A controlled atmosphere furnace is highly desirable in sintering due to its ability to provide precise temperature control, minimize oxidation or contamination, and create an optimal environment for achieving desired material properties. This type of furnace ensures consistent results, improved product quality, and enhanced production efficiency. By maintaining specific gas mixtures and thermal conditions, it prevents unwanted chemical reactions, retains alloy properties, and supports energy-efficient and environmentally friendly operations. These benefits make it indispensable for sintering processes where material integrity and performance are critical.
Key Points Explained:
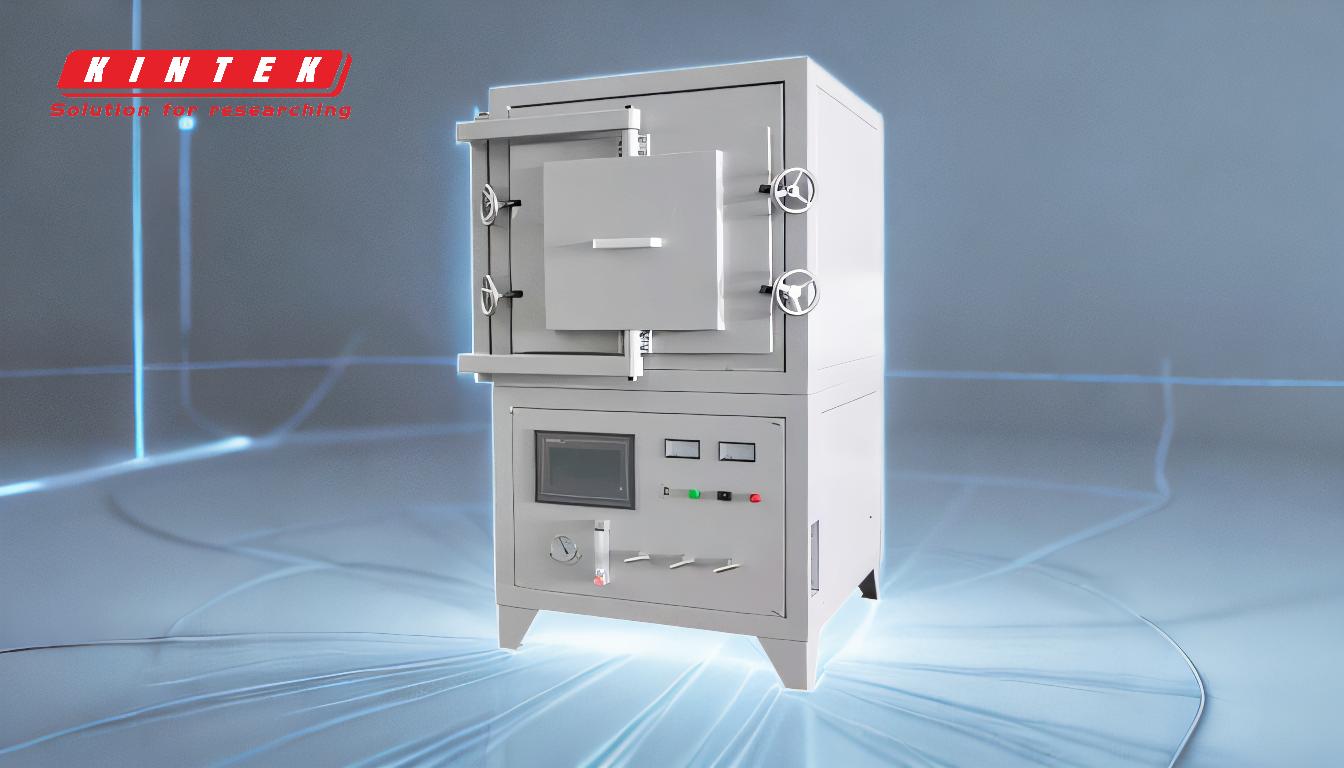
-
Precise Temperature Control
- A controlled atmosphere furnace offers highly accurate temperature regulation, which is crucial for sintering. This ensures that materials are heated and cooled uniformly, preventing defects and ensuring consistent results.
- The tightly sealed environment allows for precise adjustments, enabling the creation of specific thermal profiles tailored to the material being processed.
-
Minimized Oxidation and Contamination
- The controlled atmosphere prevents exposure to oxygen, which can cause oxidation or decarburization. This is particularly important for metals and alloys, as it preserves their strength, ductility, and other desired properties.
- By maintaining a protective or reactive atmosphere, the furnace eliminates contamination from external elements, ensuring the purity and integrity of the sintered product.
-
Optimized Material Properties
- The ability to control the atmosphere allows for the creation of specific gas mixtures that enhance material properties during sintering. For example, inert gases like argon or nitrogen can prevent unwanted chemical reactions, while reactive gases can promote desired transformations.
- This control ensures that the final product meets stringent quality standards and retains its intended mechanical and chemical characteristics.
-
Energy Efficiency and Environmental Benefits
- Controlled atmosphere furnaces are designed to operate efficiently, reducing energy consumption and operating costs. This is achieved through advanced insulation, precise controls, and optimized heating cycles.
- The environmentally friendly design minimizes emissions and waste, aligning with sustainable manufacturing practices.
-
Versatility and Adaptability
- These furnaces can handle parts of all shapes and sizes, making them suitable for a wide range of sintering applications. Their flexibility allows for easy adjustment of parameters such as temperature, time, and pressure to achieve optimal conditions.
- This adaptability ensures that the furnace can be used for various materials and processes, from metal sintering to ceramic processing.
-
Enhanced Safety and Reliability
- Controlled atmosphere furnaces are equipped with advanced safety devices, such as gas leak detectors and emergency shut-off systems, ensuring safe operation.
- The reliability of these furnaces reduces downtime and maintenance requirements, contributing to increased production efficiency and cost savings.
-
Improved Product Consistency and Quality
- The combination of precise temperature control, minimized contamination, and optimized gas mixtures results in consistent and high-quality sintered products.
- This consistency is critical for industries where material performance and reliability are paramount, such as aerospace, automotive, and medical device manufacturing.
By leveraging the capabilities of a controlled atmosphere furnace, manufacturers can achieve superior sintering outcomes, ensuring that their products meet the highest standards of quality and performance.
Summary Table:
Key Benefits | Description |
---|---|
Precise Temperature Control | Ensures uniform heating and cooling, preventing defects and ensuring consistency. |
Minimized Oxidation and Contamination | Prevents oxidation and contamination, preserving material integrity. |
Optimized Material Properties | Enhances material properties with controlled gas mixtures. |
Energy Efficiency | Reduces energy consumption and operating costs. |
Versatility and Adaptability | Suitable for various materials and sintering applications. |
Enhanced Safety and Reliability | Equipped with advanced safety features for reliable operation. |
Improved Product Consistency | Ensures high-quality, consistent sintered products. |
Ready to enhance your sintering process? Contact us today to learn more about our controlled atmosphere furnaces!