Thermal evaporation is a widely used Physical Vapor Deposition (PVD) technique that offers several advantages, particularly in the production of thin films. This method involves heating a material in a high vacuum until it evaporates, allowing it to deposit onto a substrate. The process is known for its simplicity, cost-effectiveness, and ability to produce high-purity films. Key advantages include precise control over film thickness, compatibility with a wide range of materials, and the ability to achieve uniform coatings. Additionally, thermal evaporation is suitable for applications requiring high-density films and optimal substrate adhesion. The method is particularly advantageous for producing optical coatings, electronic devices, and protective layers.
Key Points Explained:
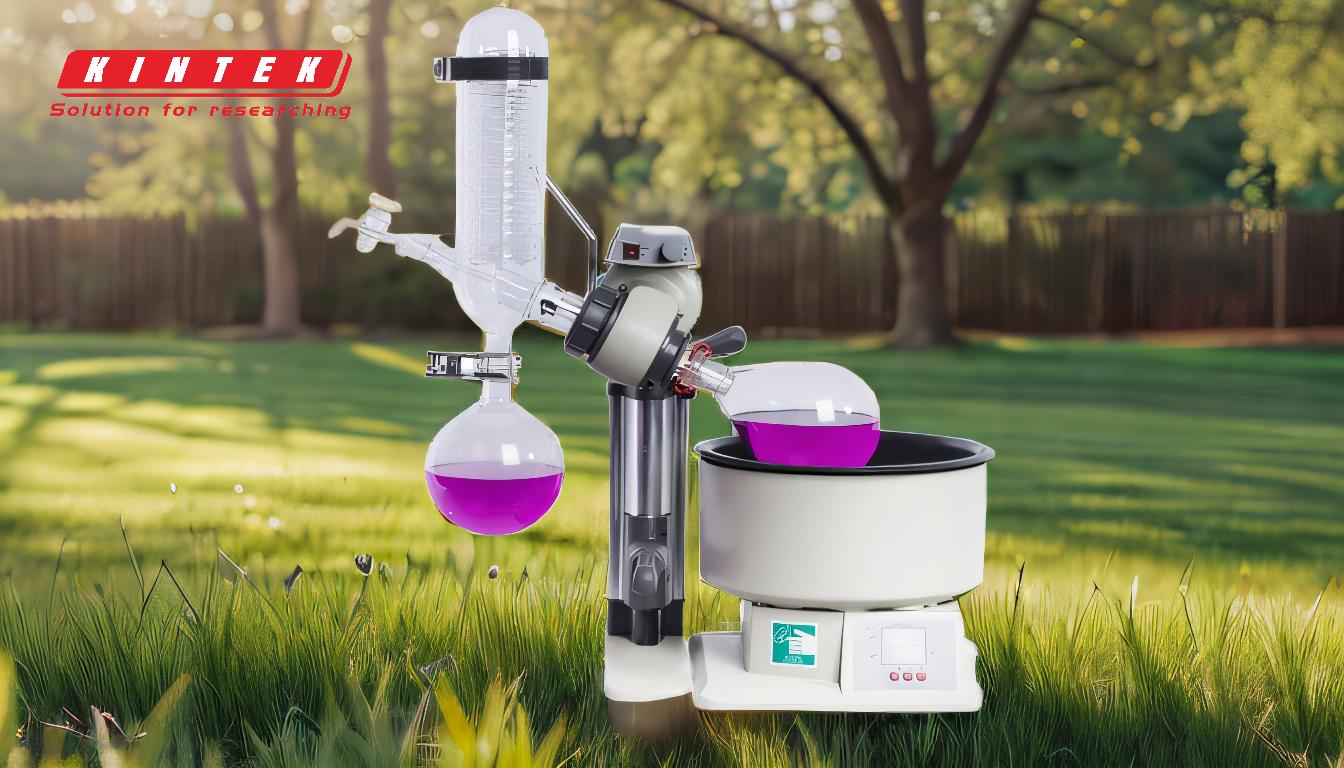
-
High Purity and Uniform Thin Films:
- Thermal evaporation is capable of producing thin films with high purity due to the high vacuum environment, which minimizes contamination. The process allows for precise control over film thickness, ensuring uniformity across the substrate. This is crucial for applications in optics, electronics, and protective coatings where consistency is key.
-
Wide Range of Materials:
- The method is compatible with a broad spectrum of materials, including metals, alloys, and certain compounds. This versatility makes it suitable for various industrial applications, from creating reflective coatings to producing semiconductor devices.
-
Cost-Effectiveness:
- Thermal evaporation is relatively economical compared to other PVD techniques like sputtering or Chemical Vapor Deposition (CVD). The equipment is simpler and less expensive, and the process can be scaled up for mass production without significantly increasing costs.
-
High-Density Films and Optimal Adhesion:
- The process is ideal for achieving high-density thin films, which are essential for applications requiring durability and resistance to wear. The films also exhibit excellent adhesion to the substrate, which is critical for the longevity and performance of the coated product.
-
Control Over Optical Properties:
- Thermal evaporation allows for precise control over the optical properties of the coatings. This is particularly valuable in producing laser optics and architectural glass, where specific wavelength reflections are required. The method can be fine-tuned to achieve desired optical characteristics, enhancing the functionality of the final product.
-
Environmentally Friendly:
- The process is considered environmentally friendly as it does not involve harmful chemicals or produce significant waste. The high vacuum environment ensures that the deposition material is used efficiently, minimizing material loss and environmental impact.
-
Compatibility with Complex Geometries:
- While thermal evaporation is generally used for flat or simple geometries, it can be adapted for more complex shapes with the use of appropriate fixtures and techniques. This flexibility makes it a versatile choice for various industrial applications.
-
Use of Evaporation Sources:
- The efficiency and effectiveness of thermal evaporation largely depend on the type of evaporation sources used. These sources, whether they are resistive heaters or electron beam evaporators, play a crucial role in determining the quality and characteristics of the deposited films. Proper selection and maintenance of these sources are essential for achieving optimal results.
In summary, thermal evaporation offers a combination of simplicity, cost-effectiveness, and high performance, making it a preferred method for many thin-film deposition applications. Its ability to produce high-purity, uniform films with excellent adhesion and optical properties ensures its continued relevance in advanced manufacturing processes.
Summary Table:
Advantage | Description |
---|---|
High Purity and Uniform Films | Produces contamination-free, uniform thin films with precise thickness control. |
Wide Range of Materials | Compatible with metals, alloys, and compounds for diverse applications. |
Cost-Effectiveness | Economical compared to other PVD techniques, with scalable production. |
High-Density Films and Adhesion | Ensures durable, wear-resistant films with excellent substrate adhesion. |
Control Over Optical Properties | Fine-tuned for specific optical characteristics in coatings. |
Environmentally Friendly | Minimal waste and no harmful chemicals, reducing environmental impact. |
Compatibility with Complex Shapes | Adaptable for complex geometries with proper fixtures and techniques. |
Efficient Evaporation Sources | Optimal results depend on the selection and maintenance of evaporation sources. |
Unlock the potential of thermal evaporation for your projects—contact our experts today!