The sieving method is a versatile and widely used technique for particle size analysis and material separation across various industries. It involves the use of laboratory sieves, sieve shakers, and air jet sieving machines to analyze and classify materials based on their particle size. This method is essential for quality control, research, and production processes in industries such as agriculture, construction, food, pharmaceuticals, metallurgy, and more. The applications of sieving include particle size distribution analysis, sample preparation, and fractioning, ensuring the consistency and quality of materials in both granular and powdery forms. Its importance spans from scientific research to industrial production, making it a critical tool in material analysis.
Key Points Explained:
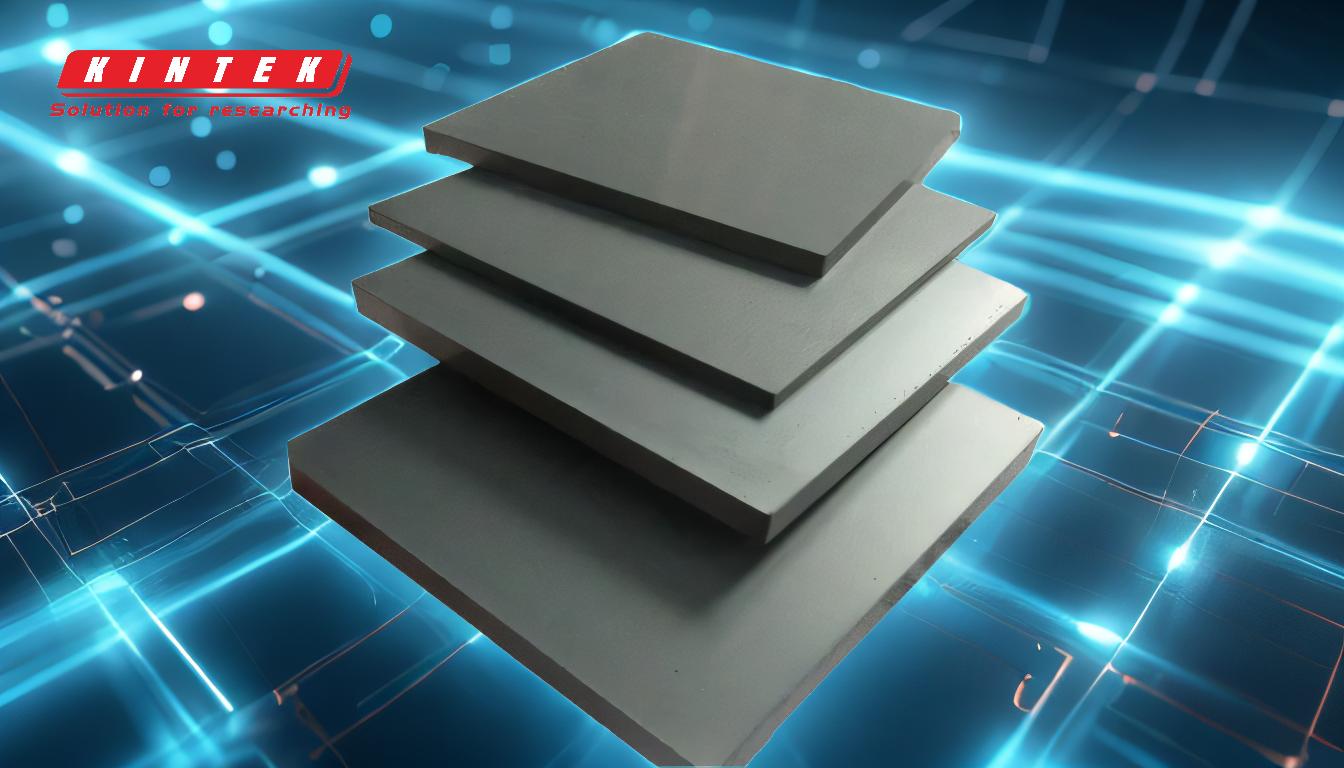
-
Particle Size Distribution Analysis:
- Sieving is primarily used to determine the particle size distribution of materials. This is crucial in industries like pharmaceuticals, where the size of particles can affect the efficacy and safety of drugs.
- In the food industry, particle size analysis ensures consistency in texture and quality of products like flour, sugar, and spices.
- In construction, sieving helps in analyzing aggregates used in concrete and asphalt, ensuring the right mix for durability and strength.
-
Sample Preparation:
- Sieving is used to prepare samples for further analysis. For example, in geology, sieving helps separate soil or rock samples into different size fractions for detailed study.
- In metallurgy, sieving is used to prepare metal powders for additive manufacturing or other processes, ensuring uniformity in particle size.
-
Fractioning:
- Sieving allows for the separation of materials into different size fractions. This is particularly useful in industries like agriculture, where seeds or grains need to be sorted by size for planting or processing.
- In the chemical industry, sieving helps in separating different components of a mixture based on particle size, which is essential for quality control and product consistency.
-
Quality Control and Inspection:
- Sieving is a critical tool in quality control processes. In the automotive and aerospace industries, sieving ensures that materials like metal powders or coatings meet stringent quality standards, reducing the risk of internal failures.
- In the pharmaceutical industry, sieving is used to ensure that active pharmaceutical ingredients (APIs) and excipients are of the correct particle size, which is vital for drug performance and safety.
-
Applications Across Industries:
- Agriculture: Sieving is used for seed sorting, soil analysis, and grain processing.
- Construction: Sieving helps in analyzing aggregates for concrete and asphalt, ensuring the right mix for building and paving roads.
- Food Industry: Sieving ensures the consistency and quality of powdered and granular food products.
- Pharmaceuticals: Sieving is used for particle size analysis of drugs and excipients, ensuring safety and efficacy.
- Metallurgy: Sieving is used for analyzing metal powders and ensuring uniformity in manufacturing processes.
- Geology: Sieving helps in soil and rock analysis for environmental and exploration purposes.
- Environmental Technology: Sieving is used in waste management and recycling processes to separate materials by size.
-
Types of Sieving Equipment:
- Laboratory Sieves: Used for manual or mechanical sieving in labs for precise particle size analysis.
- Sieve Shakers: Automated machines that shake sieves to ensure efficient and consistent particle separation. They are widely used in industries like medicine, metallurgy, and chemicals.
- Air Jet Sieving Machines: Used for fine particle analysis, especially in industries that process powdered products. These machines use air flow to separate particles, making them ideal for materials that are difficult to sieve mechanically.
-
Scientific Research and Development:
- Sieving is a fundamental tool in research labs for studying the properties of materials. It is used in fields like ceramics, abrasives, and pigments to understand how particle size affects material behavior.
- In national defense and aerospace, sieving is used to analyze materials used in advanced technologies, ensuring they meet strict performance criteria.
-
Production Control:
- In manufacturing, sieving is used to monitor and control the quality of raw materials and finished products. This is especially important in industries like abrasives, where particle size directly impacts product performance.
- In the building materials industry, sieving ensures that materials like cement and sand meet the required specifications for construction projects.
In conclusion, the sieving method is an indispensable technique across a wide range of industries. Its applications in particle size analysis, sample preparation, and quality control make it a critical tool for ensuring the consistency, safety, and performance of materials in both research and industrial settings.
Summary Table:
Key Application | Industry | Purpose |
---|---|---|
Particle Size Distribution | Pharmaceuticals | Ensures drug efficacy and safety through uniform particle size. |
Sample Preparation | Geology, Metallurgy | Separates soil, rock, or metal powders for detailed analysis. |
Fractioning | Agriculture, Chemical | Sorts seeds, grains, or mixtures by size for processing or quality control. |
Quality Control | Aerospace, Automotive | Verifies material quality to reduce failure risks. |
Scientific Research | Ceramics, Abrasives | Studies material properties and behavior based on particle size. |
Production Control | Construction, Food | Ensures raw materials meet specifications for consistent product quality. |
Need precise particle size analysis for your industry? Contact us today to find the right sieving solution!