Biomass catalysts play a critical role in enhancing the efficiency and selectivity of biomass conversion processes, such as pyrolysis, gasification, and hydrogen production. These catalysts are chosen based on the type of biomass, desired end products, and specific process conditions. Common catalysts include biochar-based materials, zeolites, clay minerals, and metal-based compounds like nickel-dolomite or titanium nitrides. They improve yields of valuable products like hydrogen, bio-oil, and hydrocarbons while reducing impurities. For example, 10 wt% Ni-dolomite is optimal for hydrogen production from rice husk, while zeolites and clay minerals are effective for hydrocarbon production. The choice of catalyst is tailored to maximize the yield and quality of the desired products.
Key Points Explained:
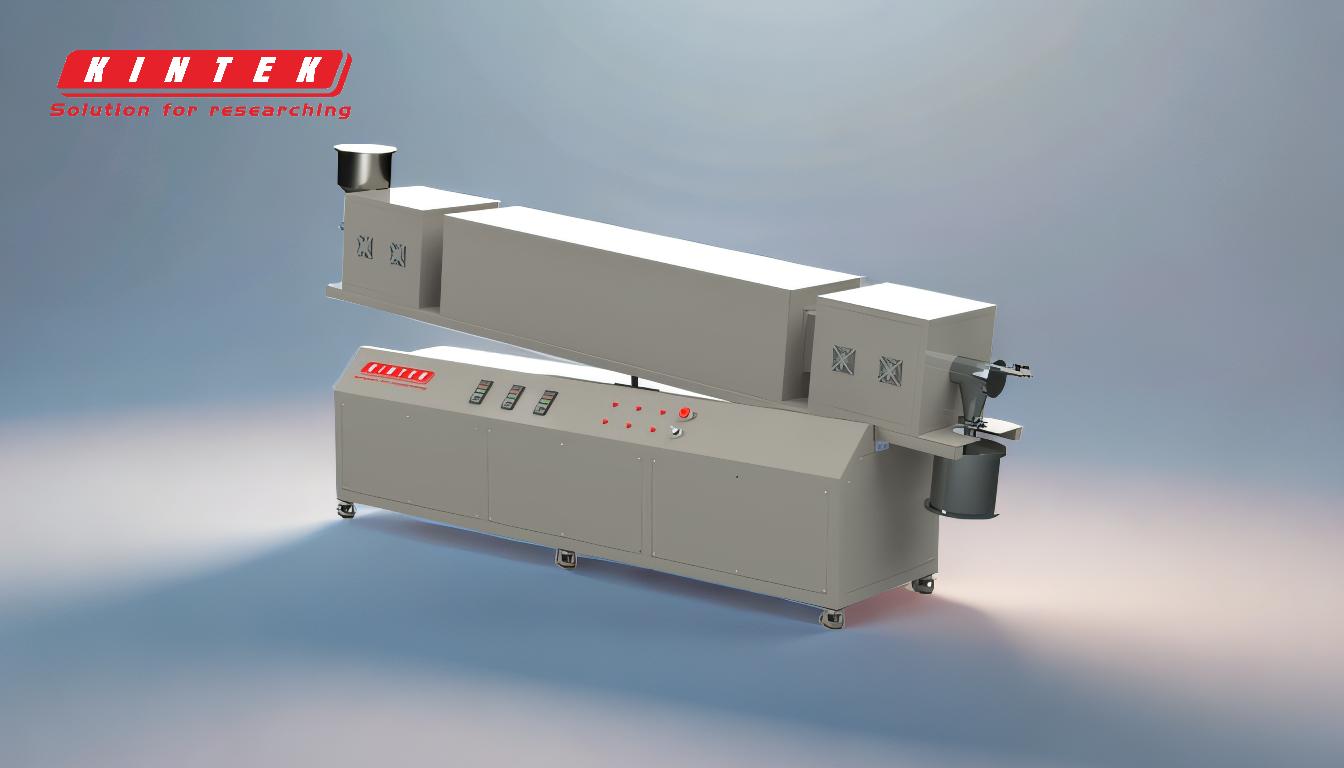
-
Role of Catalysts in Biomass Conversion
- Catalysts are essential for promoting desirable chemical reactions during biomass conversion processes, such as pyrolysis, gasification, and hydrogen production.
- They improve the yield of valuable products like hydrogen, bio-oil, and hydrocarbons (C1, C2, and C3) while reducing impurities such as oxygenates and acids.
- The effectiveness of a catalyst depends on factors like biomass type, desired end products, and process conditions.
-
Types of Catalysts for Biomass Conversion
- Biochar-Based Catalysts: Enhance pyrolysis reactions, improving the yield of biofuels and chemicals.
- Zeolites and Clay Minerals: Porous materials like zeolites (aluminum and silicon oxides) and kaolin selectively crack heavy hydrocarbons and condense light hydrocarbons, making them suitable for producing C1, C2, and C3 hydrocarbons.
-
Metal-Based Catalysts:
- Nickel-Dolomite (10 wt% Ni-dolomite): Found to be optimal for hydrogen production from biomass, particularly rice husk.
- Titanium Nitrides (TiN) and Gallium Nitrides (GaN): Used in fast pyrolysis for furfural production, promoting the formation of furfural compounds.
-
Catalyst Selection Criteria
- Biomass Type: Different catalysts are suited for different biomass feedstocks. For example, rice husk works well with nickel-dolomite for hydrogen production.
- Desired End Products: Catalysts are chosen based on the target products, such as hydrogen, hydrocarbons, or furfural.
- Process Conditions: Factors like temperature, pressure, and reaction time influence the choice of catalyst.
-
Examples of Catalyst Applications
- Hydrogen Production: 10 wt% Ni-dolomite is the most effective catalyst for hydrogen production from rice husk.
- Hydrocarbon Production: Zeolites and clay minerals are used to produce C1, C2, and C3 hydrocarbons from biomass.
- Furfural Production: Titanium nitrides (TiN) and gallium nitrides (GaN) are effective in fast pyrolysis for furfural production.
-
Benefits of Using Catalysts
- Increased Yield: Catalysts significantly improve the yield of valuable products like hydrogen, bio-oil, and hydrocarbons.
- Improved Product Quality: They reduce impurities, such as oxygenates and acids, enhancing the quality of bio-oil and other products.
- Selectivity: Catalysts enable selective reactions, ensuring that the desired products are formed efficiently.
-
Future Considerations
- Research is ongoing to develop more efficient and cost-effective catalysts for biomass conversion.
- Tailoring catalysts to specific biomass types and process conditions will further optimize yields and product quality.
- Sustainable and environmentally friendly catalysts are being explored to reduce the environmental impact of biomass conversion processes.
In summary, catalysts are indispensable in biomass conversion, enabling the production of high-value products like hydrogen, hydrocarbons, and furfural. The choice of catalyst is critical and depends on the biomass type, desired products, and process conditions. Advances in catalyst development will continue to enhance the efficiency and sustainability of biomass conversion technologies.
Summary Table:
Key Aspect | Details |
---|---|
Role of Catalysts | Improve yield of hydrogen, bio-oil, and hydrocarbons; reduce impurities. |
Common Catalyst Types | Biochar-based, zeolites, clay minerals, nickel-dolomite, titanium nitrides. |
Catalyst Selection | Based on biomass type, desired products, and process conditions. |
Applications | Hydrogen production, hydrocarbon production, furfural production. |
Benefits | Increased yield, improved product quality, and enhanced selectivity. |
Future Trends | Development of sustainable, cost-effective, and tailored catalysts. |
Optimize your biomass conversion process with the right catalysts—contact our experts today!