Thermal evaporation is a versatile thin-film deposition technique with applications spanning multiple industries. It is widely used for depositing metals like silver and aluminum, as well as for co-depositing multiple materials. Key applications include electrical contacts, optics (lens coatings, anti-reflective layers), electronics (OLEDs, solar cells, thin-film transistors), consumer packaging (aluminum films), and decorative purposes (cosmetic closures, jewelry). Additionally, it plays a role in EMI/RFI shielding, light reflectors, and specialized applications like NASA spacesuits and firefighter uniforms. Its ability to create precise, uniform, and high-quality thin films makes it indispensable in sectors ranging from aerospace to consumer goods.
Key Points Explained:
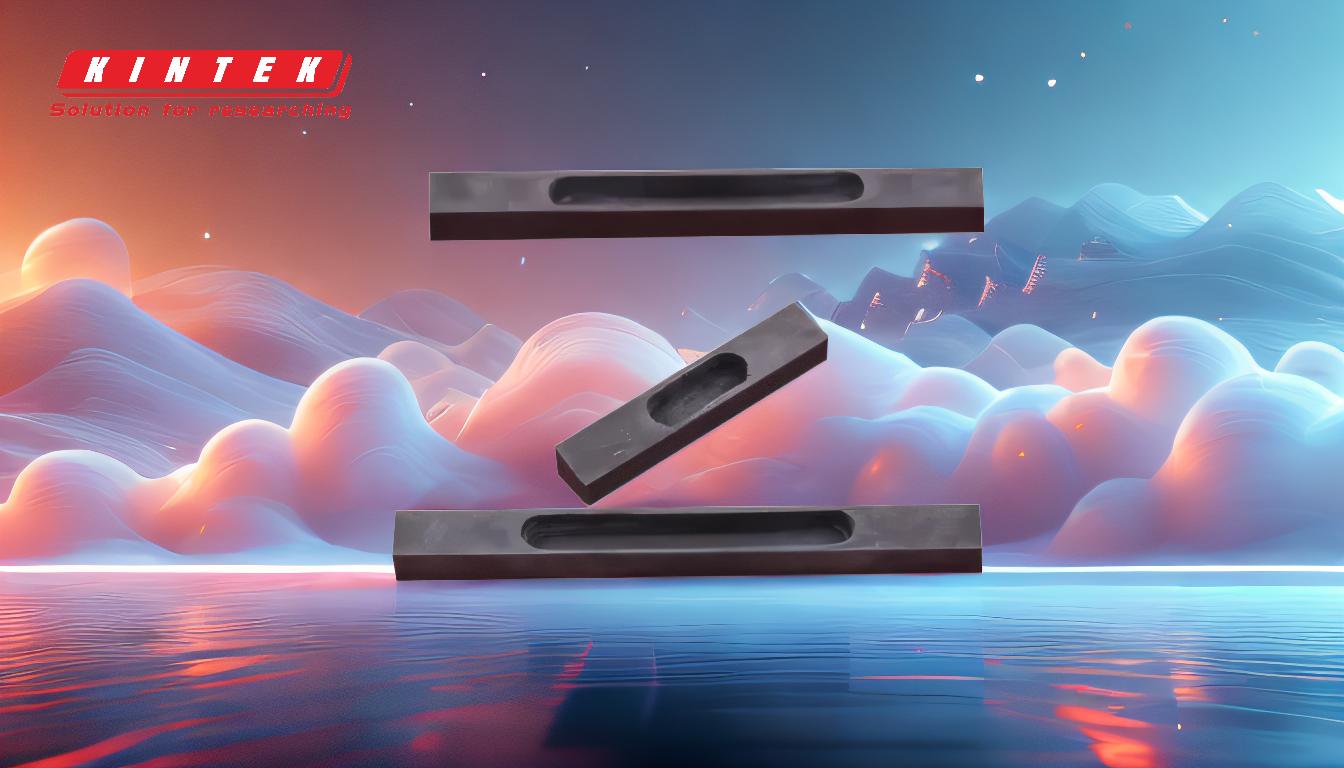
-
Electrical Contacts and Metal Deposition
- Thermal evaporation is commonly used to deposit single metals like silver and aluminum, which are essential for creating electrical contacts in various devices.
- The process involves heating the metal in a crucible until it evaporates and then condenses onto a substrate, forming a thin, uniform layer.
- This application is critical in electronics, where reliable electrical connections are necessary for components like transistors and semiconductors.
-
Optics and Anti-Reflective Coatings
- In the optics industry, thermal evaporation is used to deposit thin films on lenses to create anti-reflective coatings, UV protection layers, and other optical enhancements.
- These coatings improve light transmission, reduce glare, and enhance the durability of optical components.
- The precision of thermal evaporation ensures that the films are uniform and adhere well to the substrate, making it ideal for high-performance optical applications.
-
Electronics: OLEDs, Solar Cells, and Thin-Film Transistors
- Thermal evaporation is a key process in the production of organic light-emitting diodes (OLEDs), where it deposits thin layers of organic materials and metals.
- In solar cells, it is used to create metal bonding layers and other functional coatings that improve efficiency and durability.
- Thin-film transistors (TFTs) also rely on thermal evaporation for depositing conductive and semiconductive layers, which are essential for display technologies and integrated circuits.
-
Consumer Packaging and Decorative Applications
- Thermal evaporation is used to deposit thin aluminum films on plastic packaging, providing a barrier against moisture, oxygen, and light.
- This application is widely used in food packaging to extend shelf life and maintain product quality.
- In decorative applications, thermal evaporation is used to apply aesthetic coatings on cosmetic closures, sporting goods, and jewelry, enhancing their visual appeal.
-
EMI/RFI Shielding and Light Reflectors
- Thermal evaporation is employed to create electromagnetic interference (EMI) and radio-frequency interference (RFI) shielding in electronic devices.
- These coatings protect sensitive components from external interference, ensuring reliable performance.
- Light reflectors, used in automotive, medical, and aerospace industries, also benefit from the high reflectivity and durability of films deposited via thermal evaporation.
-
Specialized Applications: Aerospace, Medical, and Safety Equipment
- Thermal evaporation is used in advanced applications like NASA spacesuits, firefighter uniforms, and emergency blankets, where thin films provide thermal insulation, reflectivity, and protection.
- In aerospace, it is used for anti-static coatings and soundproof enclosures, enhancing the safety and performance of aircraft.
- These specialized applications highlight the adaptability of thermal evaporation in meeting stringent performance and safety requirements.
-
Co-Deposition of Multiple Materials
- Thermal evaporation can be used for co-depositing multiple materials by controlling the temperature of individual crucibles.
- This capability is essential for creating complex multi-layer structures in devices like OLEDs and solar cells, where different materials are required to achieve specific electrical and optical properties.
- The precision and control offered by thermal evaporation make it a preferred method for advanced thin-film applications.
Thermal evaporation's ability to produce high-quality, uniform thin films with precise control over thickness and composition makes it a critical technology across diverse industries. From consumer goods to cutting-edge aerospace applications, its versatility and reliability ensure its continued importance in modern manufacturing and technology.
Summary Table:
Application | Key Use Cases |
---|---|
Electrical Contacts | Depositing metals like silver and aluminum for reliable connections in electronics. |
Optics | Anti-reflective coatings, UV protection, and optical enhancements for lenses. |
Electronics | OLEDs, solar cells, and thin-film transistors for advanced devices. |
Consumer Packaging | Aluminum films for moisture and oxygen barriers in food packaging. |
Decorative Applications | Aesthetic coatings for jewelry, cosmetic closures, and sporting goods. |
EMI/RFI Shielding | Protective coatings for electronic devices to prevent interference. |
Specialized Applications | NASA spacesuits, firefighter uniforms, and aerospace coatings. |
Co-Deposition | Multi-layer structures for OLEDs and solar cells with precise material control. |
Discover how thermal evaporation can transform your industry—contact us today for expert solutions!