Atomic Layer Deposition (ALD) is a highly advanced thin-film deposition technique that offers numerous benefits, particularly in applications requiring precision, uniformity, and conformality. ALD enables the creation of ultra-thin, highly uniform films on complex geometries, curved surfaces, and even nanoparticles. Its self-limiting and self-assembled nature ensures precise control over film thickness, stoichiometry, and quality. ALD operates at relatively low temperatures, making it suitable for temperature-sensitive materials. Additionally, it eliminates the need for line-of-sight deposition, allowing for versatile applications in industries such as semiconductors, medical devices, and energy storage. Despite its complexity and higher facility costs, ALD's advantages in precision, conformality, and material versatility make it a superior choice for advanced thin-film applications.
Key Points Explained:
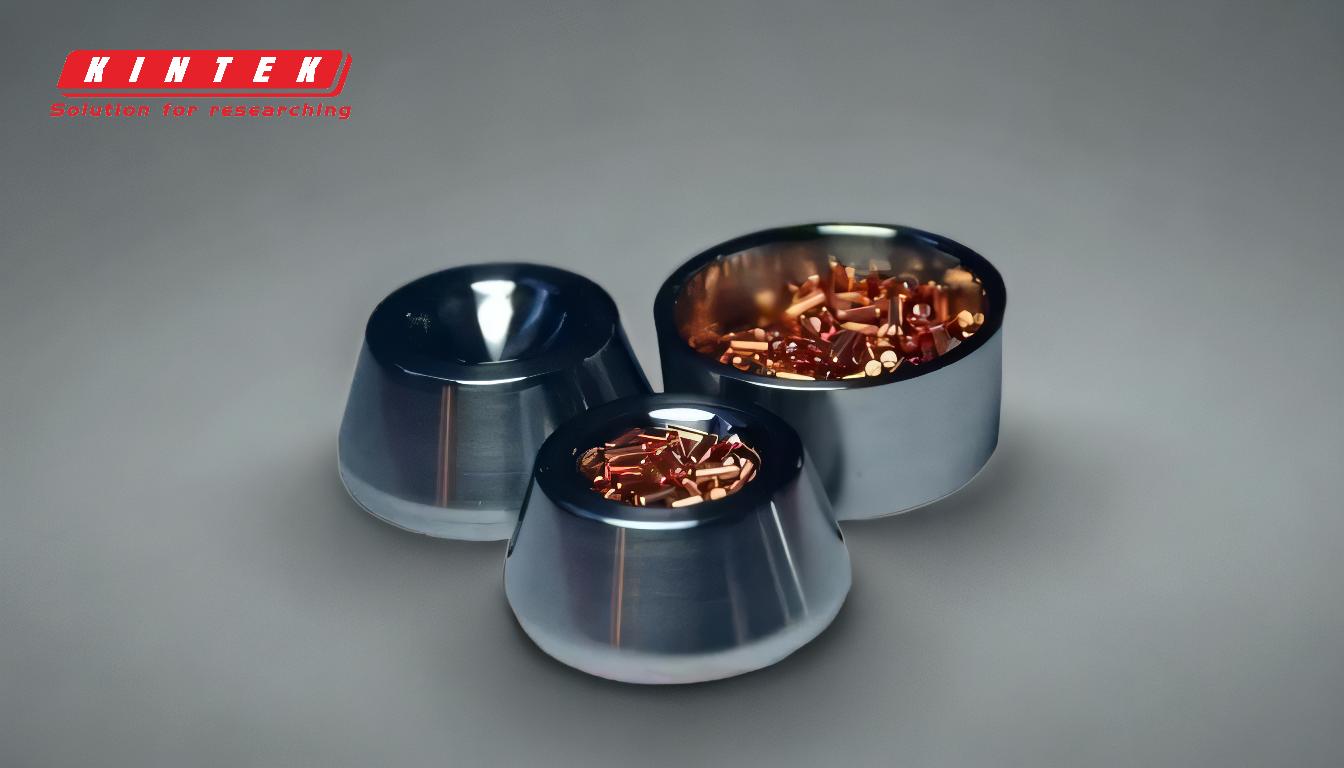
-
Highly Uniform and Conformal Films:
- ALD excels in producing uniform and conformal thin films, even on complex geometries, curved surfaces, and nanoparticles.
- This is due to its layer-by-layer deposition mechanism, which ensures even coverage regardless of surface topography.
- Applications include coating intricate medical devices, semiconductor components, and nanoparticles for catalysis or energy storage.
-
Precise Thickness Control:
- ALD allows for atomic-level precision in controlling film thickness by adjusting the number of deposition cycles.
- This precision is critical in applications like semiconductor manufacturing, where even nanometer-scale variations can impact performance.
-
Low-Temperature Processing:
- ALD operates at relatively low temperatures compared to other deposition methods, making it suitable for temperature-sensitive materials.
- This is particularly advantageous for organic materials, polymers, and certain biomedical applications.
-
Stoichiometric Control:
- ALD provides excellent control over the chemical composition of the deposited films, ensuring stoichiometric accuracy.
- This is essential for applications requiring specific material properties, such as in advanced electronics or energy storage materials.
-
Self-Limiting and Self-Assembled Mechanism:
- The self-limiting nature of ALD ensures that each deposition cycle stops once the surface is fully covered, preventing over-deposition.
- This results in inherently high-quality films with minimal defects and excellent reproducibility.
-
Versatility in Material Deposition:
- ALD can deposit a wide range of materials, including oxides, nitrides, metals, and organic compounds.
- This versatility makes it suitable for diverse applications, from protective coatings to functional layers in electronic devices.
-
Improved Electrochemical Performance:
- In energy storage applications, ALD is used to modify cathode materials by forming thin, homogeneous films that prevent unwanted reactions between electrodes and electrolytes.
- This enhances ionic conductivity and overall electrochemical performance.
-
No Line-of-Sight Requirement:
- Unlike traditional deposition methods like physical or chemical vapor deposition, ALD does not require line-of-sight exposure.
- This allows for uniform coating of complex 3D structures, such as trenches, pores, and high-aspect-ratio features.
-
Reduction of Surface Reaction Rates:
- ALD coatings can effectively reduce surface reaction rates, which is beneficial in applications like corrosion protection or stabilizing reactive materials.
-
Challenges and Considerations:
- Despite its advantages, ALD involves complex chemical reactions, high facility costs, and requires expertise to operate.
- The process also necessitates the removal of excess precursors, adding complexity to the coating process.
In summary, ALD's unique capabilities in producing highly uniform, conformal, and precisely controlled thin films make it an invaluable tool in advanced manufacturing and research. While it requires specialized equipment and expertise, its benefits in precision, versatility, and performance enhancement justify its use in cutting-edge applications.
Summary Table:
Key Feature | Description |
---|---|
Uniform & Conformal Films | Ensures even coverage on complex geometries, curved surfaces, and nanoparticles. |
Precise Thickness Control | Atomic-level precision by adjusting deposition cycles. |
Low-Temperature Processing | Suitable for temperature-sensitive materials like polymers and biomaterials. |
Stoichiometric Control | Ensures accurate chemical composition for advanced applications. |
Self-Limiting Mechanism | Prevents over-deposition, ensuring high-quality, defect-free films. |
Material Versatility | Deposits oxides, nitrides, metals, and organic compounds. |
No Line-of-Sight Requirement | Uniform coating of complex 3D structures like trenches and pores. |
Applications | Semiconductors, medical devices, energy storage, and corrosion protection. |
Unlock the potential of ALD for your advanced applications—contact our experts today!