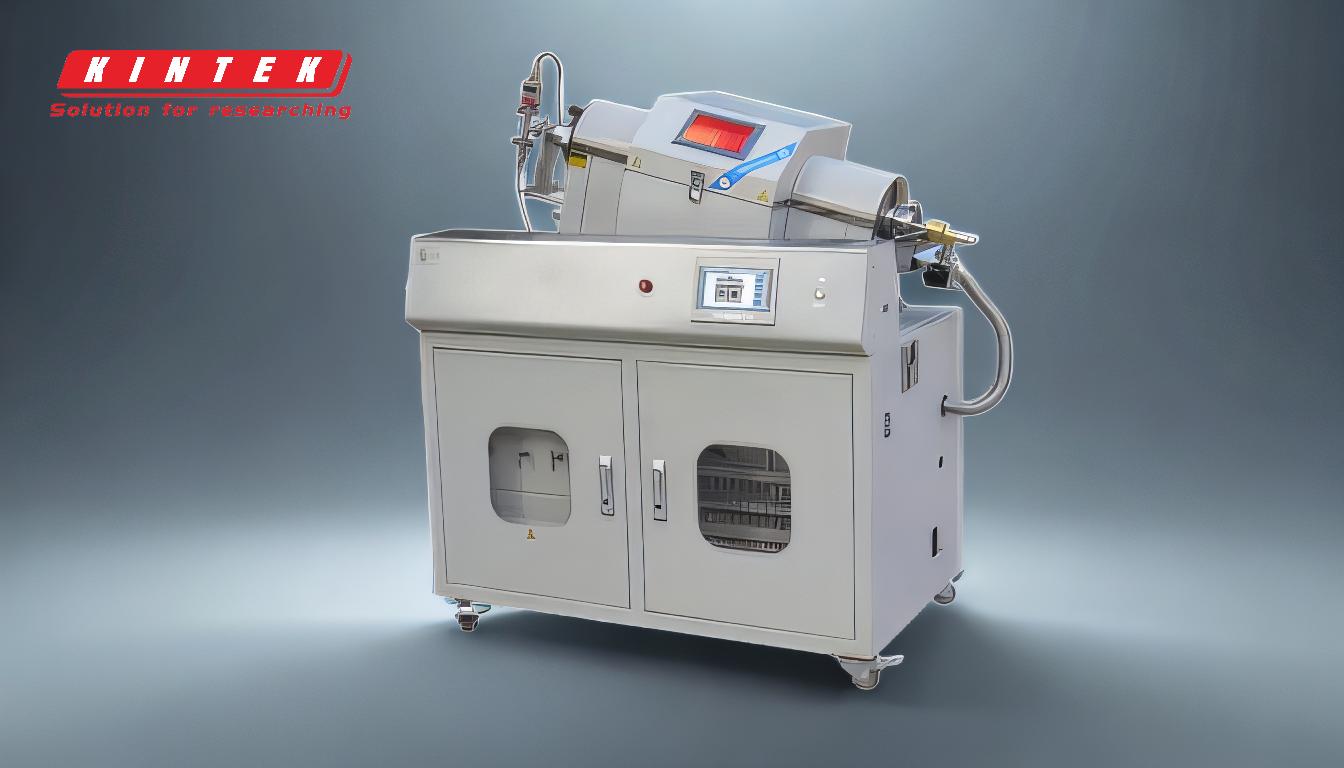
-
Food Safety of PVD Coatings:
- PVD coatings are chemically and biologically inert, making them safe for food contact.
- They adhere strongly to substrates, ensuring they do not flake or contaminate food.
- These coatings are widely used in the cutlery industry and commercial kitchen equipment, demonstrating their suitability for food-related applications.
-
Applications in the Food Industry:
- PVD coatings are used in cutlery for both decorative and functional purposes, enhancing durability and wear resistance.
- In food packaging, PVD-coated materials (e.g., aluminum-coated plastics) help preserve freshness and prevent microbial growth.
- Silver-embedded PET plastics, created using PVD, are used to ensure food safety by inhibiting bacterial growth.
-
Durability and Resistance:
- PVD coatings are highly resistant to corrosion and oxidation, making them ideal for environments where hygiene and longevity are critical.
- The coatings are very thin (0.5 to 5 microns) and replicate the original finish of materials with minimal effort, ensuring consistent performance.
-
Safety During Application:
- While PVD coatings are safe once applied, the application process requires precautions to avoid inhaling particles.
- Proper ventilation and protective equipment are necessary during the coating process to ensure worker safety.
-
Material-Specific Properties:
- The properties of PVD coatings depend on the substrate material. For example, TiN coatings on Ti-6Al-4V alloy improve fatigue limits and endurance.
- Hardness is a key factor in determining the durability of PVD coatings, making them suitable for high-stress applications in the food industry.
In summary, PVD coatings are food-safe, durable, and widely used in the food industry for their protective and functional properties. Their inert nature and strong adhesion make them ideal for applications where food safety and longevity are paramount.
Summary Table:
Key Aspect | Details |
---|---|
Food Safety | Chemically and biologically inert, strong adhesion, no contamination risk. |
Applications | Cutlery, kitchen equipment, food packaging (e.g., aluminum-coated plastics). |
Durability & Resistance | Resistant to corrosion, oxidation, and wear; 0.5 to 5 microns thick. |
Safety During Application | Requires ventilation and protective gear; safe once applied. |
Material-Specific Properties | Substrate-dependent properties (e.g., TiN coatings improve fatigue limits). |
Interested in PVD coatings for your food-related applications? Contact us today to learn more!