Chemical vapor deposition (CVD) is a widely used technique for the synthesis of single-walled carbon nanotubes (SWCNTs), and the choice of catalyst plays a critical role in determining the quality, yield, and properties of the nanotubes. Catalysts are essential for initiating and controlling the growth of SWCNTs during the CVD process. Commonly used catalysts include transition metals such as iron (Fe), cobalt (Co), nickel (Ni), and molybdenum (Mo), often supported on substrates like silica or alumina. These catalysts facilitate the decomposition of carbon-containing precursors and guide the formation of SWCNTs. The selection of catalysts and their preparation methods significantly influence the diameter, chirality, and structural uniformity of the nanotubes.
Key Points Explained:
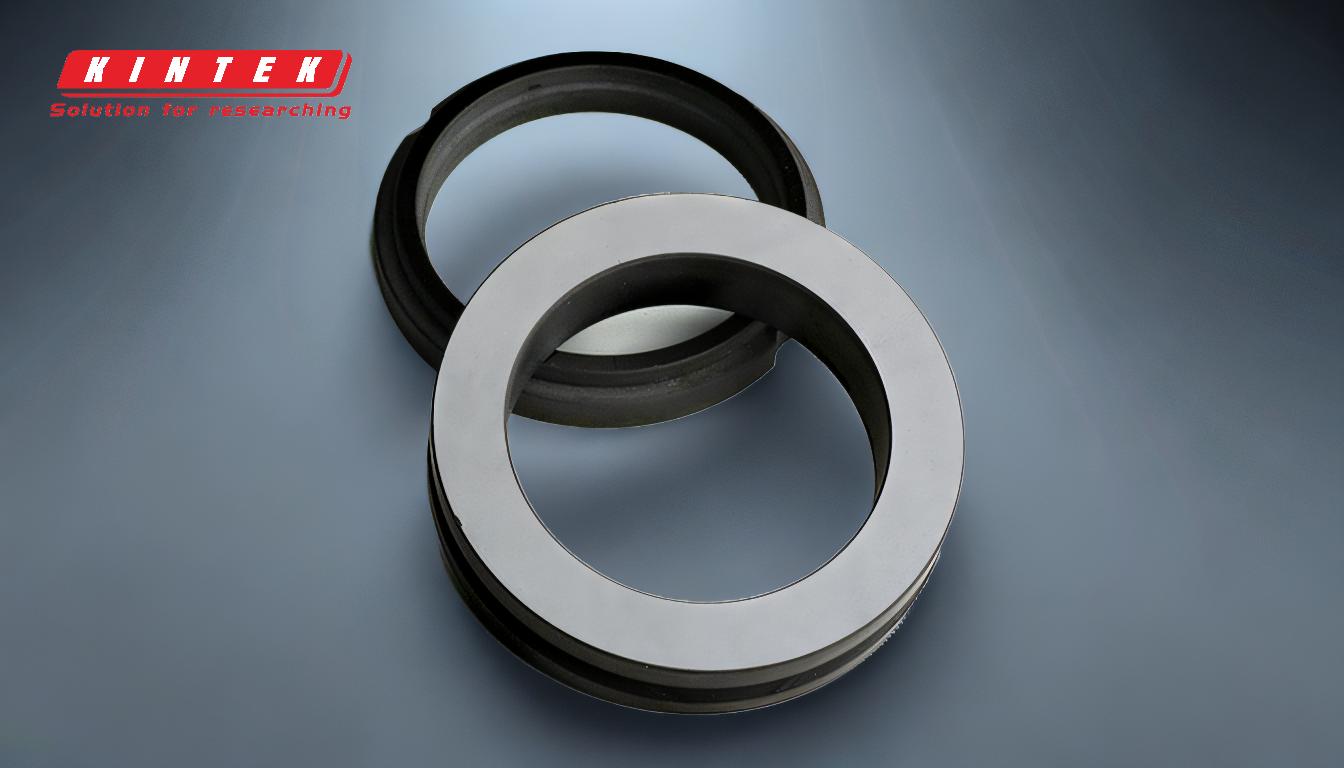
-
Role of Catalysts in CVD for SWCNT Growth:
- Catalysts are crucial for initiating the decomposition of carbon-containing precursors (e.g., methane, ethylene, or acetylene) and promoting the nucleation and growth of SWCNTs.
- They act as active sites where carbon atoms assemble into hexagonal structures, forming the cylindrical walls of SWCNTs.
-
Common Transition Metal Catalysts:
- Iron (Fe): Widely used due to its high activity and ability to produce high-quality SWCNTs. Iron nanoparticles are often supported on substrates like silica or alumina.
- Cobalt (Co): Known for producing SWCNTs with controlled diameters and chirality. Cobalt catalysts are often used in combination with other metals to enhance performance.
- Nickel (Ni): Effective for SWCNT growth, particularly in low-temperature CVD processes. Nickel catalysts are also used in bimetallic systems to improve yield and quality.
- Molybdenum (Mo): Often used as a co-catalyst with other transition metals to control the diameter and chirality of SWCNTs.
-
Catalyst Preparation and Support Materials:
- Catalysts are typically prepared as nanoparticles to provide a high surface area for carbon precursor decomposition.
- Support materials like silica (SiO₂), alumina (Al₂O₃), or magnesium oxide (MgO) are used to stabilize the catalyst nanoparticles and prevent aggregation during the CVD process.
- The choice of support material can influence the dispersion and activity of the catalyst, affecting the growth of SWCNTs.
-
Bimetallic and Alloy Catalysts:
- Bimetallic catalysts, such as Fe-Co, Fe-Ni, or Co-Mo, are often used to enhance the catalytic activity and control the properties of SWCNTs.
- These combinations can improve the yield, reduce defects, and enable better control over the chirality and diameter of the nanotubes.
-
Influence of Catalyst Size and Morphology:
- The size of the catalyst nanoparticles directly affects the diameter of the SWCNTs. Smaller nanoparticles produce narrower nanotubes, while larger particles result in wider tubes.
- The morphology of the catalyst, such as its shape and crystallinity, also plays a role in determining the structural properties of the SWCNTs.
-
Catalyst Deactivation and Regeneration:
- Over time, catalysts can become deactivated due to carbon encapsulation or poisoning by impurities in the gas phase.
- Regeneration techniques, such as oxidation or reduction treatments, can restore the activity of the catalyst for repeated use.
-
Advances in Catalyst Design:
- Recent research focuses on developing novel catalysts, such as single-atom catalysts or catalysts with tailored surface properties, to achieve better control over SWCNT growth.
- Advances in catalyst design aim to improve the selectivity for specific chiralities and reduce the production of defective nanotubes.
In summary, the choice and preparation of catalysts are critical factors in the CVD synthesis of SWCNTs. Transition metals like Fe, Co, Ni, and Mo, often supported on substrates or used in bimetallic systems, are commonly employed to achieve high-quality SWCNTs with controlled properties. Advances in catalyst design continue to drive improvements in the efficiency and precision of SWCNT production.
Summary Table:
Catalyst | Key Properties | Role in SWCNT Growth |
---|---|---|
Iron (Fe) | High activity, high-quality SWCNTs | Initiates decomposition of carbon precursors |
Cobalt (Co) | Controlled diameter and chirality | Enhances SWCNT structure and performance |
Nickel (Ni) | Effective in low-temperature CVD | Improves yield and quality in bimetallic systems |
Molybdenum (Mo) | Controls diameter and chirality | Often used as a co-catalyst |
Bimetallic (e.g., Fe-Co, Fe-Ni) | Enhanced activity and control | Improves yield and reduces defects |
Need help selecting the right catalyst for your SWCNT synthesis? Contact our experts today for tailored solutions!