Diamond cutting tools are highly valued in modern machining due to their exceptional properties, such as high hardness, excellent wear resistance, superior thermal conductivity, low thermal expansion coefficient, and low friction coefficient. These characteristics make diamond tools ideal for precision machining, especially in industries like aerospace, new energy, and electronics. They operate at cooler temperatures, reducing damage to heat-sensitive materials, and offer high efficiency, durability, and precision. Diamond tools are particularly effective for machining difficult-to-cut materials like graphite, high-silicon aluminum alloys, and ceramics, making them indispensable in advanced manufacturing processes.
Key Points Explained:
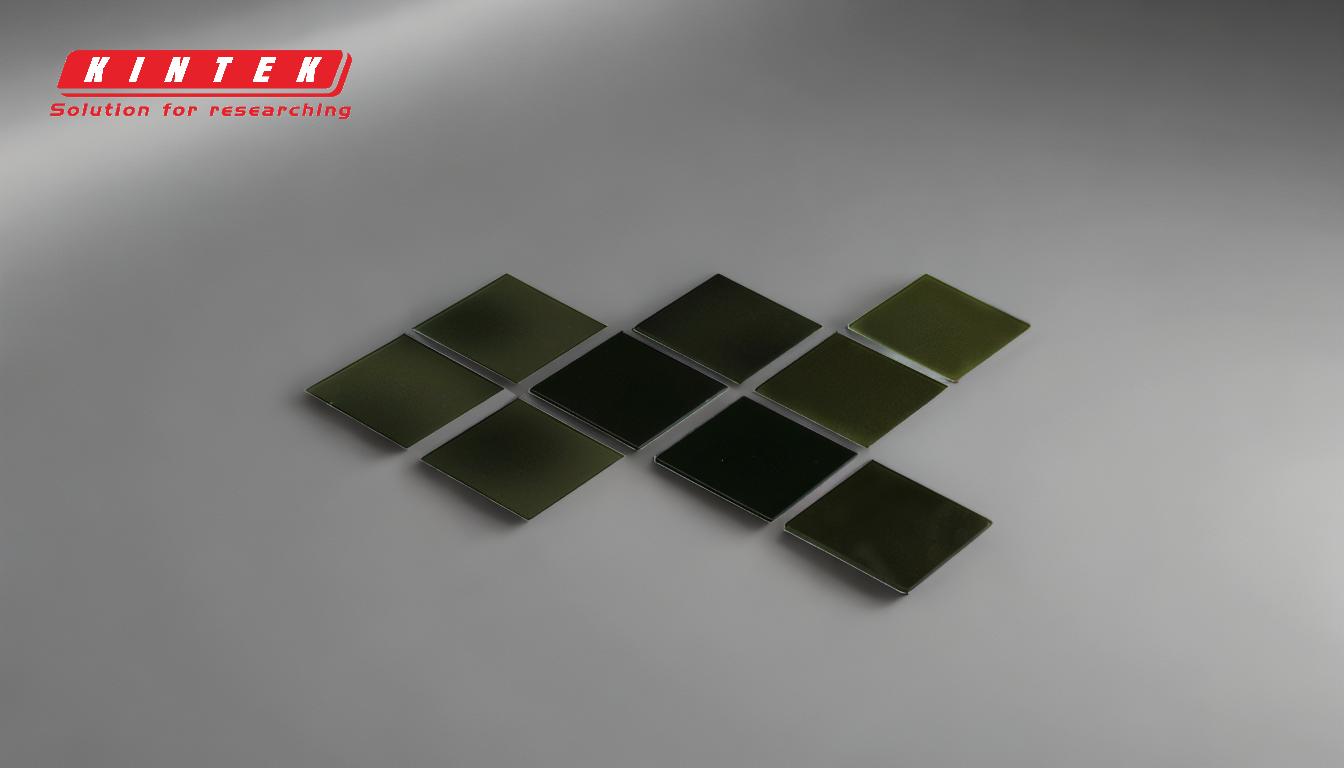
-
High Hardness and Wear Resistance:
- Diamond is the hardest known natural material, which gives diamond cutting tools unparalleled durability and resistance to wear. This hardness allows them to maintain sharp edges for extended periods, reducing the need for frequent tool changes and increasing overall productivity.
- The wear resistance of diamond tools ensures consistent performance over time, which is critical for maintaining precision in high-tolerance machining operations.
-
Superior Thermal Conductivity:
- Diamond has excellent thermal conductivity, which helps dissipate heat generated during cutting processes. This property is particularly beneficial when machining heat-sensitive materials, as it minimizes thermal damage to the workpiece.
- The ability to operate at cooler temperatures extends the lifespan of both the tool and the workpiece, making diamond tools ideal for applications where heat management is crucial.
-
Low Thermal Expansion Coefficient:
- The low thermal expansion coefficient of diamond ensures dimensional stability during machining. This stability is essential for maintaining precision in high-precision applications, such as aerospace components or electronic circuits.
- This property also reduces the risk of tool deformation due to temperature fluctuations, further enhancing machining accuracy.
-
Low Coefficient of Friction:
- Diamond's low friction coefficient reduces the cutting forces required during machining, which in turn minimizes heat generation and tool wear. This results in smoother cutting operations and improved surface finishes on the workpiece.
- The reduced friction also contributes to lower energy consumption and increased tool life, making diamond tools more cost-effective in the long run.
-
Versatility in Applications:
- Diamond cutting tools are widely used in industries such as aerospace, new energy, electronics, and precision machining. They are particularly effective for machining difficult-to-cut materials like graphite, high-silicon aluminum alloys, ceramics, and carbon fibers.
- Their ability to handle a wide range of materials makes them a versatile choice for manufacturers working with advanced or specialized materials.
-
High Efficiency and Precision:
- Diamond tools offer high working efficiency due to their low grinding force, which reduces heat generation and prevents surface burns or cracks on the workpiece. This ensures high-quality finishes and precise machining results.
- The long lifespan and extended dressing periods of diamond tools further enhance productivity by reducing downtime and improving the overall work environment.
-
Chemical Inertness:
- Diamond's high chemical inertness makes it resistant to corrosion and chemical reactions, even in harsh machining environments. This property is particularly valuable when working with reactive materials or in chemically aggressive conditions.
In summary, diamond cutting tools provide a combination of hardness, thermal properties, and chemical stability that make them indispensable in modern machining. Their ability to deliver precision, efficiency, and durability across a wide range of applications ensures their continued relevance in advanced manufacturing industries.
Summary Table:
Property | Advantage |
---|---|
High Hardness | Unmatched durability and wear resistance, reducing frequent tool changes. |
Superior Thermal Conductivity | Efficient heat dissipation, ideal for heat-sensitive materials. |
Low Thermal Expansion | Dimensional stability, ensuring precision in high-tolerance machining. |
Low Friction Coefficient | Smoother cutting, reduced energy consumption, and extended tool life. |
Versatility | Effective for difficult-to-cut materials like graphite, ceramics, and alloys. |
High Efficiency | Low grinding force, preventing surface burns and cracks. |
Chemical Inertness | Resistance to corrosion and chemical reactions in harsh environments. |
Unlock the full potential of diamond cutting tools for your manufacturing needs—contact us today to learn more!