Plastic pyrolysis is a process that converts plastic waste into valuable products like fuel, gas, and char. The efficiency and output of this process are heavily influenced by the choice of catalysts, which play a critical role in enhancing reaction rates, improving product quality, and reducing energy requirements. Catalysts can significantly alter the composition of pyrolysis products, making them more suitable for specific applications. Below, we explore the key catalysts used in plastic pyrolysis, their roles, and how they impact the process.
Key Points Explained:
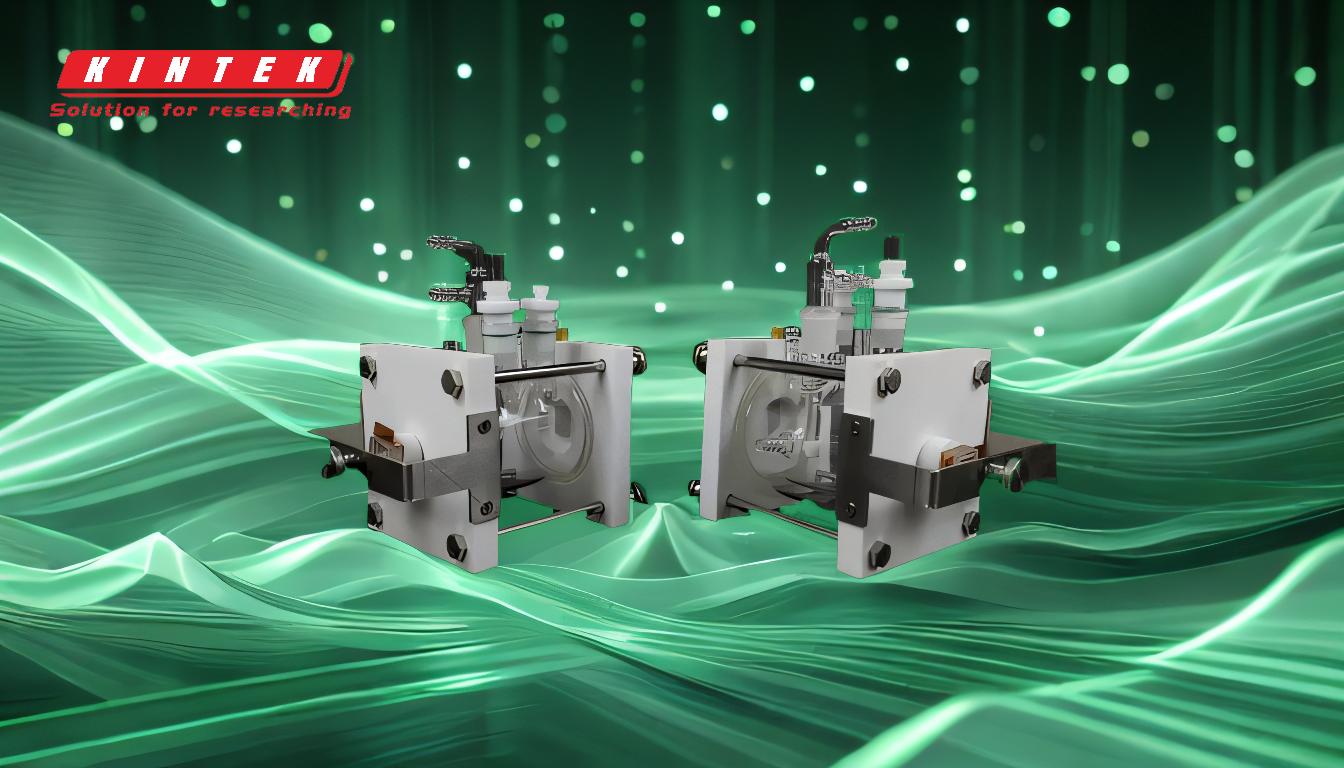
-
Types of Catalysts Used in Plastic Pyrolysis
- Zeolites: Zeolites are microporous, aluminosilicate minerals commonly used as catalysts in plastic pyrolysis. They are effective in cracking long-chain hydrocarbons into shorter, more valuable molecules like gasoline and diesel. Their high surface area and acidity make them ideal for promoting chemical reactions.
- Metal Oxides: Metal oxides such as alumina (Al₂O₃), silica (SiO₂), and magnesium oxide (MgO) are widely used due to their ability to stabilize the pyrolysis process and improve the yield of liquid fuels. They also help reduce the formation of unwanted byproducts.
- Acid Catalysts: Acid catalysts like sulfuric acid (H₂SO₄) and phosphoric acid (H₃PO₄) are used to enhance the breakdown of plastic polymers. They are particularly effective in increasing the yield of liquid hydrocarbons.
- Base Catalysts: Base catalysts such as sodium hydroxide (NaOH) and potassium hydroxide (KOH) are used to promote dechlorination reactions, which are crucial when processing chlorinated plastics like PVC.
- Transition Metal Catalysts: Metals like nickel (Ni), cobalt (Co), and iron (Fe) are used to improve the selectivity of the pyrolysis process, favoring the production of specific products like aromatics or olefins.
-
Role of Catalysts in Plastic Pyrolysis
- Enhancing Reaction Rates: Catalysts lower the activation energy required for the pyrolysis reactions, making the process faster and more efficient.
- Improving Product Quality: By selectively breaking down plastic polymers, catalysts help produce higher-quality liquid fuels with fewer impurities.
- Reducing Energy Requirements: Catalysts allow the pyrolysis process to occur at lower temperatures, reducing energy consumption and operational costs.
- Controlling Product Distribution: Catalysts can influence the types of products formed, such as increasing the yield of liquid fuels or reducing the formation of char and gas.
-
Impact of Catalyst Properties on Pyrolysis
- Surface Area and Porosity: Catalysts with high surface areas and porous structures provide more active sites for reactions, leading to better performance.
- Acidity and Basicity: The acidity or basicity of a catalyst determines its ability to break specific chemical bonds, influencing the composition of the pyrolysis products.
- Thermal Stability: Catalysts must withstand high temperatures without degrading to ensure consistent performance throughout the pyrolysis process.
-
Factors Influencing Catalyst Selection
- Type of Plastic: Different plastics require different catalysts. For example, polyethylene (PE) and polypropylene (PP) benefit from zeolites, while PVC requires base catalysts for dechlorination.
- Desired Products: The choice of catalyst depends on the target products. For instance, zeolites are preferred for producing liquid fuels, while metal oxides are better for stabilizing the process.
- Process Conditions: Temperature, pressure, and residence time influence the effectiveness of catalysts. Some catalysts perform better under specific conditions.
-
Challenges and Considerations
- Catalyst Deactivation: Catalysts can become deactivated due to coke formation or poisoning by impurities in the plastic feedstock. Regular regeneration or replacement is necessary.
- Cost and Availability: The cost and availability of catalysts can impact the economic feasibility of the pyrolysis process.
- Environmental Impact: Some catalysts, particularly acid and base catalysts, can pose environmental risks if not handled properly.
-
Future Trends in Catalyst Development
- Nanocatalysts: The use of nanocatalysts is gaining attention due to their high surface area and reactivity, which can further enhance pyrolysis efficiency.
- Bifunctional Catalysts: Catalysts with both acidic and basic properties are being developed to handle mixed plastic waste more effectively.
- Sustainable Catalysts: Research is focusing on developing eco-friendly catalysts that are less harmful to the environment and easier to recycle.
By understanding the role and impact of catalysts in plastic pyrolysis, stakeholders can optimize the process to achieve higher yields, better product quality, and lower environmental impact. The choice of catalyst is a critical decision that depends on the type of plastic, desired products, and process conditions. Future advancements in catalyst technology are expected to further improve the efficiency and sustainability of plastic pyrolysis.
Summary Table:
Catalyst Type | Role in Pyrolysis | Key Benefits |
---|---|---|
Zeolites | Cracks long-chain hydrocarbons into shorter, valuable molecules like gasoline/diesel | High surface area, acidity, and improved product quality |
Metal Oxides | Stabilizes pyrolysis, improves liquid fuel yield, reduces byproducts | Effective for stabilizing reactions and enhancing fuel production |
Acid Catalysts | Enhances breakdown of plastic polymers, increases liquid hydrocarbon yield | Effective for increasing liquid fuel output |
Base Catalysts | Promotes dechlorination, essential for processing chlorinated plastics (e.g., PVC) | Reduces harmful chlorine content in products |
Transition Metals | Improves selectivity, favors production of specific products like aromatics/olefins | Enhances product specificity and process efficiency |
Ready to optimize your plastic pyrolysis process? Contact our experts today to learn more about the right catalysts for your needs!