Plasma-Enhanced Chemical Vapor Deposition (PECVD) is a versatile thin-film deposition technique widely used in industries such as semiconductor manufacturing, solar cell production, and surface coating. Unlike traditional Chemical Vapor Deposition (CVD), which relies solely on thermal energy, PECVD utilizes plasma to enhance chemical reactions at lower temperatures, typically between 100-400°C. This method involves introducing process gases into a low-pressure chamber, where a high-frequency electrical discharge generates a plasma. The plasma dissociates the gases into reactive species, which then deposit as a solid film on a substrate. PECVD is particularly advantageous for depositing high-quality thin films on temperature-sensitive materials, offering precise control over film properties such as thickness, composition, and uniformity.
Key Points Explained:
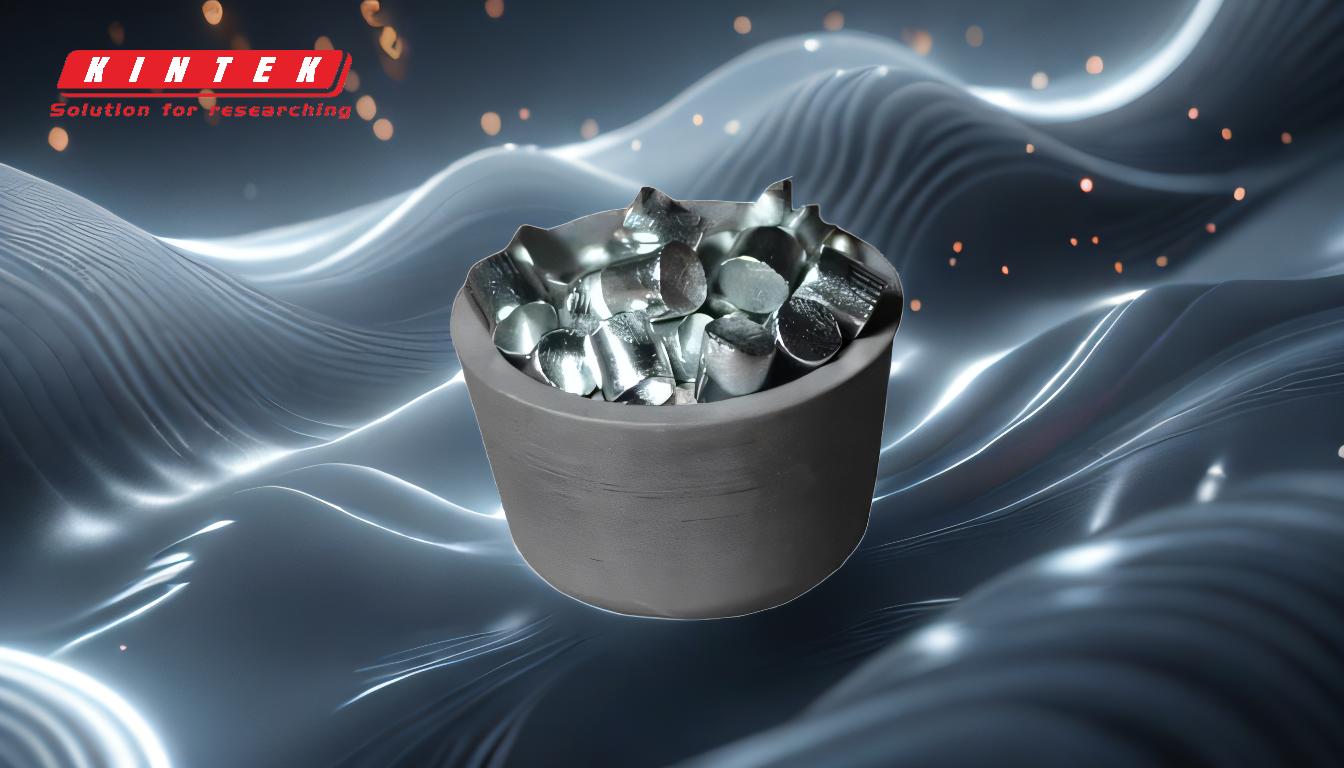
-
Definition and Purpose of PECVD:
- PECVD stands for Plasma-Enhanced Chemical Vapor Deposition, a thin-film deposition technique that combines plasma energy with chemical reactions to deposit materials on substrates.
- It is used to create high-quality thin films for applications in semiconductors, solar cells, and protective coatings.
-
Working Principle:
- Plasma Generation: A high-frequency electrical discharge (RF, DC, or pulsed DC) is applied to create a plasma in a low-pressure environment. This plasma consists of ionized species that provide the energy needed to dissociate stable precursor gases.
- Chemical Reactions: The plasma breaks down the precursor gases into reactive species, which then undergo chemical reactions to form a solid film on the substrate.
- Substrate Heating: The substrate is typically heated to a predetermined temperature (100-400°C) to facilitate film growth, although the plasma itself can also provide some heating.
-
Advantages Over Traditional CVD:
- Lower Temperature Operation: PECVD allows for deposition at much lower temperatures compared to traditional CVD, making it suitable for temperature-sensitive materials.
- Enhanced Reaction Rates: The plasma provides additional energy to dissociate gases, enabling faster and more efficient deposition.
- Versatility: PECVD can deposit a wide range of materials, including silicon-based films, carbon-based films, and metal oxides.
-
Process Steps:
- Chamber Preparation: The substrate is placed in a vacuum chamber, and the chamber is evacuated to create a low-pressure environment.
- Gas Introduction: Process gases (precursors) are introduced into the chamber.
- Plasma Ignition: A high-frequency electrical discharge is applied to generate plasma, which dissociates the gases into reactive species.
- Film Deposition: The reactive species deposit onto the substrate, forming a solid film.
- Post-Processing: The substrate may undergo additional treatments, such as annealing, to improve film properties.
-
Applications:
- Semiconductor Manufacturing: PECVD is used to deposit dielectric layers, passivation layers, and other thin films in semiconductor devices.
- Solar Cells: It is employed to create anti-reflective coatings and passivation layers in photovoltaic cells.
- Protective Coatings: PECVD is used to deposit hard, wear-resistant coatings on various materials.
-
Key Parameters:
- Pressure: Typically operates at low pressures (millitorr to torr range) to maintain plasma stability.
- Power: The power of the electrical discharge affects the energy of the plasma and the rate of film deposition.
- Gas Flow Rates: Precise control of gas flow rates is essential to achieve the desired film composition and properties.
- Substrate Temperature: The temperature of the substrate influences the film's microstructure and adhesion.
-
Comparison with Other Deposition Techniques:
- PECVD vs. Thermal CVD: PECVD operates at lower temperatures and provides faster deposition rates due to the plasma's energy.
- PECVD vs. PVD (Physical Vapor Deposition): PECVD involves chemical reactions, whereas PVD relies on physical processes like sputtering or evaporation. PECVD generally offers better step coverage and conformal coatings.
-
Challenges and Considerations:
- Film Uniformity: Achieving uniform film thickness across large substrates can be challenging.
- Plasma-Induced Damage: High-energy plasma species can potentially damage sensitive substrates.
- Process Control: Precise control of process parameters (pressure, power, gas flow) is critical to ensure consistent film quality.
In summary, PECVD is a powerful and versatile thin-film deposition technique that leverages plasma energy to enable low-temperature, high-quality film growth. Its ability to deposit a wide range of materials with precise control over film properties makes it indispensable in modern manufacturing processes, particularly in the semiconductor and solar industries.
Summary Table:
Aspect | Details |
---|---|
Definition | PECVD combines plasma energy with chemical reactions for thin-film deposition. |
Temperature Range | 100-400°C, ideal for temperature-sensitive materials. |
Key Advantages | Lower temperature operation, faster deposition, and material versatility. |
Applications | Semiconductors, solar cells, protective coatings. |
Process Steps | Chamber prep, gas introduction, plasma ignition, film deposition. |
Key Parameters | Pressure, power, gas flow rates, substrate temperature. |
Comparison with CVD | Lower temperature, faster rates, better for sensitive materials. |
Challenges | Film uniformity, plasma-induced damage, precise process control. |
Ready to explore PECVD solutions for your industry? Contact our experts today to learn more!