Evaporative deposition is a widely used technique for creating thin film coatings with specific properties, offering precise control over film thickness and composition. However, it also has limitations, such as sensitivity to contamination and challenges in scalability. This process is particularly useful for applications requiring high-quality, uniform films across a variety of materials, including metals, ceramics, and semiconductors. Despite its advantages, the need for a high-vacuum environment and potential issues with impurity levels and film stress must be considered when choosing this method.
Key Points Explained:
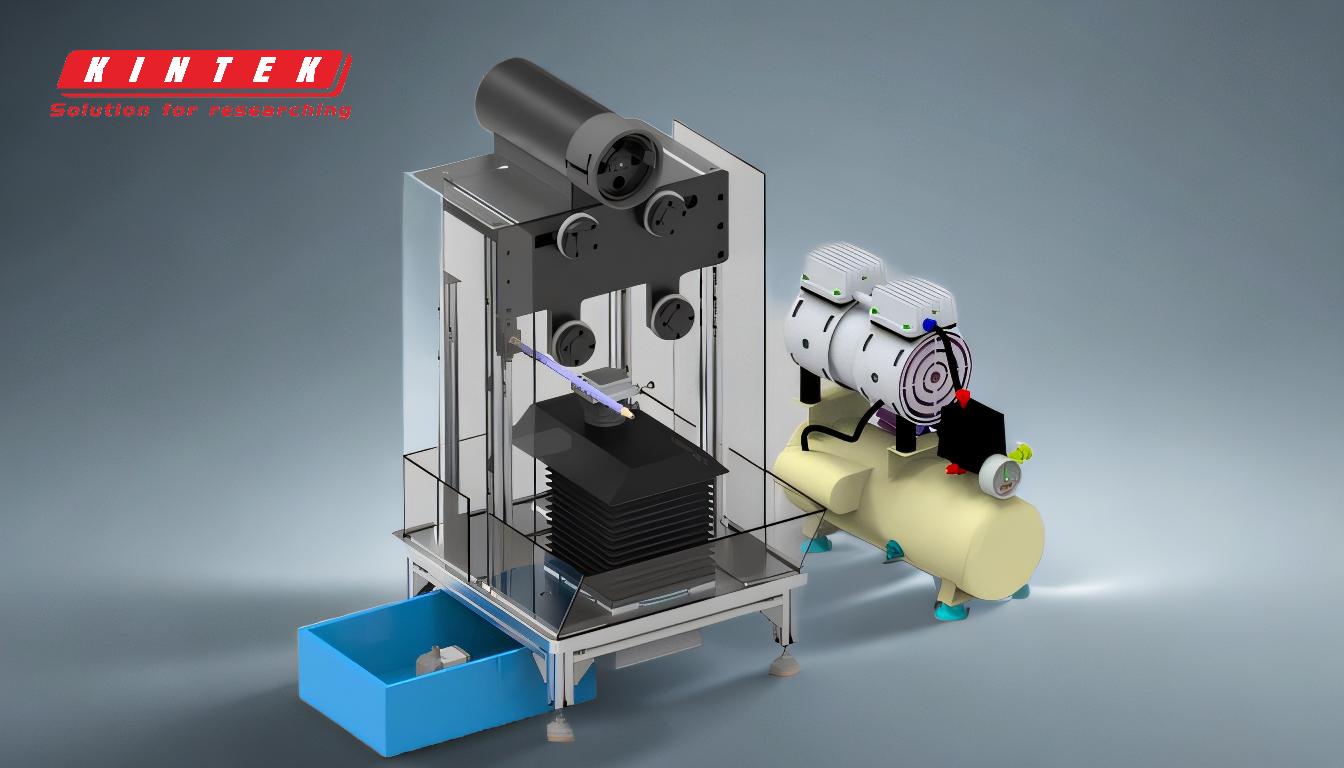
-
Precise Control of Film Thickness and Composition:
- Advantage: Evaporative deposition allows for precise control over the thickness and composition of the deposited film. This is achieved by carefully managing the vapor pressure of the source material and the temperature of the substrate. Such control is crucial for applications requiring specific film properties, such as insulation, conductivity, or wear resistance.
- Implication: This precision enables the creation of highly specialized coatings, making the technique valuable in industries like electronics, optics, and aerospace.
-
High-Quality Thin Films:
- Advantage: The process is capable of producing high-quality thin films with good uniformity and conformity. This ensures that the films have consistent properties across the entire substrate, which is essential for reliable performance in various applications.
- Implication: High-quality films are particularly important in industries such as semiconductor manufacturing, where even minor inconsistencies can lead to significant performance issues.
-
Versatility in Material Deposition:
- Advantage: Evaporative deposition can deposit a wide range of materials, including metals, ceramics, and semiconductors. This versatility makes it a valuable tool for creating coatings with diverse functional properties.
- Implication: The ability to work with various materials broadens the application scope of evaporative deposition, allowing it to be used in different technological fields, from electronics to protective coatings.
-
Requirement for High-Vacuum Environment:
- Disadvantage: The process requires a high-vacuum environment to prevent contamination and ensure the purity of the deposited film. This requirement can increase the complexity and cost of the equipment needed.
- Implication: The need for a high-vacuum setup can limit the accessibility of the technique for smaller-scale operations or industries where cost is a significant constraint.
-
Sensitivity to Contamination:
- Disadvantage: Evaporative deposition is highly sensitive to contamination, which can affect the quality and performance of the thin films. Even minor impurities can lead to defects in the film, impacting its functional properties.
- Implication: This sensitivity necessitates stringent control over the deposition environment, adding to the operational challenges and costs.
-
Limited Scalability:
- Disadvantage: The technique has limitations in terms of scalability, particularly when compared to other deposition methods. This can restrict its use in large-scale production environments.
- Implication: For industries requiring mass production, the limited scalability of evaporative deposition may make it less attractive compared to alternative methods that can handle larger volumes more efficiently.
-
Film Quality and Stress:
- Disadvantage: The films produced by evaporative deposition can have issues with density and stress. Low-density films and moderate film stress can affect the mechanical and functional properties of the coating.
- Implication: These issues may necessitate additional post-deposition treatments or limit the use of evaporative deposition in applications where mechanical integrity is critical.
-
Uniformity Challenges Without Additional Systems:
- Disadvantage: Achieving good film uniformity can be challenging without the use of masks and planetary systems. These additional systems can increase the complexity and cost of the deposition process.
- Implication: The need for such systems to achieve uniformity can be a drawback, especially in applications where cost and simplicity are prioritized.
In summary, evaporative deposition offers significant advantages in terms of precision, quality, and material versatility, making it a valuable technique for creating specialized thin films. However, the need for a high-vacuum environment, sensitivity to contamination, and challenges with scalability and film quality must be carefully considered when selecting this method for specific applications.
Summary Table:
Aspect | Advantages | Disadvantages |
---|---|---|
Precise Control | Enables exact thickness and composition for specialized coatings. | Requires high-vacuum environment, increasing complexity and cost. |
High-Quality Films | Produces uniform, consistent films essential for reliable performance. | Sensitive to contamination, leading to potential defects. |
Material Versatility | Deposits metals, ceramics, and semiconductors for diverse applications. | Limited scalability, making it less suitable for large-scale production. |
Film Quality | Ideal for industries like electronics and aerospace. | Issues with film density and stress may require post-deposition treatments. |
Uniformity | Ensures consistent properties across substrates. | Achieving uniformity often requires additional systems, increasing costs. |
Discover how evaporative deposition can enhance your thin film applications—contact our experts today for tailored solutions!