Dental ceramics, commonly used in restorative dentistry, are composed of inorganic, non-metallic materials primarily derived from clay and minerals. The primary component is kaolin, a type of clay, which constitutes about 60% of the material. The remaining 40% includes additives such as feldspar, quartz, and oxides, each contributing specific properties like color, hardness, and durability. These materials are mixed and fired at high temperatures to create strong, aesthetically pleasing dental restorations. Dental ceramics are brittle, with high compressive strength but low tensile strength, making them prone to fracture under strain. The choice of materials and their proportions can vary depending on the desired properties of the final product.
Key Points Explained:
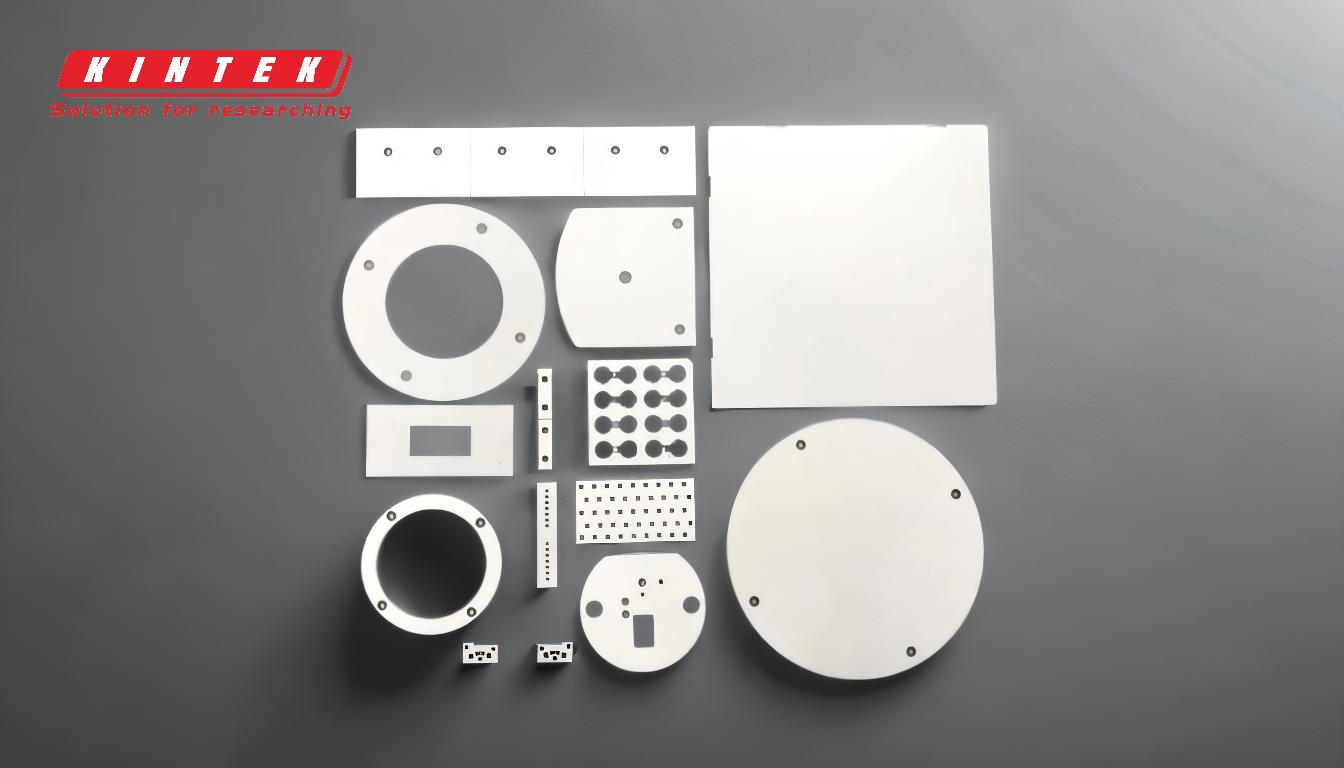
-
Primary Components of Dental Ceramics:
- Kaolin (Clay): Kaolin is the main component, making up about 60% of dental porcelain. It is a type of clay sourced from soil or salt mines. Kaolin provides the basic structure and plasticity needed for shaping the ceramic material before firing.
-
Minerals and Additives: The remaining 40% consists of various minerals and additives, each serving a specific purpose:
- Feldspar: Added to provide color and improve the melting properties during firing.
- Quartz: Incorporated to increase the hardness and strength of the ceramic.
- Oxides: Used to enhance durability and resistance to wear and tear.
-
Processing of Raw Materials:
- Clay Sourcing: Clay, primarily kaolin, is sourced directly from natural deposits in soil or salt mines. This raw material is then purified to remove impurities that could affect the quality of the final product.
- Mineral Processing: Minerals like feldspar and quartz often require chemical processing to achieve the desired purity and particle size. This processing ensures that these additives can effectively contribute to the properties of the dental ceramic.
-
Mixing and Firing:
- Mixing: The purified clay and processed minerals are mixed in precise proportions to create a homogeneous blend. This mixture is then shaped into the desired form, such as crowns, veneers, or inlays.
- Firing: The shaped material is fired at high temperatures, typically between 1,200°C and 1,400°C. This process vitrifies the material, transforming it into a hard, durable ceramic. The high temperatures also cause the feldspar to melt, binding the other components together and creating a glassy matrix.
-
Properties of Dental Ceramics:
- Brittleness: Dental ceramics are inherently brittle, meaning they have high compressive strength but low tensile strength. This makes them prone to cracking or fracturing under stress, particularly in areas subjected to bending or impact forces.
- Aesthetic Appeal: One of the key advantages of dental ceramics is their ability to mimic the natural appearance of teeth. The inclusion of feldspar and other colorants allows for a range of shades that can match the patient's natural tooth color.
- Biocompatibility: Dental ceramics are biocompatible, meaning they are well-tolerated by the body and do not cause adverse reactions. This makes them suitable for long-term use in the oral environment.
-
Types of Dental Ceramics:
- Monolithic Ceramics: These are single-layer ceramics that provide a balance of strength and aesthetics. They are often used for full-contour restorations.
- Press to Metal (PFM): In this type, a ceramic layer is pressed onto a metal substrate. This combination provides the strength of metal with the aesthetic benefits of ceramic.
- Press to Zirconia: Similar to PFM, but with a zirconia substrate instead of metal. Zirconia offers superior strength and is often used in areas requiring high durability.
-
Applications in Dentistry:
- Crowns and Bridges: Dental ceramics are commonly used for crowns and bridges due to their strength and ability to match natural tooth color.
- Veneers: Thin layers of ceramic are used to cover the front surface of teeth, improving their appearance and protecting the underlying tooth structure.
- Inlays and Onlays: These are used to restore damaged or decayed teeth, providing a durable and aesthetically pleasing solution.
In summary, dental ceramics are composed of a blend of kaolin and various minerals, each contributing to the material's strength, durability, and aesthetic properties. The materials are carefully processed, mixed, and fired at high temperatures to create restorations that are both functional and visually appealing. Despite their brittleness, dental ceramics are widely used in restorative dentistry due to their biocompatibility and ability to closely mimic natural teeth.
Summary Table:
Component | Percentage | Role |
---|---|---|
Kaolin (Clay) | 60% | Provides structure and plasticity for shaping |
Feldspar | Part of 40% | Adds color and improves melting properties during firing |
Quartz | Part of 40% | Increases hardness and strength |
Oxides | Part of 40% | Enhances durability and resistance to wear |
Firing Temp. | 1,200°C-1,400°C | Vitrifies material, creating a hard, durable ceramic |
Key Properties | - | Brittle, high compressive strength, biocompatible, aesthetically pleasing |
Interested in learning more about dental ceramics? Contact our experts today for personalized advice!