Chemical vapor deposition (CVD) is a versatile thin-film deposition technique widely used in nanotechnology and materials science. Catalysts play a crucial role in CVD processes by facilitating the decomposition of precursor gases and promoting the formation of desired thin films or nanostructures. The choice of catalyst depends on the material being deposited, the substrate, and the specific application. Common catalysts include transition metals like nickel, iron, and cobalt, which are particularly effective for growing carbon-based materials such as graphene and carbon nanotubes. These catalysts lower the activation energy required for chemical reactions, enabling precise control over film properties and morphology.
Key Points Explained:
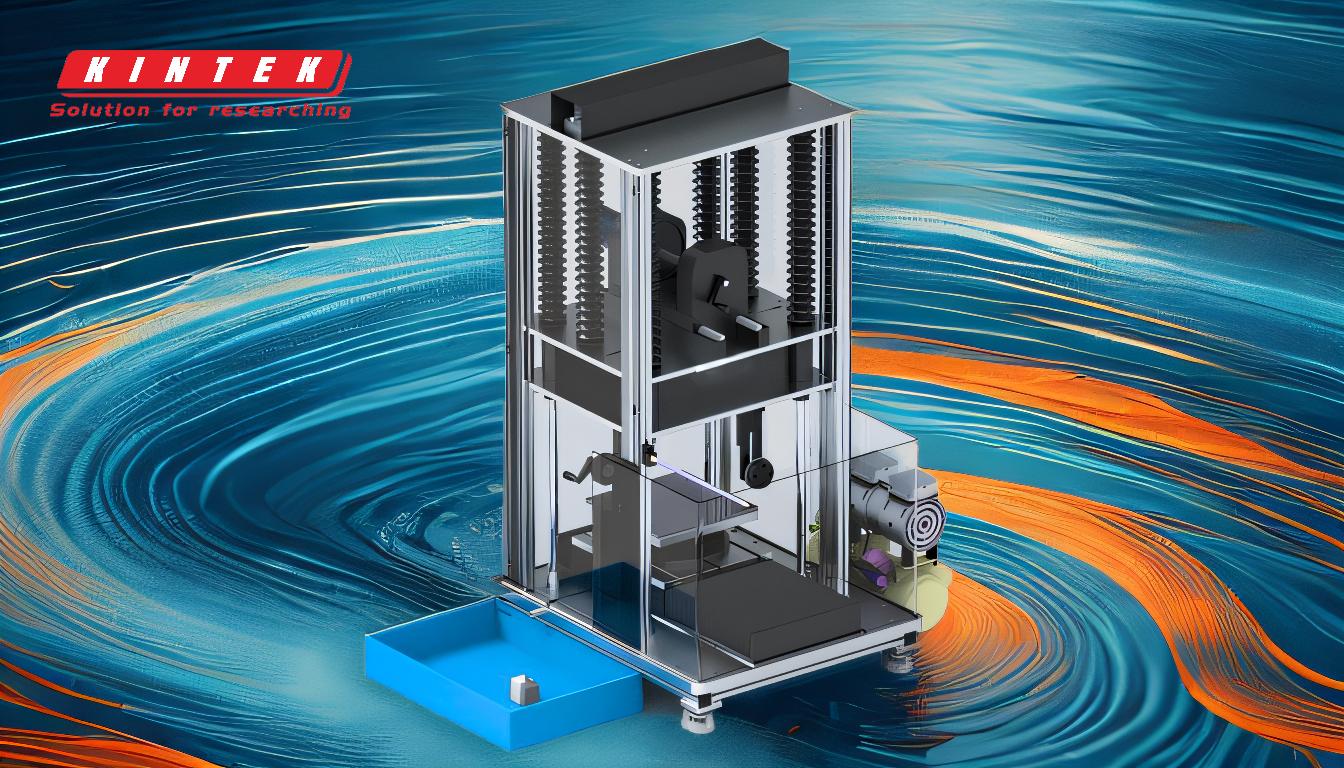
-
Role of Catalysts in CVD:
- Catalysts in CVD processes are essential for controlling the chemical reactions that lead to thin-film deposition. They lower the activation energy required for precursor decomposition and promote the formation of specific materials, such as graphene or carbon nanotubes.
- For example, in the growth of graphene, catalysts like nickel allow carbon atoms to dissolve and then precipitate during cooling, forming high-quality graphene layers.
-
Common Catalysts Used in CVD:
- Transition Metals: Nickel, iron, and cobalt are widely used due to their ability to dissolve carbon and facilitate its reorganization into desired structures. These metals are particularly effective for growing carbon-based nanomaterials.
- Noble Metals: Gold and platinum are used in specialized applications where high stability and resistance to oxidation are required.
- Metal Oxides: Certain metal oxides, such as copper oxide, are used for depositing oxides and other inorganic materials.
-
Catalyst Selection Criteria:
- Substrate Compatibility: The catalyst must be compatible with the substrate material to ensure proper adhesion and film quality.
- Thermal Stability: The catalyst should remain stable at the high temperatures typically used in CVD processes.
- Reaction Specificity: The catalyst should selectively promote the desired chemical reactions while minimizing unwanted by-products.
-
Impact of Catalysts on Film Properties:
- Catalysts influence the morphology, thickness, and crystallinity of the deposited films. For instance, the choice of catalyst can determine whether graphene forms as a single layer or multiple layers.
- The catalyst also affects the uniformity and defect density of the deposited material, which are critical for applications in electronics and nanotechnology.
-
Challenges and Considerations:
- Catalyst Contamination: Residual catalyst particles can remain on the deposited film, potentially affecting its properties. Post-deposition cleaning processes are often required.
- Catalyst Lifespan: Catalysts may degrade over time due to high temperatures or chemical reactions, necessitating periodic replacement or regeneration.
- Cost and Availability: Some catalysts, such as noble metals, can be expensive or scarce, influencing the overall cost-effectiveness of the CVD process.
-
Applications of Catalysts in CVD:
- Graphene Growth: Nickel and copper are commonly used to grow high-quality graphene for electronic and optoelectronic applications.
- Carbon Nanotube Synthesis: Iron and cobalt catalysts are widely used to produce carbon nanotubes with controlled diameters and lengths.
- Magnetic Coatings: Catalysts are used to deposit magnetic thin films for data storage devices, such as hard drives.
By carefully selecting and optimizing catalysts, CVD processes can achieve precise control over material properties, enabling advancements in nanotechnology, electronics, and materials science.
Summary Table:
Catalyst Type | Examples | Applications |
---|---|---|
Transition Metals | Nickel, Iron, Cobalt | Graphene growth, carbon nanotube synthesis |
Noble Metals | Gold, Platinum | High-stability applications, oxidation resistance |
Metal Oxides | Copper Oxide | Deposition of oxides and inorganic materials |
Selection Criteria | Substrate compatibility, thermal stability, reaction specificity | Ensures optimal film quality and performance |
Need help selecting the right catalyst for your CVD process? Contact our experts today!