Sheet metal is a versatile material widely used in various industries due to its unique properties and adaptability. It is formed by rolling or pressing metal into thin, flat pieces, making it suitable for a range of applications from construction to automotive manufacturing. The advantages of sheet metal include its strength, durability, and cost-effectiveness, while its disadvantages involve limitations in design complexity and susceptibility to corrosion. Its uses span across industries, including HVAC systems, automotive bodies, and electronic enclosures, showcasing its importance in modern manufacturing and construction.
Key Points Explained:
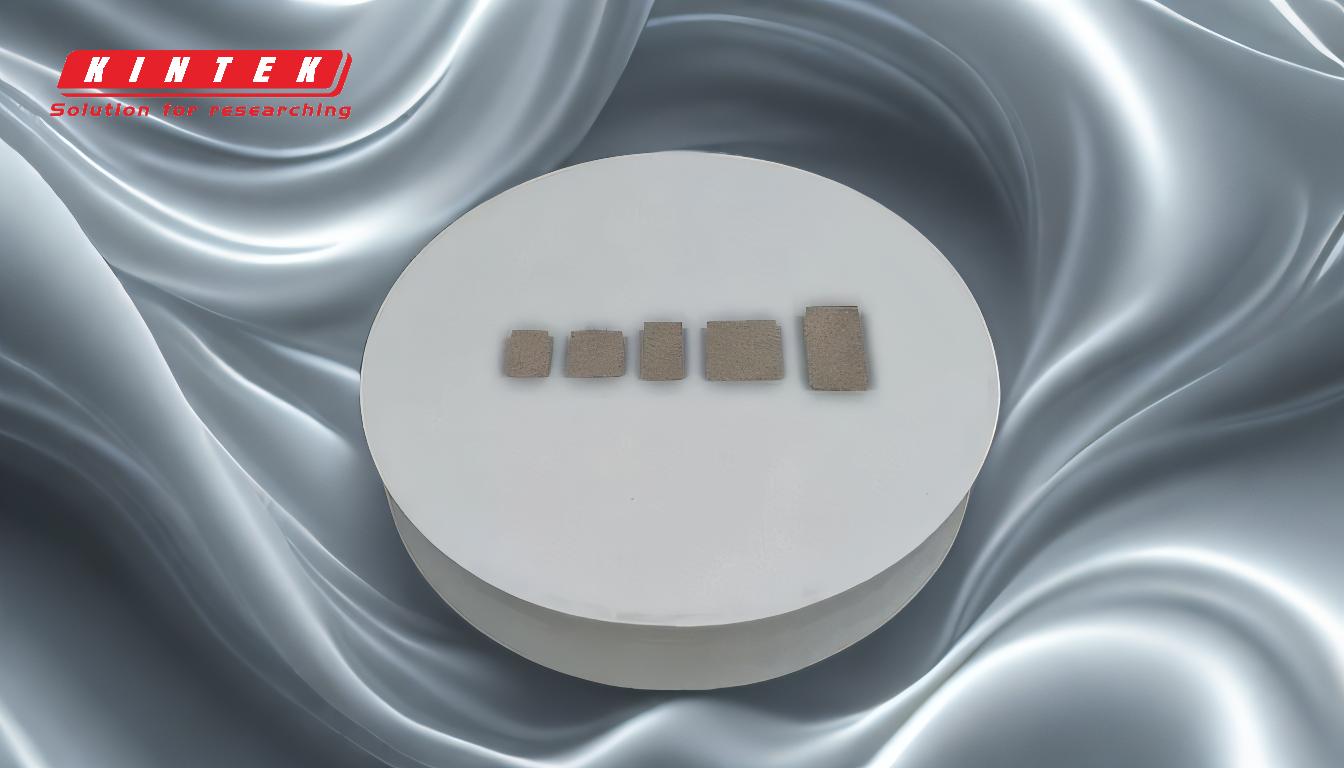
-
Advantages of Sheet Metal:
- Strength and Durability: Sheet metal is known for its high strength-to-weight ratio, making it ideal for applications requiring robust materials. It can withstand significant stress and mechanical loads without deformation.
- Cost-Effectiveness: Due to its availability and ease of production, sheet metal is often more affordable than other materials like plastics or composites. This makes it a preferred choice for large-scale manufacturing.
- Versatility: Sheet metal can be easily cut, bent, and shaped into various forms, allowing for customization in design and application. This flexibility is particularly useful in industries like construction and automotive manufacturing.
- Recyclability: Sheet metal is highly recyclable, contributing to sustainable manufacturing practices. This eco-friendly aspect is increasingly important in modern industries.
-
Disadvantages of Sheet Metal:
- Design Limitations: While sheet metal is versatile, it has limitations in creating highly complex or intricate designs. This can restrict its use in applications requiring advanced geometries.
- Susceptibility to Corrosion: Certain types of sheet metal, such as untreated steel, are prone to rust and corrosion when exposed to moisture or harsh environments. Protective coatings or treatments are often required to mitigate this issue.
- Weight: Although lightweight compared to solid metal blocks, sheet metal can still add significant weight to structures or products, which may be a drawback in applications where weight is a critical factor.
- Cost of Tooling: While the material itself is cost-effective, the tools and machinery required for cutting, bending, and shaping sheet metal can be expensive, especially for small-scale operations.
-
Uses of Sheet Metal:
- Construction: Sheet metal is widely used in roofing, wall cladding, and structural components due to its strength and durability. It is also used in HVAC systems for ductwork and ventilation.
- Automotive Industry: Car bodies, chassis, and engine components often utilize sheet metal for its lightweight and robust properties. It helps improve fuel efficiency while maintaining structural integrity.
- Electronics: Sheet metal is used to fabricate enclosures and cabinets for electronic devices, providing protection and heat dissipation.
- Aerospace: In the aerospace industry, sheet metal is used for aircraft skins, panels, and structural components, where weight and strength are critical factors.
- Consumer Goods: Appliances like refrigerators, washing machines, and ovens often incorporate sheet metal in their construction due to its durability and aesthetic appeal.
-
Material Options in Sheet Metal:
- Steel: Commonly used for its strength and affordability, steel sheet metal is ideal for heavy-duty applications. However, it requires protective coatings to prevent rust.
- Aluminum: Lightweight and corrosion-resistant, aluminum sheet metal is perfect for applications where weight reduction is essential, such as in the aerospace and automotive industries.
- Copper: Known for its electrical conductivity and aesthetic appeal, copper sheet metal is often used in electrical components and decorative applications.
- Stainless Steel: Highly resistant to corrosion and staining, stainless steel sheet metal is used in environments requiring hygiene and durability, such as medical equipment and food processing.
-
Manufacturing Processes:
- Cutting: Techniques like laser cutting, plasma cutting, and shearing are used to shape sheet metal into desired forms.
- Bending: Press brakes and other tools are employed to bend sheet metal into specific angles and shapes.
- Stamping: This process involves pressing sheet metal into molds to create detailed designs or patterns.
- Welding: Sheet metal pieces are often welded together to form larger structures or components.
-
Environmental and Economic Impact:
- Sheet metal’s recyclability reduces waste and promotes sustainable manufacturing practices. Its durability also means fewer replacements, leading to long-term cost savings.
- The material’s widespread availability and ease of production contribute to its economic viability, making it a staple in many industries.
By understanding the advantages, disadvantages, and uses of sheet metal, purchasers and manufacturers can make informed decisions about its application in their projects. Its versatility and cost-effectiveness make it a valuable material, despite some limitations in design and susceptibility to corrosion.
Summary Table:
Aspect | Details |
---|---|
Advantages | Strength, durability, cost-effectiveness, versatility, recyclability |
Disadvantages | Design limitations, susceptibility to corrosion, weight, cost of tooling |
Uses | Construction, automotive, electronics, aerospace, consumer goods |
Material Options | Steel, aluminum, copper, stainless steel |
Manufacturing | Cutting, bending, stamping, welding |
Environmental Impact | Recyclable, promotes sustainability, reduces waste |
Discover how sheet metal can benefit your project—contact us today for expert advice!