Biomass conversion involves the transformation of organic materials into valuable products such as biofuels, chemicals, and gases. Catalysts play a crucial role in enhancing the efficiency and selectivity of these processes. Common catalysts include zeolites, clay minerals, metal-based catalysts like Ni-dolomite, and biochar-based catalysts. These catalysts are tailored to specific reactions, such as cracking heavy hydrocarbons, producing hydrogen, or generating furfural compounds. The choice of catalyst depends on the type of biomass, desired end products, and process conditions. This answer explores the key catalysts used in biomass conversion, their roles, and their applications in various processes.
Key Points Explained:
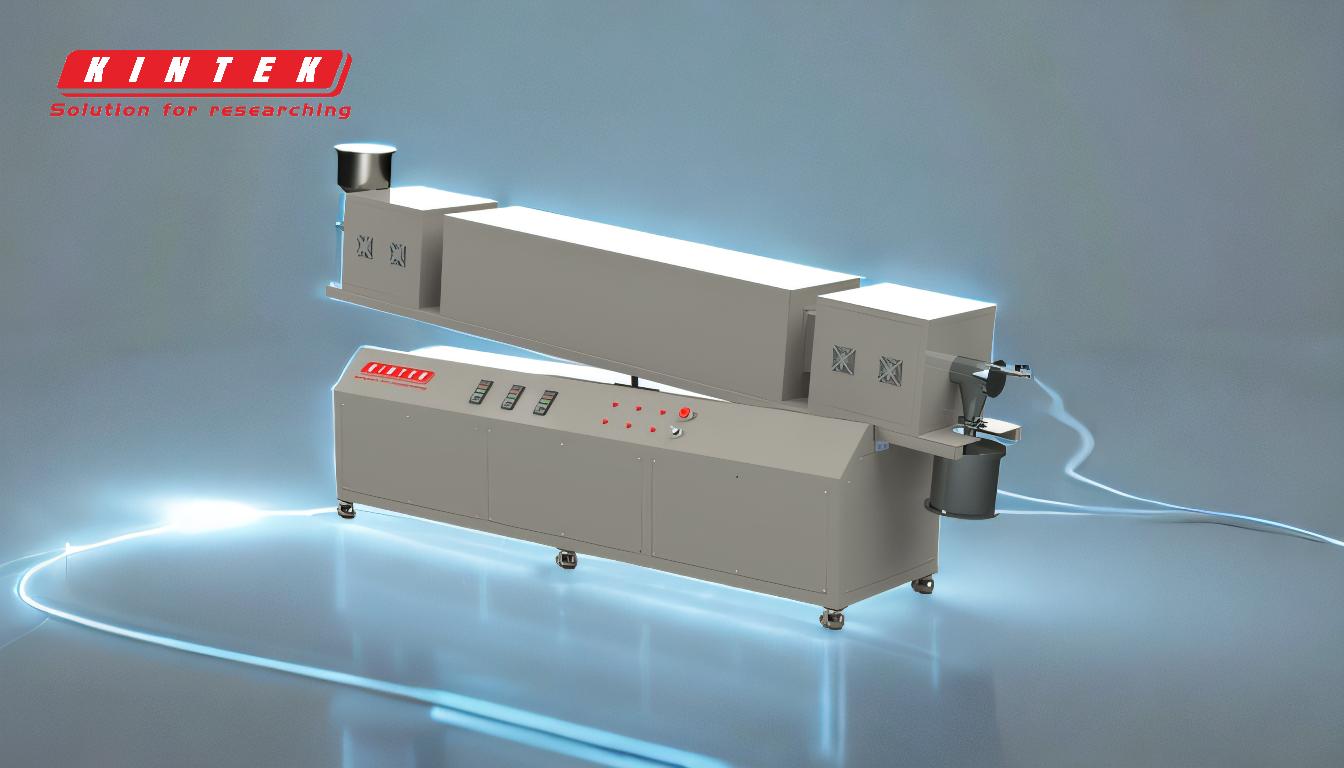
-
Zeolites and Clay Minerals:
- Composition: Zeolites are porous materials made of aluminum and silicon oxides, while clay minerals like kaolin are naturally occurring aluminosilicates.
- Function: These catalysts selectively crack heavy hydrocarbons and condense light hydrocarbons during biomass conversion.
- Applications: They are used to produce C1, C2, and C3 hydrocarbons (e.g., methane, ethane, propane) from biomass.
- Advantages: Their porous structure provides high surface area and selectivity, making them effective for specific hydrocarbon production.
-
Ni-Dolomite Catalysts:
- Composition: These catalysts consist of nickel (Ni) supported on dolomite, a calcium magnesium carbonate mineral.
- Function: Ni-dolomite is particularly effective for hydrogen production from biomass.
- Applications: Studies have shown that 10 wt% Ni-dolomite is optimal for hydrogen production, with rice husk yielding the highest hydrogen output.
- Advantages: The nickel component enhances catalytic activity, while dolomite provides stability and support.
-
Titanium and Metal Nitride Catalysts:
- Composition: These include titanium compounds (e.g., TiN) and metal nitrides (e.g., GaN).
- Function: They promote the production of furfural compounds during biomass fast pyrolysis.
- Applications: Used in processes aimed at converting biomass into furfural, a valuable chemical intermediate.
- Advantages: These catalysts are highly effective in selective furfural production, improving process efficiency.
-
Biochar-Based Catalysts:
- Composition: Derived from the pyrolysis of biomass, biochar is a carbon-rich material.
- Function: Biochar-based catalysts enhance desirable chemical reactions during pyrolysis, improving the yield of biofuels and chemicals.
- Applications: Used in pyrolysis processes to convert biomass into biofuels and other valuable products.
- Advantages: Biochar is sustainable and cost-effective, as it is derived from biomass itself.
-
Factors Influencing Catalyst Selection:
- Biomass Type: The composition of the biomass (e.g., lignin, cellulose, hemicellulose) influences the choice of catalyst.
- Desired End Products: Catalysts are selected based on the target products, such as hydrocarbons, hydrogen, or furfural.
- Process Conditions: Temperature, pressure, and reaction environment (e.g., pyrolysis, gasification) dictate the suitability of specific catalysts.
-
Emerging Trends in Catalyst Development:
- Sustainability: There is a growing focus on developing catalysts from renewable or waste-derived materials, such as biochar.
- Selectivity: Advances in catalyst design aim to improve selectivity for specific products, reducing unwanted byproducts.
- Durability: Research is ongoing to enhance catalyst stability and longevity, reducing the need for frequent replacement.
By understanding the roles and applications of these catalysts, stakeholders in biomass conversion can optimize processes to achieve higher yields and more valuable products. The choice of catalyst is critical and should align with the specific goals of the conversion process.
Summary Table:
Catalyst | Composition | Function | Applications | Advantages |
---|---|---|---|---|
Zeolites & Clays | Aluminum, silicon oxides, aluminosilicates | Cracks heavy hydrocarbons, condenses light hydrocarbons | Produces C1, C2, C3 hydrocarbons (e.g., methane, ethane, propane) | High surface area, selectivity for specific hydrocarbons |
Ni-Dolomite | Nickel supported on dolomite | Optimizes hydrogen production | 10 wt% Ni-dolomite for highest hydrogen yield (e.g., rice husk) | Enhanced catalytic activity, stability, and support |
Titanium & Nitrides | Titanium compounds (e.g., TiN, GaN) | Promotes furfural production | Biomass fast pyrolysis for furfural compounds | High selectivity for furfural, improves process efficiency |
Biochar-Based | Carbon-rich material from biomass pyrolysis | Enhances desirable reactions during pyrolysis | Biofuel and chemical production from biomass | Sustainable, cost-effective, derived from biomass |
Optimize your biomass conversion process with the right catalysts—contact our experts today!