Pyrolysis of plastic can be safe if proper safety measures, protocols, and systems are implemented. However, it involves inherent risks due to the high temperatures, flammable gases, and toxic byproducts generated during the process. Key risks include fire, explosion, toxic gas release, and occupational hazards. To ensure safety, operators must adhere to strict regulations, use appropriate personal protective equipment (PPE), maintain equipment, and implement robust safety management systems. Inert gas purging, careful monitoring, and proper training are critical to mitigating risks during startup, shutdown, and operational upsets. With these precautions, pyrolysis can be conducted safely.
Key Points Explained:
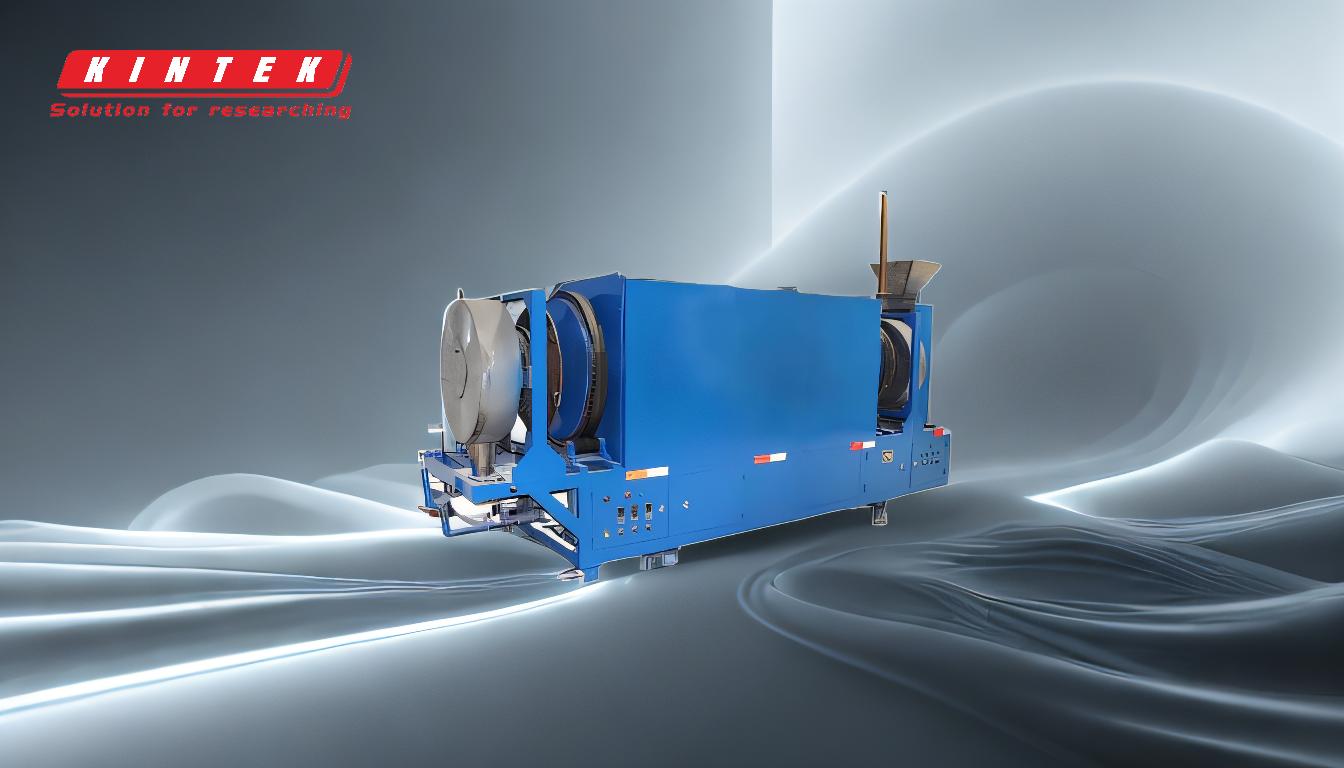
-
Inherent Risks of Pyrolysis:
- Pyrolysis involves heating plastic to high temperatures, often exceeding the autoignition temperature of the produced gases. This creates a risk of fire or explosion if oxygen is present.
- Toxic gases, primarily carbon monoxide, are released during the process, posing health hazards to workers and the environment.
- Risks are highest during system startup, shutdown, intermittent operation, or operational upsets, where improper handling can lead to accidents.
-
Critical Safety Measures:
- Inert Gas Purging: To prevent explosions, inert gases (e.g., nitrogen) are used to purge oxygen from the system. This is essential during all phases of operation.
- Temperature and Pressure Monitoring: Continuous monitoring and control of high temperatures and pressures are necessary to prevent system failures.
- Emission Control: Proper systems must be in place to capture and treat toxic gases and other emissions to protect workers and the environment.
-
Equipment and Process Safety:
- Regular maintenance and inspections of pyrolysis equipment are crucial to prevent malfunctions that could lead to accidents.
- Safety management systems should be implemented to identify, assess, and mitigate risks throughout the process.
- Compliance with local regulations and obtaining necessary permits ensures that the facility meets safety standards.
-
Occupational Safety:
- Workers must wear appropriate PPE, including heat-resistant gloves, goggles, and respiratory protection, to safeguard against high temperatures, toxic gases, and physical hazards.
- Proper training on safety protocols and emergency procedures is essential to minimize human error and ensure safe operations.
- Handling sharp or heavy objects, as well as managing waste storage, requires careful attention to prevent injuries.
-
Fire and Explosion Hazards:
- The risk of fire and explosion is inherent in pyrolysis due to the flammable nature of the gases produced. Strict control of oxygen levels and proper system design are critical.
- Fire suppression systems and emergency shutdown procedures must be in place to respond quickly to any incidents.
-
Environmental and Regulatory Compliance:
- Pyrolysis plants must address emission control issues to prevent the release of harmful substances into the environment.
- Waste handling and storage must comply with regulations to avoid contamination and other environmental hazards.
- Regular audits and inspections ensure ongoing compliance with safety and environmental standards.
-
Operational Best Practices:
- Implementing a culture of safety, where all workers are aware of risks and committed to following protocols, is essential.
- Conducting risk assessments and hazard analyses before starting operations helps identify potential issues and implement preventive measures.
- Emergency response plans should be developed and regularly practiced to ensure preparedness for any incidents.
By addressing these key points, pyrolysis of plastic can be conducted safely, minimizing risks to workers, the environment, and the surrounding community.
Summary Table:
Key Aspect | Details |
---|---|
Inherent Risks | Fire, explosion, toxic gas release, and occupational hazards. |
Critical Safety Measures | Inert gas purging, temperature/pressure monitoring, emission control. |
Equipment Safety | Regular maintenance, safety management systems, regulatory compliance. |
Occupational Safety | PPE, proper training, handling sharp/heavy objects, waste storage. |
Fire/Explosion Hazards | Control oxygen levels, fire suppression systems, emergency shutdown plans. |
Environmental Compliance | Emission control, waste handling, regular audits, and inspections. |
Operational Best Practices | Safety culture, risk assessments, emergency response plans. |
Ensure your pyrolysis operations are safe and compliant—contact our experts today for guidance!