Molds are critical tools in manufacturing, primarily used to shape materials into specific forms during mass production. They are widely employed in processes like injection molding, where they shape molten resin into desired products, and in casting, where they form metals or other materials into precise shapes. Molds enable the efficient and consistent production of complex parts, making them indispensable in industries ranging from automotive to consumer goods.
Key Points Explained:
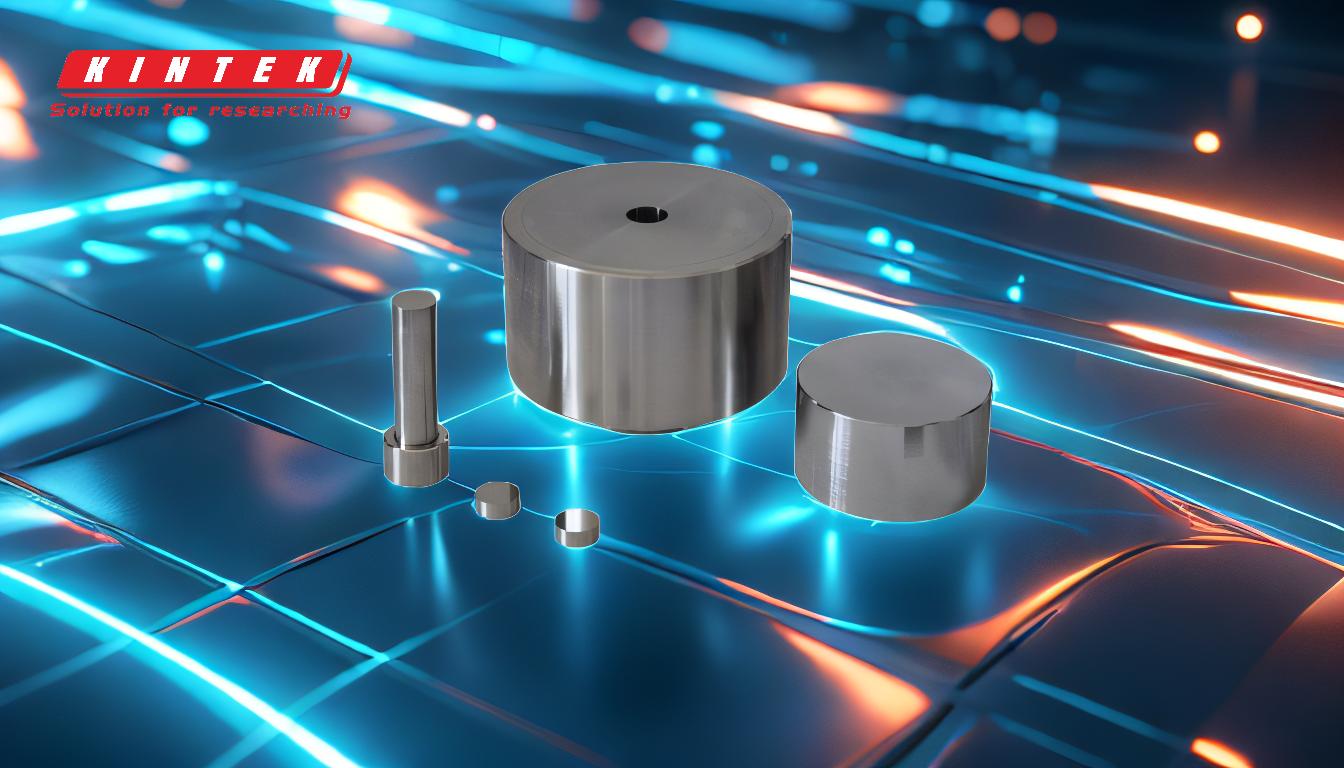
-
Definition and Purpose of Molds:
- Molds are tools designed to shape materials into specific forms or structures.
- They are essential in mass production, ensuring consistency, precision, and efficiency in manufacturing processes.
-
Common Applications of Molds:
- Injection Molding: Molds are used to shape molten resin or plastic into products. This process is widely used for creating items like plastic containers, automotive parts, and consumer goods.
- Casting: Molds are used in metal casting to form metals or alloys into desired shapes. This is common in industries like aerospace, automotive, and jewelry making.
- Other Processes: Molds are also used in processes like blow molding (for hollow objects), compression molding (for thermosetting plastics), and rotational molding (for large, hollow parts).
-
Advantages of Using Molds:
- Precision and Consistency: Molds allow for the production of highly accurate and uniform parts, which is crucial for industries with strict quality standards.
- Efficiency: Molds enable high-volume production, reducing manufacturing time and costs.
- Versatility: Molds can be designed to create complex geometries and intricate details, making them suitable for a wide range of applications.
-
Materials Used for Molds:
- Molds are typically made from durable materials like steel, aluminum, or silicone, depending on the application and the material being shaped.
- The choice of mold material depends on factors like the production volume, the type of material being molded, and the required precision.
-
Industries That Rely on Molds:
- Automotive: Molds are used to produce components like dashboards, bumpers, and engine parts.
- Consumer Goods: Items like plastic bottles, toys, and household appliances are often made using molds.
- Medical: Molds are used to create medical devices and components with high precision.
- Aerospace: Molds are essential for producing lightweight, high-strength components for aircraft.
-
Future Trends in Mold Technology:
- 3D Printing: Advances in 3D printing are enabling the creation of complex molds with reduced lead times and costs.
- Smart Molds: Integration of sensors and IoT technology into molds is improving process monitoring and quality control.
- Sustainable Materials: There is a growing focus on using eco-friendly materials for molds and reducing waste in manufacturing processes.
In summary, molds are indispensable tools in modern manufacturing, enabling the mass production of precise, consistent, and complex parts across a wide range of industries. Their versatility, efficiency, and ability to meet high-quality standards make them a cornerstone of industrial production.
Summary Table:
Aspect | Details |
---|---|
Definition | Tools designed to shape materials into specific forms or structures. |
Applications | Injection molding, casting, blow molding, compression molding, rotational molding. |
Advantages | Precision, consistency, efficiency, and versatility in production. |
Materials | Steel, aluminum, silicone, chosen based on application and precision needs. |
Industries | Automotive, consumer goods, medical, aerospace. |
Future Trends | 3D printing, smart molds, sustainable materials. |
Ready to enhance your manufacturing process with precision molds? Contact us today to learn more!