Atomic Layer Deposition (ALD) is a highly advanced thin-film deposition technique that offers unique advantages, such as the ability to produce ultra-thin, uniform, and conformal coatings on complex geometries, including nanoparticles and curved surfaces. However, it also has its limitations, such as being a slower process compared to other deposition methods and requiring precise control and expertise. Below, we explore the key advantages and disadvantages of ALD in detail.
Key Points Explained:
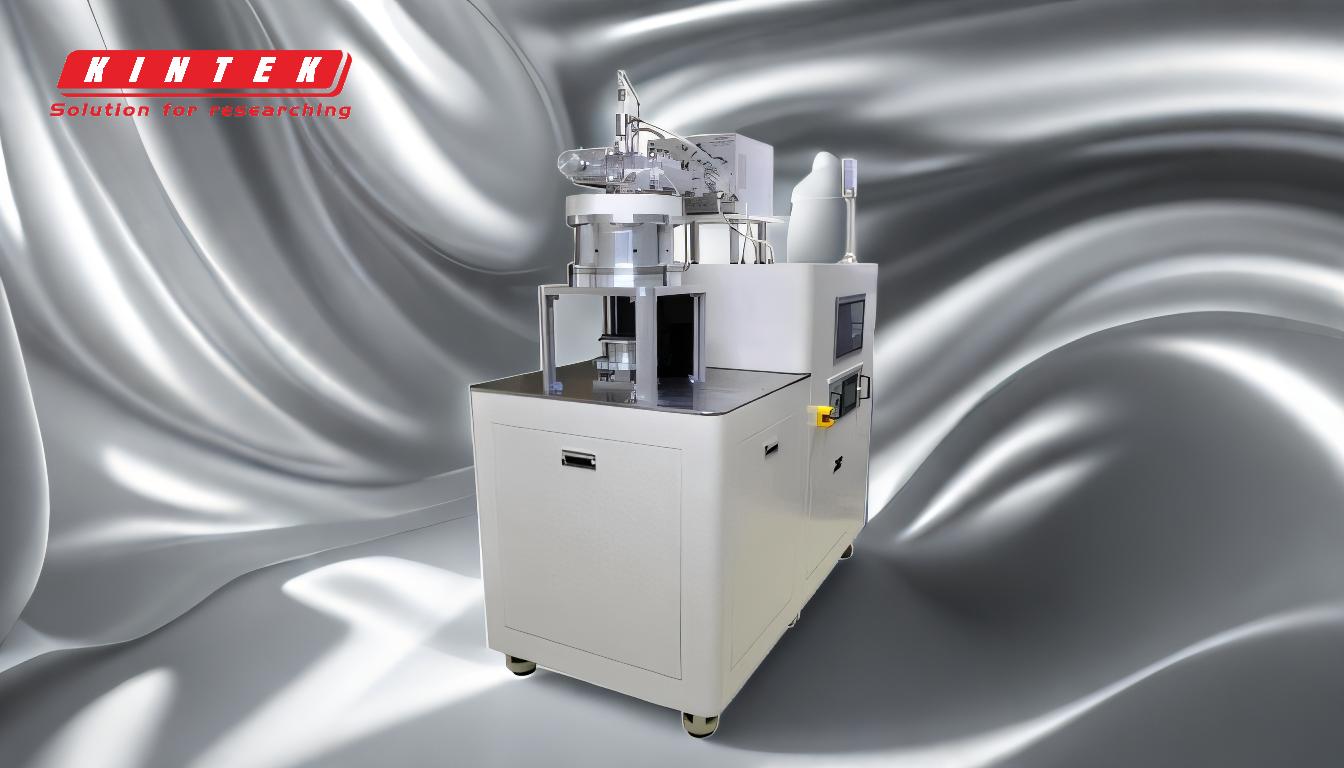
-
Advantages of ALD
- Uniform and Conformal Coatings: ALD excels in depositing highly uniform and conformal films, even on complex geometries, nanoparticles, and curved surfaces. This makes it ideal for applications requiring precise and consistent thin-film coatings.
- Atomic-Level Precision: ALD allows for precise control over film thickness at the atomic level, enabling the creation of multi-layer structures with exceptional accuracy.
- Versatility: ALD can deposit a wide range of materials, including oxides, nitrides, and metals, making it suitable for diverse applications in electronics, energy storage, and catalysis.
- Low-Temperature Processing: ALD can often be performed at relatively low temperatures, making it compatible with temperature-sensitive substrates.
-
Disadvantages of ALD
- Slow Deposition Rate: ALD is a sequential process that involves alternating precursor and reactant pulses, making it significantly slower than other deposition techniques like Chemical Vapor Deposition (CVD).
- Complexity and Cost: The process requires precise control of precursor delivery, vacuum conditions, and reaction parameters, necessitating specialized equipment and expertise. This increases operational complexity and cost.
- Limited Material Selection: While ALD can deposit many materials, the availability of suitable precursors for certain materials can be a limiting factor.
- Scalability Challenges: Scaling ALD for high-throughput industrial applications can be challenging due to its inherently slow deposition rate and the need for precise process control.
-
Process Steps in ALD
- Step 1: Precursor Introduction: A precursor gas is introduced into the chamber, forming a chemically bound monolayer on the substrate surface.
- Step 2: Purging: Excess precursor is removed by evacuating and purging the chamber.
- Step 3: Reactant Introduction: A reactant gas is introduced to react with the adsorbed precursor, forming the desired film.
- Step 4: By-Product Removal: Reaction by-products are pumped away, completing one ALD cycle.
-
Applications of ALD
- Semiconductors: ALD is widely used in the semiconductor industry for depositing high-k dielectrics, gate oxides, and barrier layers.
- Energy Storage: It is employed in the fabrication of advanced battery electrodes and solid-state electrolytes.
- Catalysis: ALD is used to create highly efficient catalysts by depositing uniform coatings on nanoparticle surfaces.
- Optics and Coatings: ALD is used for anti-reflective coatings, protective layers, and optical filters.
-
Future Prospects
- Improved Precursors: Research is ongoing to develop new precursors that expand the range of materials that can be deposited via ALD.
- High-Throughput ALD: Efforts are being made to increase deposition rates and scalability for industrial applications.
- Hybrid Techniques: Combining ALD with other deposition methods, such as CVD or Physical Vapor Deposition (PVD), could enhance its versatility and efficiency.
In summary, ALD is a powerful technique for depositing ultra-thin, uniform, and conformal films with atomic-level precision. While it offers significant advantages in terms of film quality and versatility, its slow deposition rate, complexity, and cost are notable drawbacks. Understanding these trade-offs is essential for selecting ALD as the appropriate deposition method for specific applications.
Summary Table:
Aspect | Advantages | Disadvantages |
---|---|---|
Uniformity | Deposits ultra-thin, uniform, and conformal coatings on complex geometries. | Slow deposition rate compared to other methods like CVD. |
Precision | Enables atomic-level control over film thickness and multi-layer structures. | Requires precise control, specialized equipment, and expertise. |
Versatility | Deposits a wide range of materials (oxides, nitrides, metals). | Limited by the availability of suitable precursors for certain materials. |
Temperature | Can operate at low temperatures, suitable for sensitive substrates. | High operational complexity and cost. |
Scalability | Ideal for high-precision applications like semiconductors and catalysis. | Scaling for high-throughput industrial applications is challenging. |
Interested in how ALD can benefit your project? Contact us today to learn more!