Thin film deposition, particularly through techniques like Physical Vapor Deposition (PVD) and sputtering, offers numerous advantages that make it a preferred method in various industries. These benefits include enhanced film adhesion, precise control over film properties, improved durability, and the ability to deposit a wide range of materials. Thin film deposition is widely used in applications such as machining tools, advanced thin-film devices, and coatings for improved performance and longevity. The process is also environmentally friendly, making it a sustainable choice for modern manufacturing.
Key Points Explained:
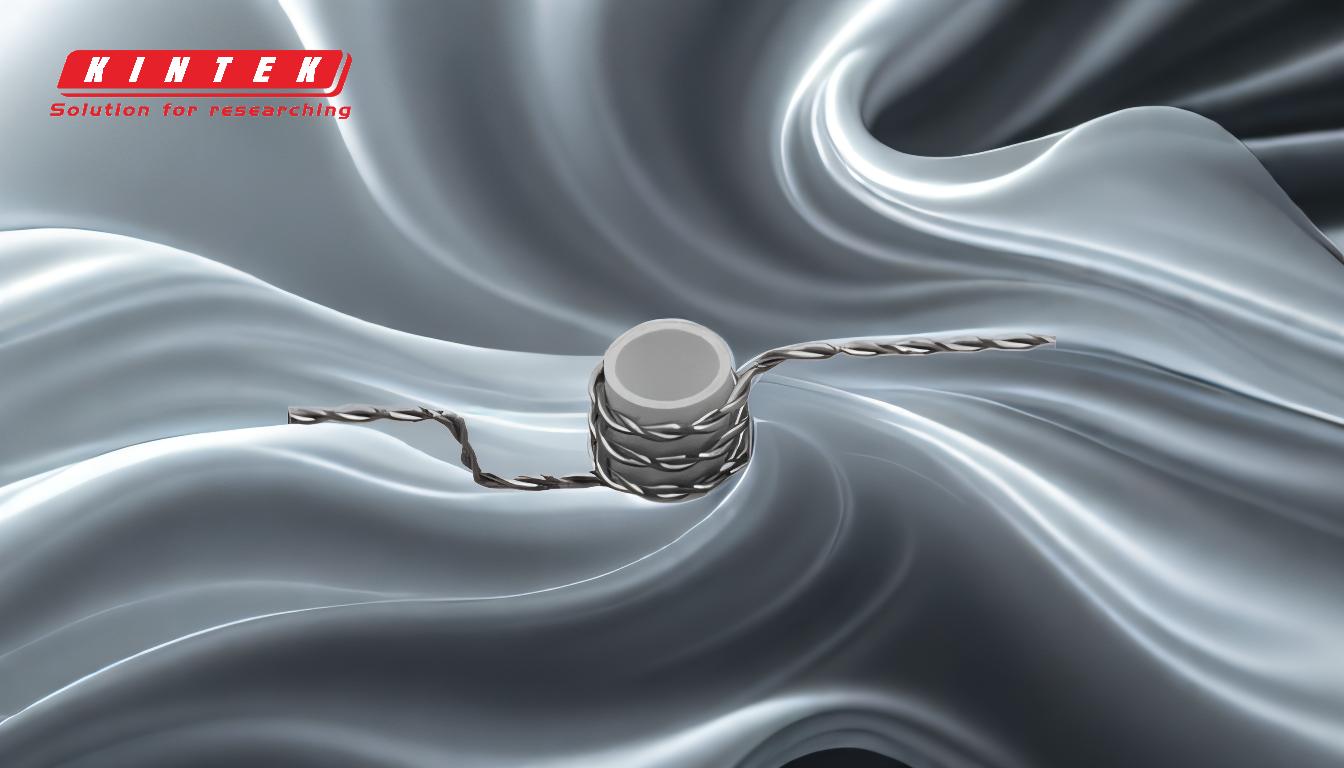
-
Enhanced Film Adhesion and Uniformity:
- Thin film deposition techniques, especially sputtering, provide excellent film adhesion strength. This ensures that the deposited films remain firmly attached to the substrate, even under harsh conditions.
- The process allows for highly precise and uniform thin films, which are critical for applications requiring consistent performance, such as in semiconductors and optical devices.
-
Improved Durability and Performance:
- Thin film deposition significantly enhances the durability of components and tools. For example, machining tools treated with thin film coatings exhibit increased lifespan and better thermal properties.
- The coatings provide resistance to oxidation, wear, erosion, and corrosion, making them ideal for use in demanding environments.
-
Versatility in Material Deposition:
- PVD and other thin film deposition techniques allow for the deposition of a wide range of materials, including metals, ceramics, and compounds. This versatility enables the creation of tailored coatings with specific properties for various applications.
- Compounds used in thin film deposition can be deposited at relatively low temperatures, which is beneficial for substrates that are sensitive to high temperatures.
-
Environmental and Economic Benefits:
- PVD is considered an environmentally friendly process due to its minimal waste generation and the absence of harmful by-products.
- The ability to perform concurrent double-sided coating with appropriate mechanical configurations enhances production efficiency, reducing both time and costs.
-
High-Temperature Tolerance and Ablation Resistance:
- Thin film coatings produced through PVD are extremely hard and resistant to high temperatures, making them suitable for applications in aerospace and other high-stress industries.
- These coatings also exhibit superior ablation resistance, which is crucial for components exposed to extreme conditions.
-
Applications in Advanced Technologies:
- Thin film deposition is integral to the fabrication of advanced thin-film devices, such as solar panels, microelectronics, and sensors. The precise control over film properties ensures optimal performance in these high-tech applications.
- The technique is also used in the production of corrosion-resistant and wear-resistant coatings, which are essential for extending the life of industrial components.
In summary, thin film deposition offers a multitude of advantages, including improved adhesion, durability, versatility, and environmental benefits. These properties make it an indispensable technique in modern manufacturing and advanced technology applications.
Summary Table:
Advantage | Description |
---|---|
Enhanced Film Adhesion | Ensures strong bonding to substrates, even under harsh conditions. |
Improved Durability | Increases lifespan and resistance to wear, corrosion, and oxidation. |
Versatility in Materials | Deposits metals, ceramics, and compounds for tailored coatings. |
Environmental Benefits | Minimal waste and no harmful by-products, making it eco-friendly. |
High-Temperature Resistance | Ideal for aerospace and high-stress applications due to heat resistance. |
Advanced Technology Applications | Used in solar panels, microelectronics, and sensors for optimal performance. |
Unlock the potential of thin film deposition for your projects—contact our experts today!