Chemical vapor deposition (CVD) is a highly versatile and efficient method for applying coatings to a wide range of materials, offering numerous advantages over other deposition techniques. It is particularly valued for its ability to produce high-purity, uniform, and durable coatings that can withstand extreme conditions, making it ideal for applications in industries such as semiconductors, ceramics, and mining. CVD's ability to coat complex shapes, its cost-effectiveness, and its adaptability to various materials and conditions further enhance its appeal. This method not only extends the life of components subjected to harsh environments but also enables the creation of advanced materials with tailored properties.
Key Points Explained:
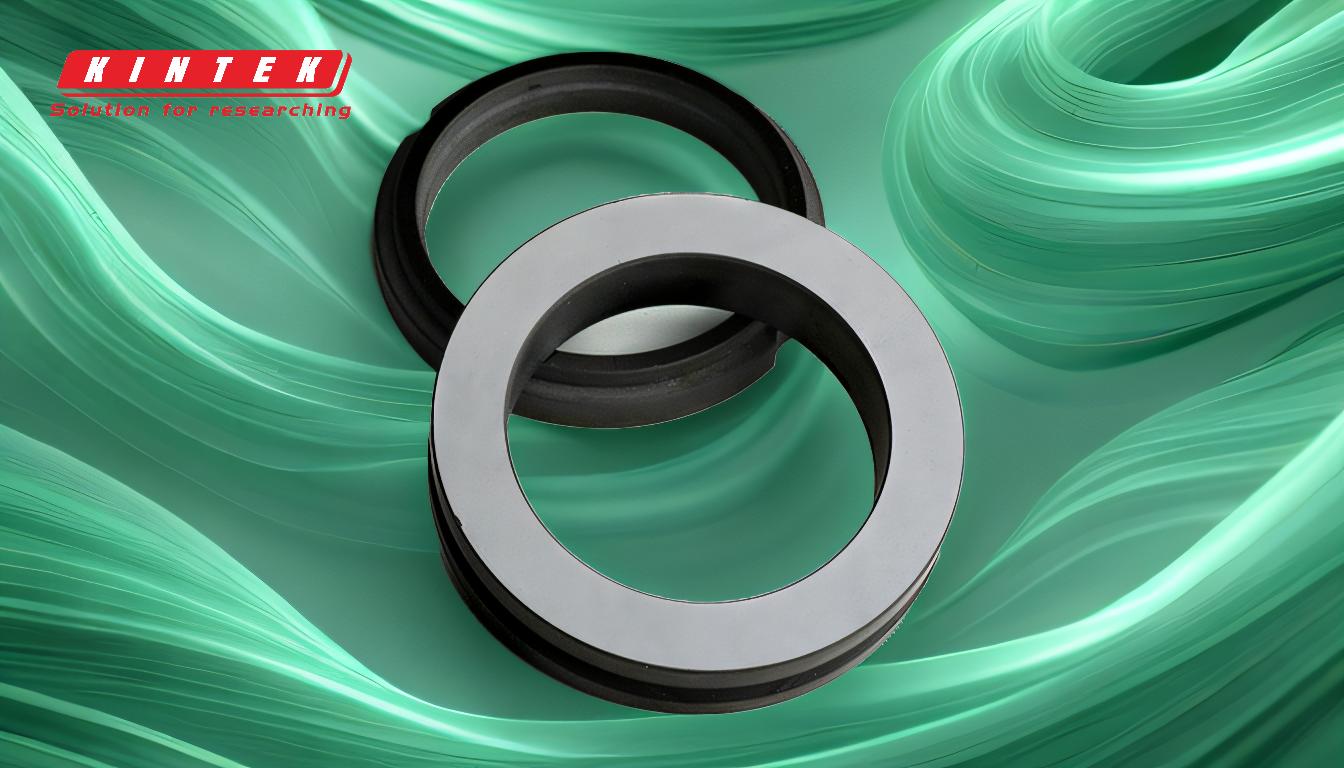
-
High Purity and Uniformity:
- CVD is capable of depositing films with exceptional purity and uniformity. This is crucial for applications where consistency and quality are paramount, such as in the production of semiconductors and high-performance ceramics. The process relies on chemical reactions, which can be precisely controlled to achieve the desired material properties.
-
Versatility in Material Compatibility:
- CVD can be applied to a wide range of materials, including metals, ceramics, and glass. This versatility makes it suitable for diverse industrial applications, from enhancing the durability of mining equipment to improving the performance of electronic components.
-
Ability to Coat Complex Geometries:
- Unlike some other deposition methods, CVD is not limited by a line-of-sight deposition. This allows it to effectively coat complex shapes, deep recesses, and intricate geometries, which is particularly beneficial for components with challenging designs.
-
Economic and Scalable:
- CVD is often more economical than other techniques due to its high deposition rates and the ability to produce thick coatings. Additionally, it can be easily scaled up for mass production, making it a cost-effective solution for large-scale industrial applications.
-
Durable and High-Performance Coatings:
- Coatings produced by CVD are known for their durability and ability to withstand high-stress environments. They can be optimized for specific properties such as corrosion resistance, abrasion resistance, and high purity, ensuring long-lasting performance even under extreme conditions.
-
Precision and Control:
- CVD offers full control over the deposition process, including parameters such as temperature, pressure, and gas flow rate. This precision allows for the creation of ultra-thin layers and the synthesis of both pure and complex materials with tailored properties.
-
Enhanced Surface Properties:
- CVD can enhance the surface properties of substrates in ways that conventional techniques cannot. This includes imparting characteristics such as lubricity, weatherability, and hydrophobicity, which are essential for specific applications.
-
No Need for Ultra-High Vacuum:
- Unlike some other deposition methods, CVD does not typically require an ultra-high vacuum, which simplifies the process and reduces equipment costs.
-
Application in Advanced Technologies:
- CVD is integral to the production of nanocomposite ceramic coatings and other advanced materials, which are critical in industries such as electronics, aerospace, and energy. Its ability to produce high-purity single- or polycrystalline thin films, as well as amorphous films, makes it indispensable in modern manufacturing.
In summary, CVD coating offers a combination of high performance, versatility, and cost-effectiveness, making it a preferred choice for a wide range of industrial applications. Its ability to produce durable, high-quality coatings on complex geometries and diverse materials ensures its continued relevance in advanced manufacturing and technology sectors.
Summary Table:
Advantage | Description |
---|---|
High Purity & Uniformity | Produces consistent, high-quality coatings essential for semiconductors & ceramics. |
Material Compatibility | Works with metals, ceramics, and glass for diverse industrial applications. |
Complex Geometries | Coats intricate shapes and deep recesses effectively. |
Economic & Scalable | Cost-effective with high deposition rates and scalability for mass production. |
Durable Coatings | Resists corrosion, abrasion, and extreme conditions for long-lasting performance. |
Precision & Control | Full control over parameters like temperature, pressure, and gas flow rate. |
Enhanced Surface Properties | Adds lubricity, weatherability, and hydrophobicity for specialized needs. |
No Ultra-High Vacuum | Simplifies the process and reduces equipment costs. |
Advanced Technologies | Critical for nanocomposite ceramic coatings and modern manufacturing. |
Unlock the potential of CVD coating for your applications—contact our experts today!