Powder metallurgy (PM) is a versatile manufacturing technique with several advantages, but it also has notable limitations. These include size restrictions due to press capacity, challenges in producing complex-shaped parts, and generally lower strength and ductility compared to cast or forged components. Additionally, secondary finishing requirements can increase production time and costs. Despite these limitations, PM remains a valuable method for producing a wide range of metal components.
Key Points Explained:
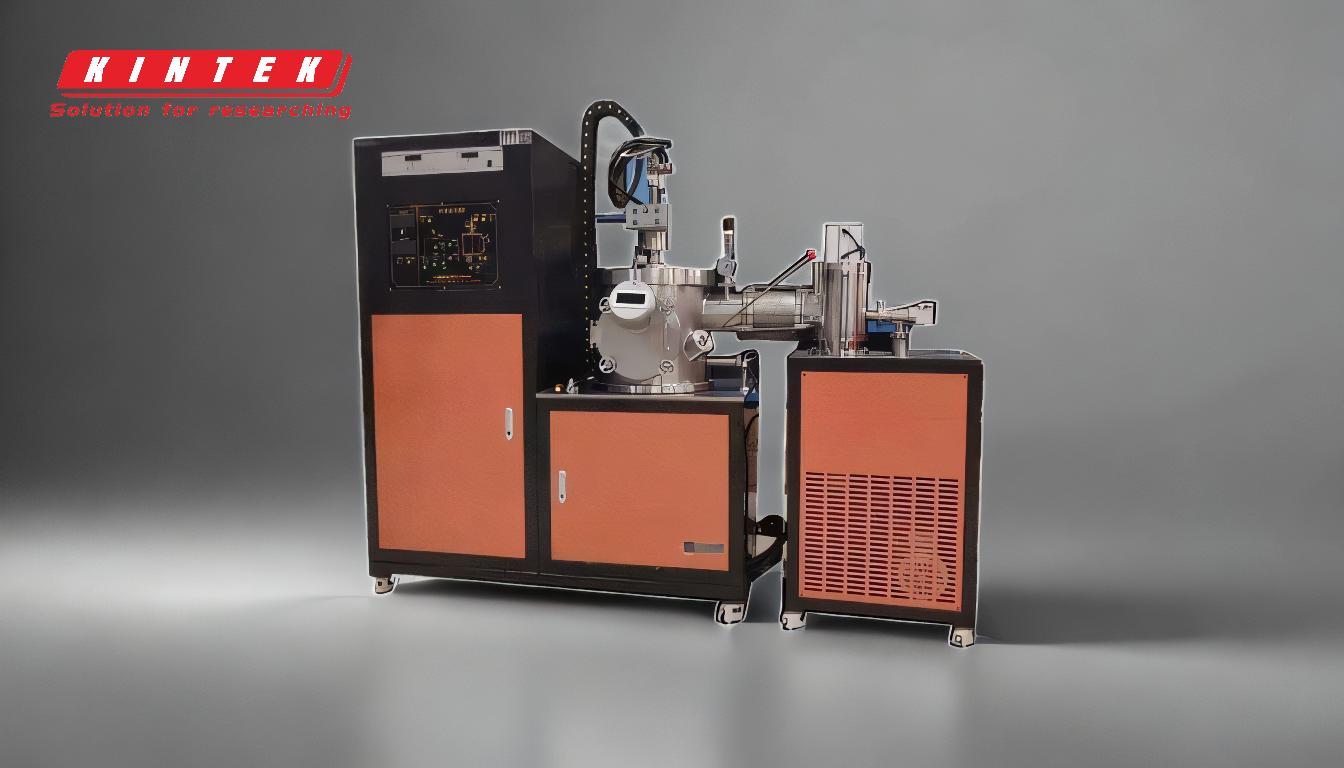
-
Size Limitations:
- Press Capacity: The largest presses in the powder metallurgy industry are about 1,500 tons, which limits the practical size of parts to approximately 40-50 square inches of planar area. This constraint can be a significant drawback when manufacturing larger components.
- Impact on Design: Engineers and designers must consider these size limitations when planning parts, potentially requiring alternative manufacturing methods for larger components.
-
Complex-Shaped Parts:
- Production Challenges: Creating complex-shaped parts can be difficult with powder metallurgy. The process involves compacting metal powder into a die, which may not always accommodate intricate geometries.
- Manufacturer Expertise: While skilled manufacturers can overcome some of these challenges, the complexity of the part often increases production time and costs.
-
Mechanical Properties:
- Strength and Ductility: PM parts generally do not match the strength and ductility of parts produced by casting or forging. This is due to the inherent porosity in PM components, which can reduce mechanical performance.
- Material Limitations: Although PM can use a wide range of metals, the final properties of the parts may not meet the requirements for high-stress applications.
-
Secondary Finishing Requirements:
- Additional Processing: Powder metallurgy injection molding often requires significant secondary finishing, such as machining, heat treatment, or surface coating, to achieve the desired final properties and surface finish.
- Cost and Time: These additional steps can increase the overall production time and cost, making PM less economical for some applications.
-
Versatility in Material Use:
- Wide Range of Materials: Despite the limitations, PM is versatile in terms of the types of metals that can be used. This includes various alloys and composite materials, making it suitable for a broad spectrum of applications.
- Material Selection: The ability to use different materials allows for customization based on specific application requirements, though the final properties may still be limited by the PM process.
-
Economic Considerations:
- Cost-Effectiveness: For high-volume production of relatively simple parts, PM can be cost-effective. However, for low-volume or highly complex parts, the costs associated with tooling and secondary finishing may outweigh the benefits.
- Market Demand: The economic viability of PM also depends on market demand and the specific requirements of the end-use application.
In summary, while powder metallurgy offers several advantages, including material versatility and cost-effectiveness for certain applications, it also has significant limitations. These include size restrictions, challenges in producing complex shapes, and generally lower mechanical properties compared to other manufacturing methods. Understanding these limitations is crucial for making informed decisions about when and how to use powder metallurgy in manufacturing.
Summary Table:
Limitation | Details |
---|---|
Size Restrictions | Limited by press capacity (up to 1,500 tons), restricting part size. |
Complex-Shaped Parts | Difficult to produce intricate geometries; increases production time and cost. |
Mechanical Properties | Lower strength and ductility compared to cast or forged parts. |
Secondary Finishing | Requires additional processing, increasing time and cost. |
Material Versatility | Wide range of metals usable, but final properties may be limited. |
Economic Considerations | Cost-effective for high-volume, simple parts; less so for complex designs. |
Need help deciding if powder metallurgy is right for your project? Contact our experts today!