Catalytic pyrolysis is a process that uses catalysts to enhance the breakdown of biomass or plastic into valuable products such as biofuels, chemicals, and hydrocarbons. The choice of catalyst depends on the feedstock and desired end products, with common catalysts including biochar-based materials, titanium compounds, metal nitrides (e.g., TiN, GaN), zeolites, and clay minerals like kaolin. These catalysts improve reaction efficiency, promote selective cracking of heavy hydrocarbons, and enhance deoxygenation, leading to higher yields of targeted compounds like furfural, C1-C3 hydrocarbons, and drop-in fuels. The basicity of the catalyst also plays a critical role in its effectiveness, with higher basicity correlating with stronger deoxygenation capacity.
Key Points Explained:
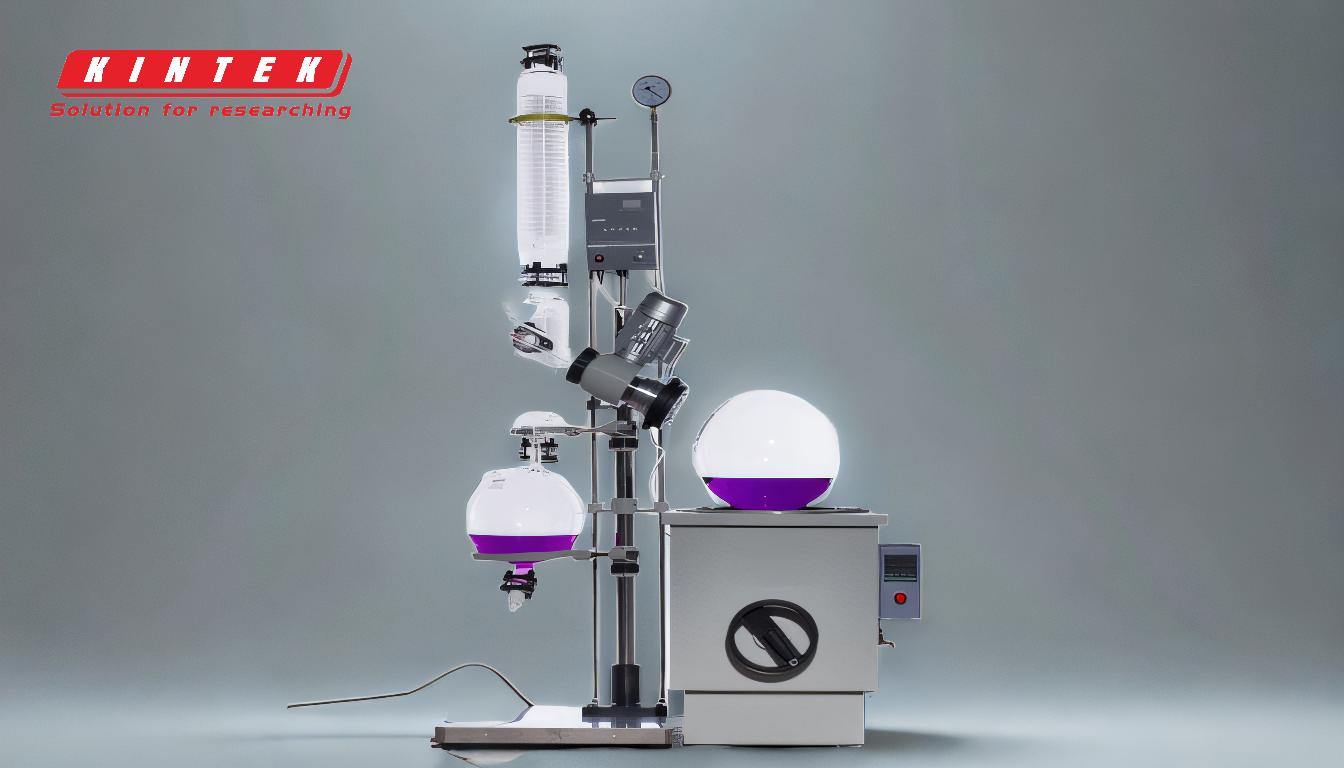
-
Role of Catalysts in Pyrolysis
- Catalysts are used to promote specific chemical reactions during pyrolysis, improving the yield and quality of desired products.
- They facilitate the breakdown of complex molecules in biomass or plastic into simpler, more valuable compounds like biofuels, chemicals, and hydrocarbons.
-
Types of Catalysts
- Biochar-based catalysts: Enhance the production of biofuels and chemicals by promoting desirable reactions.
- Titanium compounds and metal nitrides (e.g., TiN, GaN): Specifically used in biomass fast pyrolysis for furfural production.
- Zeolites: Porous materials composed of aluminum and silicon oxides, used to produce C1, C2, and C3 hydrocarbons from biomass.
- Clay minerals (e.g., kaolin): Assist in selective cracking of heavy hydrocarbons and condensation of light hydrocarbons.
-
Catalyst Basicity and Efficiency
- The basicity of a catalyst is a key factor in its efficiency.
- Higher basicity correlates with stronger deoxygenation capacity, which is crucial for producing high-quality biofuels and chemicals.
-
Applications in Biomass Pyrolysis
- Catalysts like TiN and GaN are particularly effective in promoting the production of furfural compounds from biomass.
- Zeolites and clay minerals are used to selectively crack and condense hydrocarbons, depending on the type of biomass and desired end products.
-
Applications in Plastic Pyrolysis
- Catalysts are used to convert plastic into oil during pyrolysis.
- The addition of a catalyst improves the quality of the product, making it easier to upgrade to drop-in fuels that contain only molecules found in current hydrocarbon fuels.
-
Selective Cracking and Condensation
- Catalysts enable selective cracking of heavy hydrocarbons and condensation of light hydrocarbons, which is essential for tailoring the pyrolysis process to specific feedstocks and desired outcomes.
-
Impact on Product Quality
- Catalysts not only increase the yield of target products but also enhance their quality, making them more suitable for use as drop-in fuels or chemical feedstocks.
By understanding the role and types of catalysts in catalytic pyrolysis, purchasers can make informed decisions about selecting the right catalysts for their specific feedstock and desired end products. This ensures optimal efficiency, yield, and product quality in the pyrolysis process.
Summary Table:
Key Aspect | Details |
---|---|
Role of Catalysts | Promote specific reactions, improve yield, and enhance product quality. |
Types of Catalysts | Biochar-based, titanium compounds, metal nitrides, zeolites, clay minerals. |
Catalyst Basicity | Higher basicity improves deoxygenation capacity and product quality. |
Applications in Biomass | Production of furfural, C1-C3 hydrocarbons, and selective cracking. |
Applications in Plastic | Conversion of plastic into oil and drop-in fuels. |
Impact on Product Quality | Enhances yield and quality of biofuels and chemical feedstocks. |
Discover how the right catalysts can optimize your pyrolysis process—contact our experts today!