The chemical vapor deposition (CVD) approach is a highly advantageous method for producing carbon nanotubes (CNTs) due to its versatility, controllability, and cost-effectiveness. It allows for the synthesis of high-purity materials with tailored properties by adjusting parameters such as temperature, pressure, and gas flow rates. CVD is particularly effective for creating ultra-thin layers and complex structures, making it ideal for applications like electrical circuits. Additionally, it is environmentally friendly compared to other methods, as it minimizes material and energy consumption while reducing greenhouse gas emissions. Overall, CVD stands out as a leading technique for CNT production due to its precision, scalability, and adaptability.
Key Points Explained:
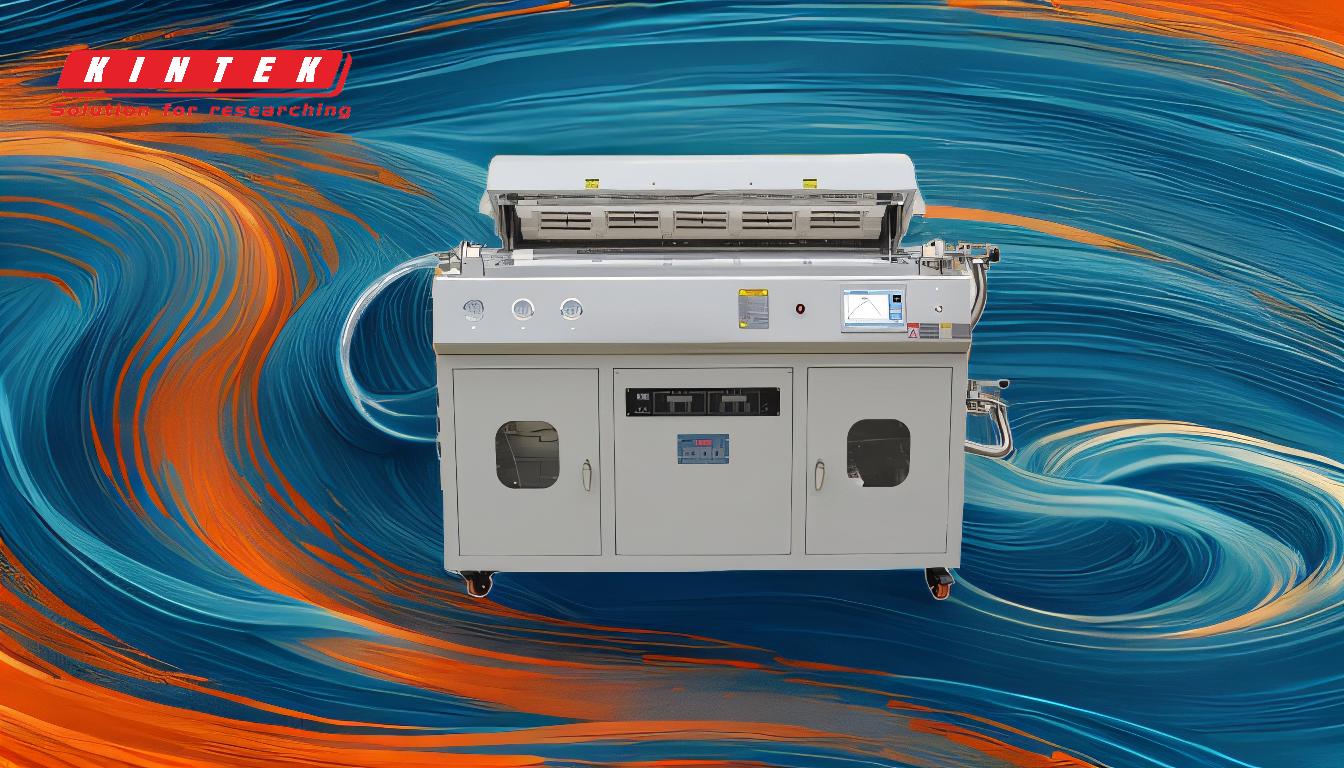
-
High Versatility and Control:
- CVD relies on chemical reactions, which can be precisely controlled by adjusting parameters such as temperature, pressure, gas flow rate, and gas concentration. This allows for the synthesis of a wide range of materials, including single- or polycrystalline thin films, amorphous films, and complex materials with desired purity levels.
- The ability to create ultra-thin layers of material makes CVD ideal for applications like electrical circuits, where precision is critical.
-
Structural Controllability:
- Catalytic chemical vapor deposition (CCVD), a subset of CVD, is the mainstream method for CNT production due to its ability to control the structure of the nanotubes. This ensures consistent quality and performance in the final product.
- The process allows for the adjustment of the chemical and physical properties of the films, enabling the production of CNTs with specific characteristics tailored to their intended use.
-
Cost-Effectiveness:
- CVD is often more economical than other deposition methods, such as physical vapor deposition (PVD), due to its high deposition rates and ability to produce thick coatings without requiring ultra-high vacuum conditions.
- The process minimizes material consumption and energy usage, making it a cost-effective solution for large-scale production.
-
Environmental Friendliness:
- CVD is designed to limit environmental impact by reducing greenhouse gas emissions and energy consumption during the synthesis process. This makes it a more sustainable option compared to other methods.
- The ability to optimize gases for specific properties, such as corrosion resistance or high purity, further enhances its eco-friendly profile.
-
Ability to Coat Complex Surfaces:
- Unlike PVD, CVD is not limited by line-of-sight deposition, meaning it can coat holes, deep recesses, and other complex shapes with high throwing power. This makes it suitable for precision and complex surfaces.
- The process also exhibits good wrap-around properties, ensuring uniform coating even on intricate geometries.
-
High-Quality Material Production:
- CVD produces materials with greater purity, hardness, and resistance to agitation or damage compared to other coating methods. This results in durable coatings that can withstand high-stress environments and extreme temperatures.
- The method is capable of depositing a wide range of materials, including graphene, which is essential for advanced technological applications.
-
Simplicity and Ease of Operation:
- CVD equipment is relatively simple and easy to operate and maintain, making it accessible for various industrial applications.
- The process is scalable, allowing for both small-scale laboratory experiments and large-scale industrial production.
In summary, the chemical vapor deposition approach offers a combination of precision, versatility, cost-effectiveness, and environmental sustainability, making it a preferred method for CNT production. Its ability to produce high-quality materials with tailored properties and its suitability for complex surfaces further solidify its position as a leading technique in modern material science.
Summary Table:
Advantage | Description |
---|---|
High Versatility and Control | Precise control over temperature, pressure, and gas flow for tailored material properties. |
Structural Controllability | Produces consistent quality CNTs with adjustable chemical and physical properties. |
Cost-Effectiveness | Economical for large-scale production with minimal material and energy consumption. |
Environmental Friendliness | Reduces greenhouse gas emissions and energy usage for sustainable production. |
Complex Surface Coating | Coats intricate geometries and deep recesses with uniform thickness. |
High-Quality Material | Produces durable, high-purity materials resistant to extreme conditions. |
Simplicity and Scalability | Easy to operate and maintain, suitable for both lab and industrial applications. |
Ready to leverage the benefits of CVD for your CNT production? Contact our experts today to learn more!