CVD (Chemical Vapor Deposition) coating offers numerous benefits, particularly in enhancing the durability and performance of materials in challenging environments. By altering surface properties, CVD coatings combat corrosion, oxidation, and wear, extending the lifespan of components in industries like aerospace, mining, and semiconductors. This method is highly effective for depositing refractory materials, improving wear resistance, and enabling scalable production of advanced materials like carbon nanotubes and 2D materials. Despite its higher temperature requirements and potential for harmful gas emissions, CVD remains a preferred choice for applications demanding high-performance coatings, such as turbine blades and nanocomposite ceramic coatings.
Key Points Explained:
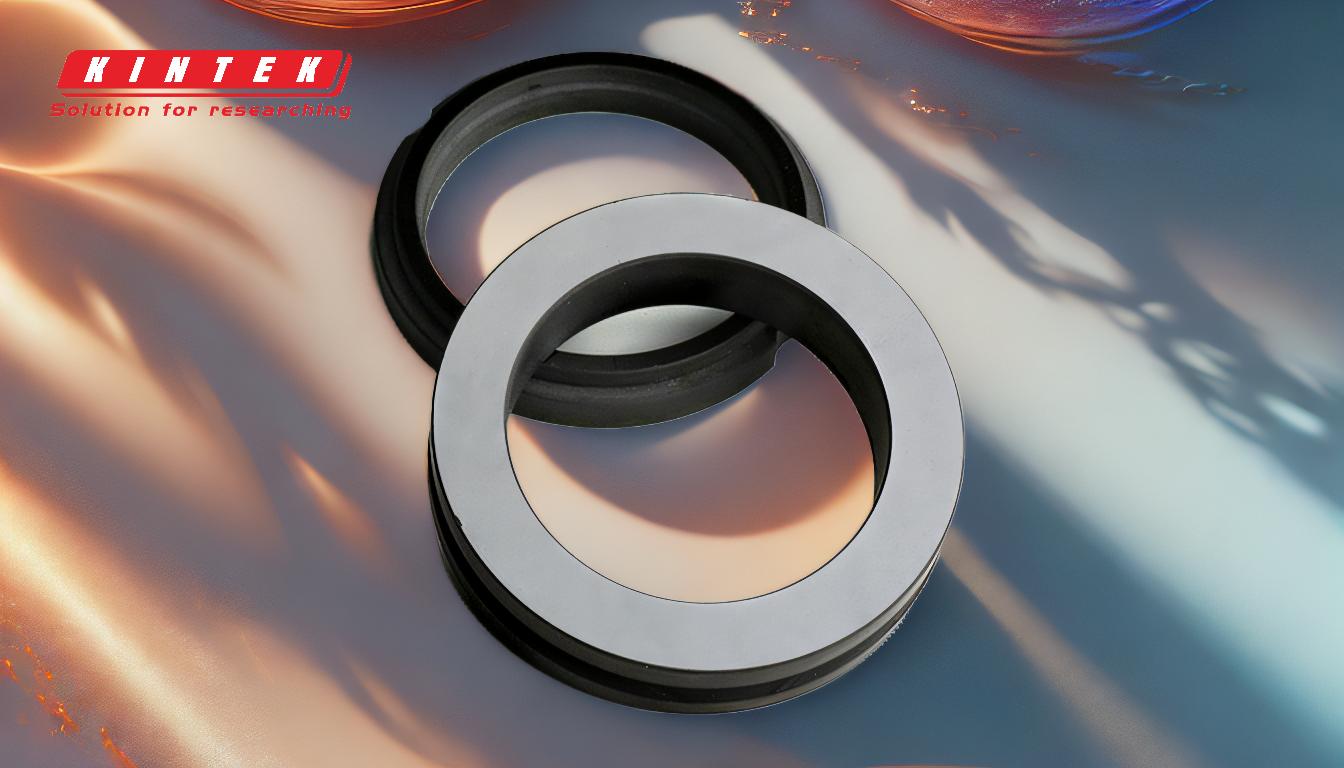
-
Enhanced Durability in Harsh Environments:
- CVD coatings are specifically designed to combat severe attrition caused by corrosion, oxidation, and wear. This makes them ideal for industrial applications where components are exposed to aggressive operating conditions.
- By altering the surface properties of metals or non-metals, CVD coatings significantly extend the lifespan of materials, reducing the need for frequent replacements and maintenance.
-
Improved Wear and Thermal Resistance:
- CVD is widely used to deposit refractory materials on critical components like turbine blades. These coatings enhance wear resistance and thermal shock resistance, ensuring reliable performance under extreme temperatures and mechanical stress.
- This capability is particularly valuable in industries such as aerospace and energy, where components must withstand high temperatures and mechanical wear.
-
Scalable Production of Advanced Materials:
- CVD is recognized as the most successful method for preparing 2D materials due to its ability to produce high-quality, uniform coatings at a low cost and on a large scale.
- The technology is also used in the production of carbon nanotubes (CNTs) and layered thin films, which are essential for applications in nanotechnology, electronics, and advanced materials science.
-
Versatility Across Industries:
- CVD technology is employed in a wide range of industries, including semiconductors, ceramics, and mining. Its ability to produce nanocomposite ceramic coatings makes it a critical component in these fields.
- For example, in the semiconductor industry, CVD is used to deposit thin films that are essential for the fabrication of microelectronic devices.
-
Comparison with PVD:
- While CVD offers significant benefits, it is important to note that PVD (Physical Vapor Deposition) is often preferred in certain industrial applications. PVD operates at lower temperatures, which can be advantageous for coating cutting tools and other temperature-sensitive components.
- CVD, on the other hand, requires higher temperatures and uses volatile chemicals, which can produce harmful gases. However, CVD remains the preferred choice for applications requiring high-performance coatings, such as turbine blades and nanocomposite ceramic coatings.
-
Critical Role in Nanocomposite Ceramic Coatings:
- CVD is particularly important for producing nanocomposite ceramic coatings, which are essential in industries like mining and ceramics. These coatings provide exceptional hardness, wear resistance, and thermal stability, making them ideal for use in harsh environments.
- The ability of CVD to deposit uniform and high-quality coatings ensures the reliability and longevity of components in these demanding applications.
In summary, CVD coating offers a range of benefits, including enhanced durability, improved wear and thermal resistance, and the ability to produce advanced materials at scale. While it has some limitations compared to PVD, its advantages make it a critical technology in industries requiring high-performance coatings.
Summary Table:
Benefit | Description |
---|---|
Enhanced Durability | Combats corrosion, oxidation, and wear, extending material lifespan. |
Improved Wear and Thermal Resistance | Deposits refractory materials for high-performance applications like turbine blades. |
Scalable Production of Advanced Materials | Produces 2D materials, carbon nanotubes, and layered thin films at scale. |
Versatility Across Industries | Used in aerospace, mining, semiconductors, and ceramics for nanocomposite coatings. |
Critical Role in Nanocomposite Ceramic Coatings | Provides exceptional hardness, wear resistance, and thermal stability. |
Unlock the potential of CVD coatings for your industry—contact us today to learn more!