Plastic pyrolysis, while a promising technology for sustainable waste management and resource recovery, faces several significant challenges. These include high energy consumption, difficulties in controlling the process and product quality, high capital and operational costs, and challenges related to feedstock variability and reactor design. Additionally, issues such as metal and ash accumulation, inefficient separation of end products, and the production of toxic by-products further complicate the process. Addressing these challenges is crucial for improving the efficiency, scalability, and economic viability of plastic pyrolysis.
Key Points Explained:
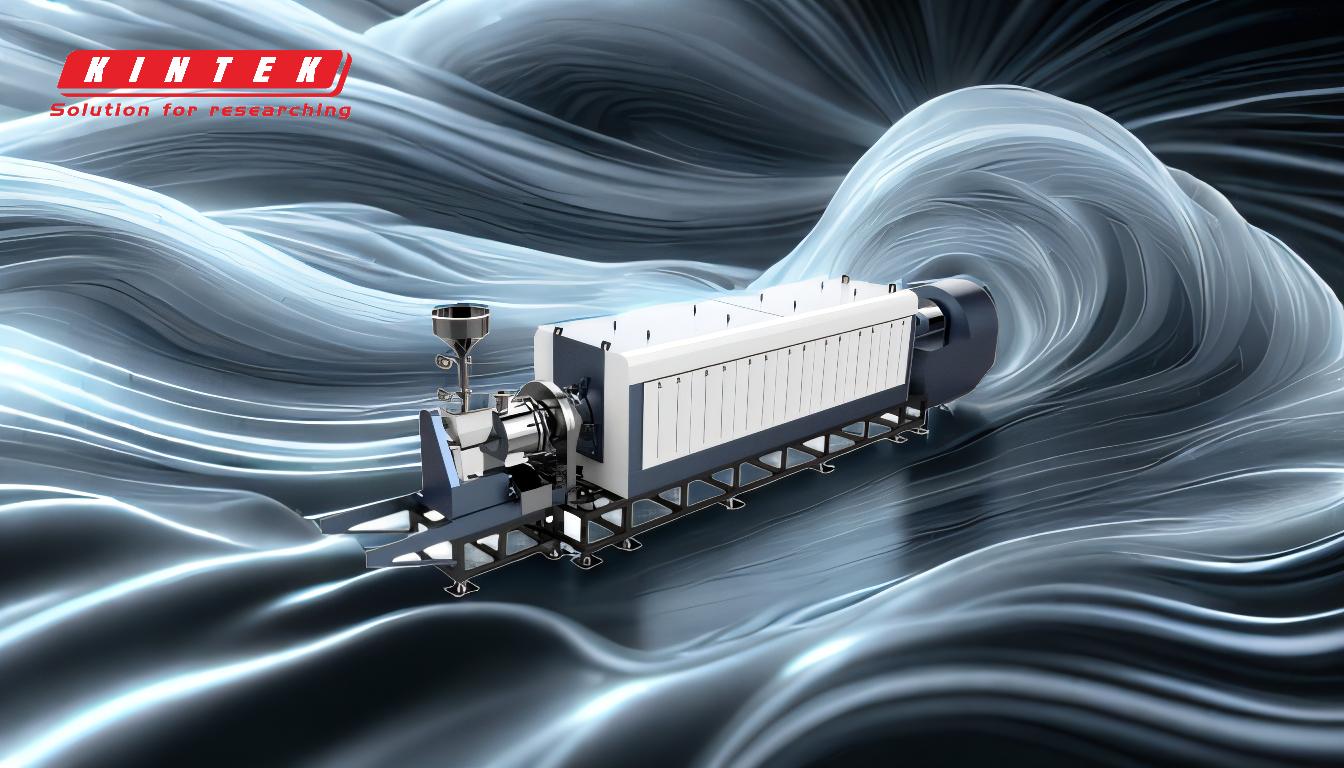
-
High Energy Consumption and Process Control:
- Plastic pyrolysis is an energy-intensive process that requires specific conditions to operate efficiently. Maintaining consistent temperatures throughout the feedstock is challenging due to the poor heat conductivity of organic materials. This uneven heating can lead to incomplete pyrolysis or undesirable by-products.
- Controlling the types of decomposition products is difficult, especially in high-temperature pyrolysis, which often results in toxic by-products. This makes the process less environmentally friendly and complicates the recovery of useful products.
-
Feedstock Variability and Logistics:
- The quality and composition of plastic waste (feedstock) can vary significantly, especially when dealing with mixed municipal solid waste (MSW). This variability affects the consistency of the pyrolysis process and the quality of the end products.
- Efficient feedstock logistics, including collection, sorting, and preprocessing, are critical but challenging to implement, particularly for large-scale operations.
-
Reactor Design and Operational Challenges:
- Reactor designs need improvement to enhance heat transfer, reduce parasitic energy losses, and handle the sticky nature of heated plastics and rubber. Accumulation of metals and ash in reactor beds can impede the process and reduce bio-oil yields.
- Continuous processing, which is essential for economic viability, is difficult to achieve due to the uneven heating and movement of materials within the reactor.
-
High Capital and Operational Costs:
- The equipment required for pyrolysis, including reactors, monitoring systems, and separation units, is expensive. This high capital cost is a significant barrier to widespread adoption.
- Operational costs are also high due to the need for sophisticated monitoring and auto-adjusting systems to maintain optimal process conditions.
-
Separation and Purification of End Products:
- Efficient separation and purification of pyrolysis products (bio-oil, bio-char, and syngas) are critical for their commercial use. However, achieving this efficiency is technically challenging and adds to the overall cost of the process.
- The presence of impurities and toxic by-products further complicates the purification process, reducing the economic value of the end products.
-
Environmental and Safety Concerns:
- The production of toxic by-products during pyrolysis poses environmental and safety risks. Proper handling and disposal of these by-products are necessary to minimize their impact.
- The process also generates emissions that need to be controlled to meet environmental regulations.
-
Limited Global Adoption and Scalability:
- Despite its potential, pyrolysis technology has seen limited global adoption due to the challenges mentioned above. Scaling up the process for real-world applications remains a significant hurdle.
- The lack of standardized processes and regulatory frameworks further hinders the widespread implementation of pyrolysis technology.
In conclusion, while plastic pyrolysis offers a promising solution for waste management and resource recovery, addressing its technical, economic, and environmental challenges is essential for its successful implementation and scalability. Improvements in reactor design, process control, feedstock handling, and product purification are key areas that require further research and development.
Summary Table:
Challenge | Description |
---|---|
High Energy Consumption | Requires consistent temperatures; uneven heating leads to incomplete pyrolysis. |
Feedstock Variability | Mixed plastic waste affects process consistency and product quality. |
Reactor Design Issues | Poor heat transfer, metal/ash accumulation, and sticky materials impede yields. |
High Capital & Operational Costs | Expensive equipment and monitoring systems increase adoption barriers. |
Product Separation Challenges | Efficient purification of bio-oil, bio-char, and syngas is technically difficult. |
Environmental & Safety Concerns | Toxic by-products and emissions require proper handling and regulation. |
Limited Global Adoption | Scaling up and standardizing processes remain significant hurdles. |
Interested in overcoming the challenges of plastic pyrolysis? Contact our experts today to explore innovative solutions!