Yes, pyrolysis and gasification are methods of converting biomass into energy and other valuable products. These processes fall under the category of thermochemical conversion, which involves the use of heat and chemical reactions to transform biomass into fuels, gases, and other byproducts. Pyrolysis heats biomass in the absence of oxygen to produce bio-oil, bio-char, and combustible gases, while gasification uses controlled amounts of oxygen and/or steam to produce syngas. Both methods are essential for converting organic materials like wood, agricultural waste, and other biomass into renewable energy sources, making them critical technologies in the transition to sustainable energy systems.
Key Points Explained:
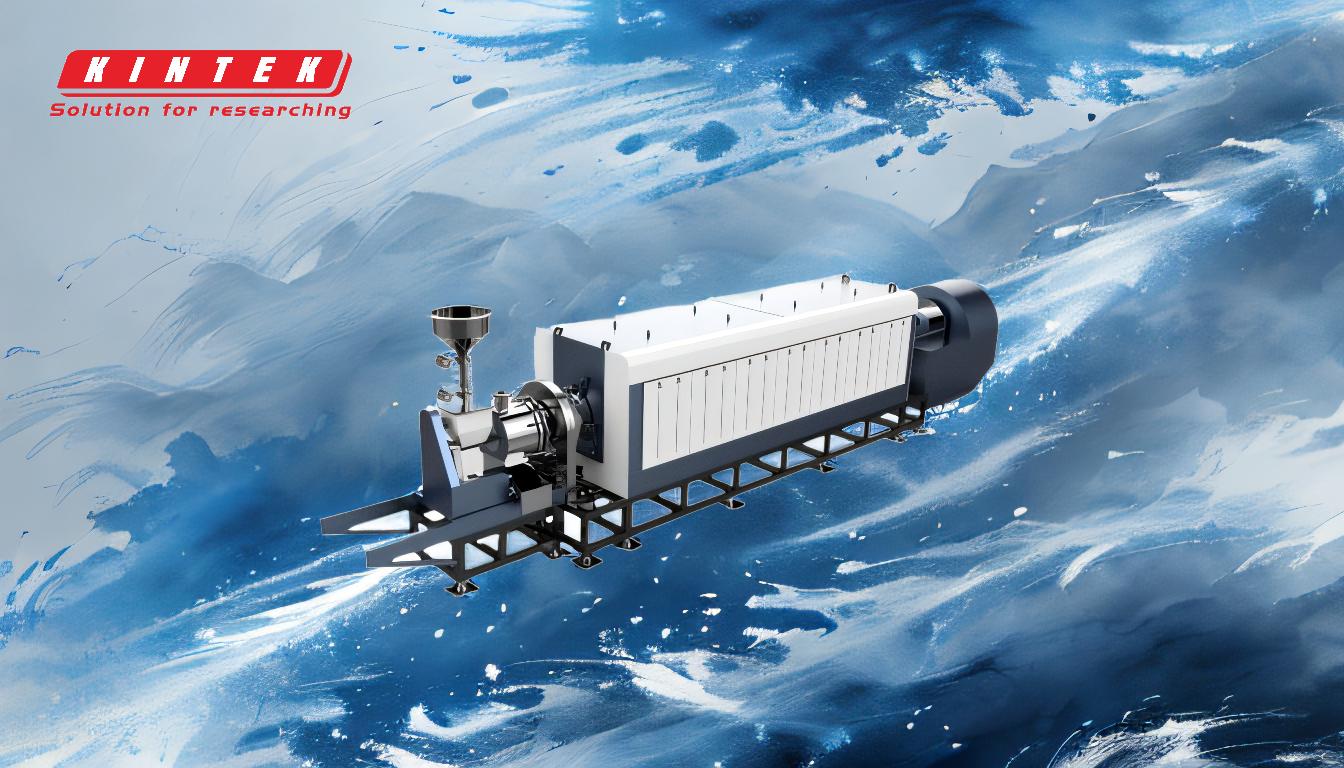
-
Definition of Biomass Conversion:
- Biomass conversion refers to the process of transforming organic materials, such as plants, trees, and agricultural waste, into useful energy sources or products. This can include renewable energy, biofuels, and other valuable materials.
- The conversion can occur through biological means (e.g., fermentation, anaerobic digestion) or thermochemical processes (e.g., pyrolysis, gasification).
-
Thermochemical Conversion Overview:
- Thermochemical conversion involves the application of heat and chemical reactions to break down biomass into energy-rich products.
- This category includes pyrolysis and gasification, which are distinct processes but share the common goal of converting biomass into usable energy forms.
-
Pyrolysis as a Biomass Conversion Method:
- Pyrolysis is a thermochemical process that heats biomass in the absence of oxygen (or with very limited oxygen) to temperatures typically between 800–900°F (or 500°C and above).
- The process decomposes biomass into three main products:
- Bio-oil: A liquid fuel that can be refined and used as a renewable energy source.
- Bio-char: A solid carbon-rich material that can be used as a soil amendment or for carbon sequestration.
- Combustible gases: Gases like methane and hydrogen that can be used for energy generation.
- Pyrolysis is particularly useful for producing intermediate liquid products that can be further processed into biofuels.
-
Gasification as a Biomass Conversion Method:
- Gasification involves heating biomass to higher temperatures (1,400–1,700°F) with controlled amounts of oxygen and/or steam.
- The primary product of gasification is syngas, a mixture of hydrogen, carbon monoxide, and other gases.
- Syngas can be used directly for electricity generation, as a fuel for engines, or as a precursor for producing liquid fuels and chemicals.
- Gasification is highly efficient and can handle a wide range of biomass feedstocks, making it a versatile technology for renewable energy production.
-
Comparison of Pyrolysis and Gasification:
- Temperature: Pyrolysis occurs at lower temperatures (800–900°F) compared to gasification (1,400–1,700°F).
- Oxygen Levels: Pyrolysis operates in the absence of oxygen, while gasification uses controlled amounts of oxygen and/or steam.
- Products: Pyrolysis produces bio-oil, bio-char, and combustible gases, whereas gasification primarily produces syngas.
- Applications: Pyrolysis is ideal for producing liquid biofuels and bio-char, while gasification is better suited for generating syngas for electricity and synthetic fuels.
-
Role in Renewable Energy Systems:
- Both pyrolysis and gasification play a crucial role in converting biomass into renewable energy, reducing reliance on fossil fuels.
- These processes help manage agricultural and forestry waste, turning it into valuable energy products and reducing environmental impact.
- The byproducts of these processes, such as bio-char and syngas, have additional applications in soil improvement, carbon sequestration, and industrial processes.
-
Environmental and Economic Benefits:
- Reduced Greenhouse Gas Emissions: By converting biomass into renewable energy, these processes help mitigate climate change by reducing carbon emissions.
- Waste Utilization: Pyrolysis and gasification provide sustainable ways to manage organic waste, reducing landfill use and pollution.
- Energy Independence: These technologies contribute to energy security by producing local, renewable energy sources.
-
Challenges and Considerations:
- Feedstock Variability: The efficiency of pyrolysis and gasification can vary depending on the type and quality of biomass used.
- Technology Costs: Initial investment and operational costs for these technologies can be high, though they are often offset by long-term energy savings.
- Scalability: While these processes are effective, scaling them up for industrial use requires careful planning and infrastructure development.
In summary, pyrolysis and gasification are essential thermochemical methods for converting biomass into renewable energy and other valuable products. They offer significant environmental and economic benefits, making them key technologies in the transition to a sustainable energy future.
Summary Table:
Aspect | Pyrolysis | Gasification |
---|---|---|
Temperature | 800–900°F (500°C and above) | 1,400–1,700°F |
Oxygen Levels | Absence of oxygen | Controlled amounts of oxygen and/or steam |
Main Products | Bio-oil, bio-char, combustible gases | Syngas (hydrogen, carbon monoxide, and other gases) |
Applications | Liquid biofuels, bio-char for soil improvement | Electricity generation, synthetic fuels, and industrial processes |
Environmental Impact | Reduces greenhouse gas emissions, manages organic waste | Efficient waste utilization, reduces reliance on fossil fuels |
Challenges | Feedstock variability, high initial costs | Scalability, operational costs |
Discover how pyrolysis and gasification can transform your biomass into renewable energy—contact us today to learn more!