Ball mill efficiency is influenced by a variety of factors, including the design and operational parameters of the mill, the properties of the material being ground, and the characteristics of the grinding media. Key factors include the drum diameter and length ratio, rotation speed, ball filling ratio, size and type of grinding media, and the physical-chemical properties of the feed material. Additionally, the timely removal of ground product, the hardness and size of the material, and the feed rate also play significant roles. Understanding and optimizing these factors can significantly enhance the grinding performance and overall efficiency of a ball mill.
Key Points Explained:
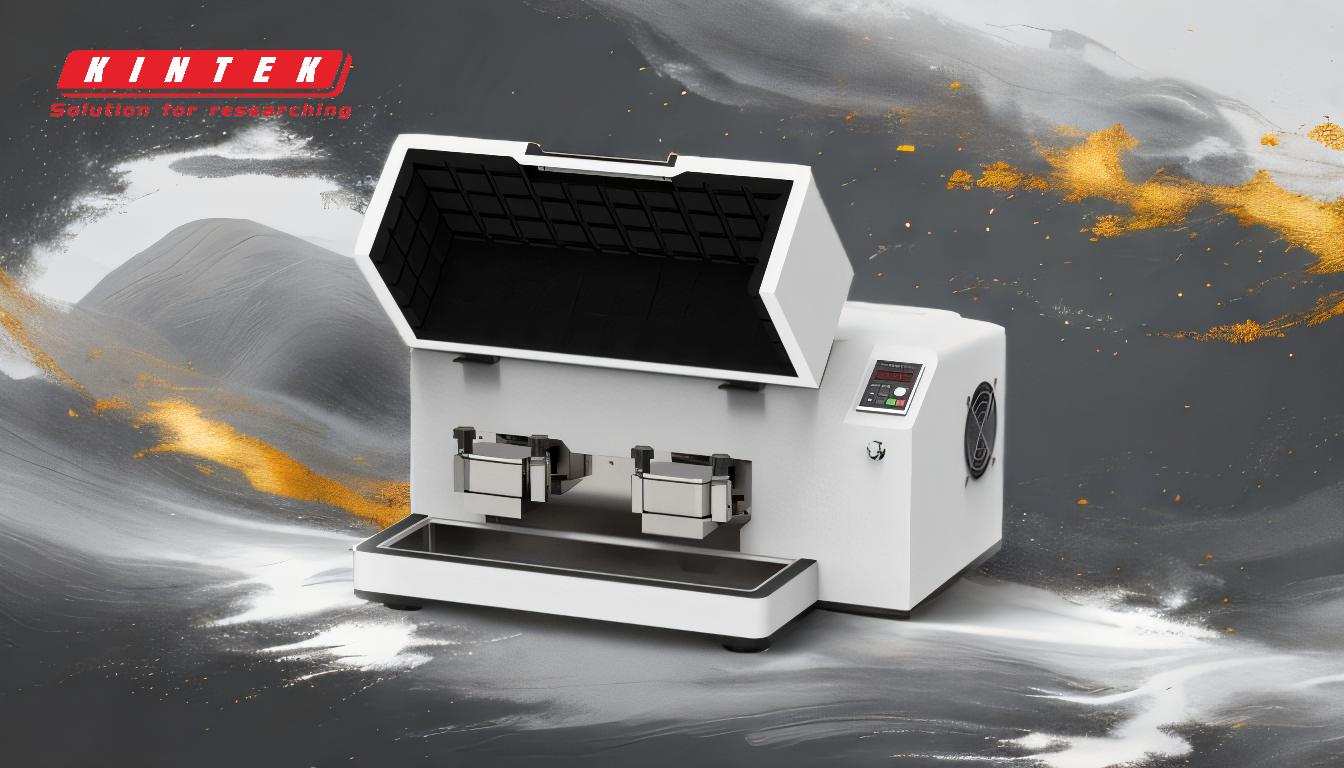
-
Drum Diameter and Length Ratio (L:D Ratio)
- The productivity of ball mills is highly dependent on the drum diameter and the ratio of drum diameter to length. An optimal L:D ratio is typically between 1.56 and 1.64. This ratio affects the residence time of the material in the mill and the efficiency of the grinding process. A well-balanced L:D ratio ensures that the material is adequately ground without overloading the mill.
-
Rotation Speed
- The speed at which the ball mill rotates is crucial for its efficiency. The rotation speed affects the motion of the grinding media and the material inside the mill. If the speed is too low, the grinding media will not be lifted sufficiently, leading to inefficient grinding. Conversely, if the speed is too high, the grinding media may centrifuge, reducing the grinding action. The optimal rotation speed depends on the mill's diameter and the size of the grinding media.
-
Ball Filling Ratio and Sizes
- The filling ratio, which is the percentage of the mill volume filled with grinding media (balls), directly impacts the grinding efficiency. An appropriate filling ratio ensures that there is enough media to grind the material effectively without causing excessive wear on the mill. The size of the balls also matters; larger balls are more effective for coarse grinding, while smaller balls are better for fine grinding. The combination of different ball sizes can optimize the grinding process.
-
Physical-Chemical Properties of Feed Material
- The nature of the material being ground, including its hardness, mechanical strength, and embedding characteristics, significantly affects the grinding efficiency. Harder materials require more energy to grind, while softer materials may be ground more easily. The grindability coefficient of the ore, which is influenced by its mechanical strength and embedding characteristics, also plays a role in determining the efficiency of the grinding process.
-
Armor Surface Shape
- The shape and design of the mill's internal armor surface can influence the grinding efficiency. A well-designed armor surface can enhance the lifting and cascading action of the grinding media, leading to more effective grinding. The surface shape also affects the wear rate of the mill lining, which can impact the long-term efficiency of the mill.
-
Milling Fineness and Timely Removal of Ground Product
- The desired fineness of the ground product affects the grinding process. Finer grinding requires more energy and time. Additionally, the timely removal of the ground product from the mill is crucial to prevent over-grinding and to maintain the efficiency of the mill. Over-grinding can lead to excessive energy consumption and reduced throughput.
-
Residence Time and Feed Rate
- The residence time of the material in the mill chamber, which is influenced by the feed rate and the level of material in the vessel, affects the degree of milling. A longer residence time allows for more thorough grinding but may reduce the mill's throughput. The feed rate must be balanced to ensure that the material is ground to the desired fineness without overloading the mill.
-
Size, Density, and Number of Balls
- The size, density, and number of balls in the mill influence the grinding efficiency. Larger and denser balls can provide more impact force, which is beneficial for grinding harder materials. However, too many balls can lead to overcrowding, reducing the effective grinding action. The optimal number and size of balls depend on the material being ground and the desired fineness.
-
Hardness of the Grinding Material
- The hardness of the grinding material affects the wear rate of the grinding media and the mill lining. Harder materials can cause more wear, leading to increased maintenance costs and reduced efficiency. The choice of grinding media and mill lining materials should consider the hardness of the material being ground to minimize wear and maximize efficiency.
-
Feed Size and Product Size
- The size of the feed material and the desired product size influence the grinding efficiency. Larger feed sizes require more energy to grind, while finer product sizes demand more precise control over the grinding process. The feed size should be optimized to achieve the desired product size with minimal energy consumption.
By carefully considering and optimizing these factors, the efficiency of a ball mill can be significantly improved, leading to better grinding performance, reduced energy consumption, and lower operational costs.
Summary Table:
Factor | Impact on Efficiency |
---|---|
Drum Diameter and Length Ratio | Affects residence time and grinding efficiency; optimal L:D ratio is 1.56–1.64. |
Rotation Speed | Determines grinding media motion; too low or high speeds reduce efficiency. |
Ball Filling Ratio and Sizes | Influences grinding effectiveness; larger balls for coarse grinding, smaller for fine. |
Feed Material Properties | Hardness and mechanical strength affect energy consumption and grindability. |
Armor Surface Shape | Enhances media lifting and cascading; impacts wear rate and long-term efficiency. |
Milling Fineness | Finer grinding requires more energy; timely removal prevents over-grinding. |
Residence Time and Feed Rate | Longer residence time improves grinding but may reduce throughput. |
Ball Size, Density, and Number | Larger, denser balls provide more impact force; overcrowding reduces efficiency. |
Hardness of Grinding Material | Harder materials increase wear; media and lining choices should minimize wear. |
Feed Size and Product Size | Larger feed sizes require more energy; finer product sizes demand precise control. |
Optimize your ball mill efficiency today—contact our experts for tailored solutions!